Experts from two industry-leading electronics companies Molex and DigiKey—shed light on the current state of the electrification movement and key considerations for the future of the automotive industry.
Automotive Electrification Movement

Matt McWhinney, group business development manager, and Kirk Ulery, distribution business development manager, at Molex; Shawn Luke, technical marketing engineer | DigiKey
The automotive industry's evolution through electrification—replacing traditional mechanically driven systems with electric components and systems—is profoundly changing the design of today’s vehicles, which range widely from internal combustion engines to mild hybrids to fully electric architectures.
As systems have evolved from carburetors and simple exhaust systems to precision fuel injectors, emission systems, and traction and braking control systems, similar advancements have been made in electrification with new architectures, components for electric motors, battery packs and advanced power electronics. Combined, these advancements are pushing engineers to reimagine how vehicles are designed and driven for maximum efficiency, reliability and safety.
Experts from two industry-leading electronics companies—Matt McWhinney and Kirk Ulery, business development managers at Molex and Shawn Luke, technical marketing manager at DigiKey—shed light on the current state of the electrification movement and key considerations for the future of the automotive industry.
Vehicle model landscape
While the highly watched demand for EV and hybrid vehicles continues to increase, sales of new EV vehicles have slowed over the last several months due to many factors, including market and public policy. Industry experts cite cost and the limited charging infrastructure in the U.S. as two major reasons.
“We’ve had fits and starts on electrification in North America,” Ulery said. “If you’re going more than 100 miles at a time, you know charging infrastructure needs to be addressed.”
Hybrid vehicles, on the other hand, are outpacing EV sales. According to Edmunds data, hybrid purchases in the U.S. saw their biggest surge in 2023, increasing from more than 750,000 sales in 2022 to tipping over 1 million sales in 2023.
Another emerging category is the mild hybrid, which uses a battery-powered electric motor to supplement gas or diesel usage. Most mild hybrids run on a 48V electrical system, which is a higher voltage than the electrical systems of a traditional combustion-engine vehicle. The 48V system powers components that are not reliant on the engine, enabling better operational efficiency.
Even with the fast pace of innovation in automotive design, gas-powered vehicles still rule the roadways. According to research by Edmunds, 82% of new vehicles sold today in the U.S. rely on gas. However, the electrification movement is well underway among traditional vehicles to the most advanced high-tech electric models.
Electrifying under the hood
Ulery notes, “One constant we’re seeing is a lot more electrification – mechanical systems are becoming electrified in all vehicles for many reasons – especially to drive efficiency.”
One example is stop-start technology, which turns off the engine when a vehicle stops and automatically restarts when the driver releases the brake or pushes the gas pedal. While this feature can put extra demand on some components, it aims to improve fuel efficiency and reduce greenhouse gas emissions.
Other examples of electrification under the hood are in radiator fans, power steering, HVAC systems and cooling pumps. All these systems used to be powered by belts off an internal combustion engine (ICE). Electric water pumps are replacing mechanical radiator pumps for more efficient performance, and the precise control with electrical cooling can extend the lifespan of these parts. If there is extended battery management, they also circulate coolant throughout a vehicle to regulate the temperature of the battery pack, electric motors and power electronics.
Switching to electric-powered modules such as power steering pumps makes the system no longer reliant on the engine, reducing parasitic loads and allowing for more available horsepower. Therefore, automakers can install smaller engines in some vehicles and retain the same driving performance while gaining efficiency benefits and outputting lower emissions.
“Electrification has opened the door to innovative new vehicle designs,” Luke notes. “Without the need to accommodate the ‘belt driven architecture’ with a traditional internal combustion engine, auto manufacturers have more flexibility in where to distribute batteries and charging ports, the ability to increase the amount of space for passengers or cargo, and more.”
Overall, the electrification movement is replacing traditional mechanical with precision electrically controlled systems that can be more efficient. Combined with advancements in software control, modern vehicles are cleaner, more energy efficient, and offer performance and sustainability for both passenger and commercial drivers.
Vehicle battery advancement
Over the last decade, vehicle manufacturers have switched from 12V to higher voltages, such as 24V (especially for commercial vehicles) and now to 48V batteries to increase power capability, reduce vehicle weight, improve acceleration and realize fuel savings.
Legislation in the U.S. and Europe has been laying the groundwork for emissions reduction in newly built vehicles. A combination of regulatory and market forces are behind the increasing shift to mild hybrid architectures, which include integrated starter generators; 48V is not only growing in mild hybrids but also seems likely to emerge in more ICE platforms.
The shift to 48V architecture involves more than just increasing the system voltage. It also requires a change in the electrical foundation. Feature-rich, higher-performance vehicles rely on lighter and smaller components that deliver the same electrical efficiency as a higher-density model.
Ulery says, “The common thing is that both 12V and 48V systems are moving traditional mechanical functions off a serpentine belt to a series of electric motors.” He shared an example of a heavy-duty pickup truck using mechanical energy for its power steering. In many vehicles, this function is becoming electrified. “The amount of energy needed for the power steering takes away from the engine’s horsepower, so by moving it to a separate electrical system, drivers can maintain more power through the drivetrain.”
The automotive industry’s move to higher voltage systems is a gradual one, given the significant impact on the design and manufacturing process. Each manufacturer's transition is on a different timeline based on their products, technical maturity and the requirements of the customers they serve. Plus, all are held to standards and design practices related to the technologies they will be using, including:
- ISO 21780 covers requirements and tests for the electric and electronic components in road vehicles equipped with an electrical system operating at a nominal voltage of 48V.
- The VDA Recommendation 320 is published and maintained by the ZVEI-German Electrical and Electronic Manufacturers’ Association. It covers a wide range of specifications and test requirements for electric and electronic components in motor vehicles to develop the 48V power supply.
Following the standard to achieve smart battery management is integral to the success of 48V architecture. With the right design process, automakers can avoid inefficient power storage, increased costs and potential safety risks to drivers.
Interconnection fundamentals to prioritize safety
With vehicles requiring more power than ever to support increasingly sophisticated electrical features, a reliable connector design for 48V systems relies on several fundamental factors to meet vehicle performance and safety standards.
McWhinney says, “Having electronics and the infrastructure – the interconnects to support your vehicle – is essential for safety.”
Since 48V systems operate at a higher voltage (than 12V), connectors and electrical systems must be built with robust materials and proper insulation for safe, reliable performance. This becomes even more important if the voltage is higher than 48V.
Connector failures can cause vehicle system malfunctions or safety hazards. To prevent disconnections, connectors should include locking mechanisms and strain relief, as well as regular inspections and maintenance checks.
“Safety and monitoring control of the electrical system is more important now than ever,” says McWhinney.
Maintaining signal quality is crucial for higher voltage applications. Poor signal integrity can precipitate malfunctions, so connectors must minimize signal loss and interference with shielded cables, as well as proper grounding and strategic placement. Addressing these considerations requires innovation and expertise, which is where advanced connector solutions come into play.
“It feels so much like table stakes, but it’s underrated how important the interconnect is in automotive design, especially for safety,” added Luke.
Keeping up with change and certification of parts
Meeting safety requirements is a top priority, but McWhinney notes that an additional challenge is the constant change in vehicle electrical system requirements, which pushes manufacturers to keep up and constantly revise connectors and other components.
Manufacturers can always refer to the US Council for Automotive Research (USCAR) to track performance requirements and carefully review and certify approved components for safe use in the automotive industry.
Components that adhere to USCAR/LV214 or similar qualifications are typically high-quality, rugged and reliable parts that can take a beating on the road without sacrificing performance. For example, Molex’s MX150 connector series offers components engineered for vehicles that face harsh environments and are durable against extreme temperatures, vibration and moisture.
Luke notes, “With more innovation opportunities in vehicle design, more vehicle manufacturers are embracing electrification practices. Because of the hyper-fast innovation cycle, there are few standard platforms in the space. However, the increased variety offers consumers more options, and we expect the cost of vehicles will likely decrease as technology advances and production ramps up.”
Considering commercial vehicles
While much has been said about passenger cars, everything discussed in this article has been going on much longer in the commercial vehicle (CV) space. Commercial vehicles quickly transitioned from 12 to 24-volt systems to power diesel and some electrical systems, which allowed them to have smaller starters in the past. There is also a long history of electric HVAC in CVs, especially in buses, construction and agriculture vehicles and heavy-duty trucking, among others.
Commercial vehicles are typically designed to help their owner/operator make money and, therefore, need to work reliably. The pressure for a CV to perform reliably is typically higher than that of passenger cars, so extra sealing and robustness are needed.
Whether designing for passenger or commercial vehicles, engineers today must consider numerous complex, power-hungry systems and features that not only meet consumer and commercial demand but are also highly efficient, durable and safe. Thankfully, technology suppliers are up for the challenge of creating the technology to solve these innovation issues.
While automotive engineers are transforming the future of transportation, suppliers like Molex and distributors like DigiKey are along for the ride, delivering high-quality components, services and expertise to enable this transformation to happen.
Matt McWhinney and Kirk Ulery are business development managers at Molex. As a leading global provider of connector solutions, Molex brings engineering excellence, trusted relationships, and an unparalleled commitment to quality and reliability to help customers across industries improve lives. Trusted for more than 80 years, Molex offers world-class design, manufacturing and a portfolio of 100,000+ innovative products.
Shawn Luke is a technical marketing engineer at DigiKey. DigiKey is both the leader and continuous innovator in the high service distribution of electronic components and automation products worldwide, providing more than 15.9 million components from over 3,000 quality name-brand manufacturers.
The content & opinions in this article are the author’s and do not necessarily represent the views of AltEnergyMag
Comments (0)
This post does not have any comments. Be the first to leave a comment below.
Featured Product
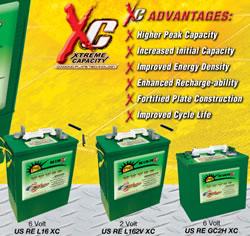