Tackling the biggest wood pellet production problem
The global market for wood pellets has been growing consistently for the last five years according to the Wood Pellet Association of Canada (WPAC). With growth not expected to slow any time soon, Stephen Harding, managing director of wood pellet handling equipment manufacturer Gough Engineering, explains how pellet production plants can keep throughput equally consistent.
For at least the last quarter of a century, the role of renewable energy has been firmly cemented in the public consciousness. Even so, its only in the past couple of years that weve started to see a significant impact.
In fact, it was only this year, more than 15 years after the UK introduced its renewables obligation initiative, that renewable power generated more power than coal and gas. This power came from solar panels, wind farms and the burning of biofuel wood pellets.
The latter is a form of fuel that has become increasingly popular in recent years. According to statistics shared by WPAC in early 2017, the global demand for wood pellets grew at roughly ten per cent each year between 2012 and 2015.
Based on these figures, William Strauss, the president of market analysis firm FutureMetrics, concluded that, "The expectations for the future of wood pellet markets are optimistic. If our forecasts are correct, more than 30 million tonnes per year of new demand by 2025 will drive more than $7 billion of investment in new production capacity worldwide".
This anticipated investment in new production capacity is necessary for the growing market, but it is critical that businesses invest in the right areas of production. While it makes sense for companies responsible for the sourcing of the initial wood to invest in more chopping equipment, processing plant managers must also ensure their equipment is up to the task.
Currently, the biggest problem that Gough Engineering is called on to address in pellet processing plants is the issue of dust in conveying systems. Wood pellets consist of compressed wood chips and saw dust, which are often transported long distances around the world from the source to the production facility.
During this transit, the pellets naturally begin to break apart due to movement, particularly if theyre transported overseas. This produces an excess amount of dust that gets processed alongside the pellets, which can slow production and even bring it grinding to a costly halt.
Process engineers and managers must therefore invest in effective screening products that separate the pellets from the dust.
For example, Gough Engineering recently worked with a UK production plant to address this very problem. The solution was to use a vibratory wood pellet screen, which would ensure that the powder was effectively separated from the pellets using vibrations to classify powder efficiently.
These screens have an adjustable throughput to ensure that engineers can adjust the capacity in line with the size of the batch. They are also able to screen powders of 80 microns and up, allowing engineers to flexibly screen out dust granules of varying sizes.
Since this process is providing sustainable energy, it makes sense that pellet screening equipment can be set up to direct the powder to a different point in production. This means that once the dust is separated, it can be transported to a compressing system to be compressed into more pellets for processing.
If the pellet industry continues to grow at its steady pace and finds a demand for 30 million tonnes per year in 2025, it is essential that plant managers make the process as efficient as possible. With the right sieving and screening equipment in place, biofuel power plants can continue to produce energy reliably.
Featured Product
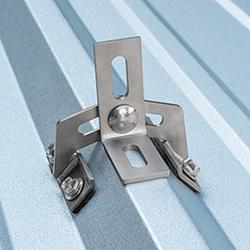