Erosion in wind turbine blades solved with the help of artificial intelligence
The erosion of materials used in wind turbine blades due to the effect of weather conditions is a problem that applies to the whole wind energy sector. VTT’s antiAGE project found a functional solution to the material problem with the help of artificial intelligence and 3D printing.
The erosion of materials used in wind turbine blades due to the effect of weather conditions is a problem that applies to the whole wind energy sector. VTT's antiAGE project found a functional solution to the material problem with the help of artificial intelligence and 3D printing.
"The blade material erodes due to the effect of rain, hailstones and sand dust, which significantly reduces the service life of wind turbines. Accelerated replacement of turbines becomes expensive: up to 2-4% of the value of all wind-generated power is lost as a result of this problem," says Principal Scientist Anssi Laukkanen from VTT.
"It is a question of a classic problem within this particular industry that costs billions of euros and brings additional costs to all wind energy. As wind turbine sizes increase and wind farms are placed out on the sea in increasingly demanding conditions, the significance of the problem becomes emphasised", says Laukkanen.
Artificial intelligence (AI) finds an optimal solution
In its antiAGE project, VTT modelled the material problem and set out to solve it virtually. This is the first time that AI was used for developing a material solution in this scale.
In principle, it is possible to find an unlimited number of different variations for the material used in wind turbine blades composed of the same material components but differing slightly from one another. Of all these alternatives, one would need to find the one that is best suited for this particular purpose and meets its operational requirements.
"Human perceptive skills are insufficient to visualise all the dimensions related to the optimisation of material solutions. AI, on the other hand, is capable of unravelling very complicated cause-and-effect relationships, simulating solutions and going through an infinite number of alternatives to find the one that works best in relation to the requirements set", Laukkanen points out.
3D printing brings flexibility to manufacturing
In principle, using AI, it would be possible to find a tailored material solution optimised for a specific purpose for every component of any single product. However, manufacturing of such highly tailored materials would be difficult if traditional manufacturing techniques were used.
3D printing, or additive manufacturing, offers an opportunity to produce the desired material in any shape without unreasonable costs. When applied like this, 3D printing will do exactly what it is supposed to do.
Cooperation with wind turbine manufacturers to begin next year
The results of the antiAGE project exceeded expectations. Through a design process using virtual testing and machine learning, VTT was able to develop an optimised solution to a very difficult material problem in less than a year: a highly durable material that hardens when exposed to mechanical stress.
"When we published the news about our solution, wind turbine manufacturers became immediately interested in it. We are now negotiating details with commercial operators," Laukkanen reports.
VTT is also applying for additional funding for the project, since there are plenty of targets for optimised material solutions in other sectors of industry as well. The more complex the product, the more expensive it is to develop materials suited for a specific purpose, and the more difficult it is in general to find material solutions that perform well. AI allows such problems to be addressed with efficiency.
Featured Product
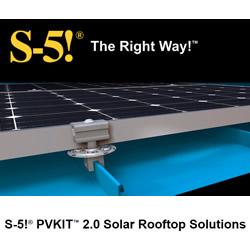