EV Battery Manufacturing: Defining The Future From 2025 Onwards
Explore the challenges and opportunities in EV battery production, from supply chain disruptions to quality management. Learn how innovations, recycling, and new chemistries can drive sustainable growth in the battery industry amid evolving regulations and market shifts.
With EV sales gaining traction worldwide, it is clear that the transition of technology and energy is finally taking center stage. This rising support for EVs is crescendoing the inclinations towards stationary energy storage solutions, i.e., the battery industry. The global battery market has been ascending steadily and is expected to cross $490 billion by the end of this decade. Spurring EV sales is just one of the drivers, but it will escalate further by integrating new mobility concepts like advanced air mobility and micro-mobility.
However, the present selection of batteries is plagued by an array of technological, commercial, and sustainability challenges. The concerning regulatory frameworks are still in the juvenile stage, which means that with time, they will tighten up to address all aforementioned concerns. Therefore, OEMs, battery producers, and manufacturers need to proactively strategize their innovation, product design, and assembly processes to prevent any non-compliance in the coming years.
Stellarix's mobility strategy consulting team thinks industry players need to carefully assess these challenges to recognize the hidden opportunities in them. This perspective summarizes some key points on both fronts and gives decision-makers something to consider.
Opportunities Paired With Challenges In High-Quality EV Batteries Upscaled Production
Supply Chain Disruptions
Challenge: The global supply chain for batteries is in a complex and fragile state. The quest for sustainable and accessible raw materials is still a daunting task, primarily due to the reliance on metals like nickel, cobalt, and lithium. It is a costly, ethically challenged, and polluting process, contradicting the sustainability claims of vehicle electrification. Several research efforts are directed at finding alternatives to lithium, and some are even being applied commercially. But their mass-scale feasibility is yet to be proven. However, tightening regulations and government policies adds pressure to these strained supply chains. These factors are leading to bottlenecks impacting the upscaling of production.
Opportunity: The battery industry's success relies heavily on scaling production. Companies that build expertise and strategically invest in the proper production tools will gain a competitive advantage in the long term. Regarding raw material scarcity, several new chemistries are emerging to meet the rising demand for increased power and capacity of solid-state batteries. Battery recycling is also a growing space that industry participants may leverage to facilitate a circular economy and better revenues.
Market Volatility
Challenge: The battery manufacturers need to ensure on-time delivery of batteries with sufficient volumes. Russian sanctions and the intensifying trade war between the West and China are increasing the investment risks in EV battery technologies and production. The growing shift towards EVs is also changing the structure of the automotive market, where batteries are now making for a higher share of the vehicle's value. It changes the interaction and relationships between industry players and the value they may derive from EVs.
Opportunity: The evolving battery chemistries present a fantastic opportunity for companies to reduce costs and reliance on traditional raw materials. They are also a way for OEMs, manufacturers, and recyclers to combat market uncertainties in the near future.
Battery Quality Management At Scale
Challenge: Battery quality management is fundamentally defined by the complex nature of battery performance. The most vulnerable and interdependent parts of all electrochemical batteries' performance are their lifetime and failure. Performance degradation over time, longer timelines of electrochemical lifetime testing, functional failure, and battery safety are key bottlenecks in the quality management of EV batteries.
Opportunity: Battery manufacturers and producers need to overcome the inevitability, severity, and frequency of the abovementioned issues with quality. However, quality control is tricky, and difficult choices must be made. Automotive strategy consulting experts suggest some essential pathways to improve quality management at scale. They could start by expanding the specification limits, shifting the population mean, tightening the distribution of a process parameter, or improving inspection or defect detection techniques during production. These approaches will improve the production process's overall efficiency and help control costs that are a significant roadblock in the broader adoption of EVs.
Final Word
The need for global-scale battery production has never been greater. Nevertheless, producing a standard-quality battery is a challenging endeavor involving huge environmental, reputational, financial, and human stakes. Yet battery quality is often overlooked in contrast to the ongoing mobility electrification efforts. Improving battery quality could address some significant challenges with the present selection of EV batteries, like performance degradation over time.
Therefore, both OEMs and cell producers need to pay attention to this aspect during the product design and development phase. The industry has a long road ahead. Still, small steps like standardizing battery failure modes, conducting comprehensive tests for every failure, increasing modeling tools, and improving battery characterization techniques could lead to massively high-quality battery manufacturing. Lastly, the industry also needs to work on preventing counterfeited products and low-quality cells and developing safety and quality certifications.
Featured Product
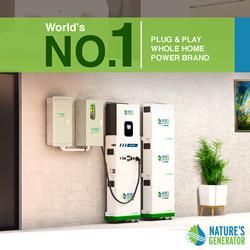