Getting value from e-cycling
Between 2009 and 2012, the European Union (EU) funded an aptly-titled project called the Recovery of Electronic Waste through Advanced Recycling and Demonstration (REWARD). Although the project has concluded, electronics recycling and recovery is an ongoing task in many recycling plants. Here, Stephen Harding, managing director of recycling materials management specialist Gough Engineering, explains how recycling plant managers can improve electronics recovery and reap the rewards.
Achieving the circular economy, or a society in which nothing is wasted or disposed of until its potential value has completely depleted, seems to be one of the EUs key objectives in the twenty-first century. The EU has introduced a number of schemes, initiatives and directives to promote the idea that anything reusable be reused or recycled.
Of course, this isnt an entirely new concept. Businesses have long understood the benefits of drawing the most value from assets as possible. The only difference is that now its become a more important issue for wider society, with the competitive advantage provided by asset utilisation replaced with economic and environmental responsibility.
While it is often promoted from an environmental perspective, there is a strong economic benefit in recycling products such as electronics.
As EU Commission environmental spokesperson Enrico Brivio says of electronics recycling, "the more valuable our waste becomes due to pressures on our resources, the more we will need the technologies and innovation to pump it back into the economy instead of burying it or burning it".
Effective materials recovery is critical in ensuring that the electronics recycling, or e-cycling, process is as effective as it can be. In a typical electronic application, there will be hundreds of resources with little reusable value and many components made of high value materials. Recycling plant managers will naturally want to recover as many valuable materials as possible with little waste mixed in.
This is only possible with effective screening and separation equipment for recovery operations. In most applications where screening is necessary, there is a risk that screen blinding will impact throughput rates.
For example, one stage in the recycling process of a standard refrigerator involves the unit itself being shredded down to separate insulation foam, electronic matter, metals, plastics and gases. From there, each component goes its separate way.
The foam, for instance, is ground into a powder to release the gases contained within it and the resulting polyurethane powder then moves on via a conveying system to another part of the plant for handling.
When this powder is being screened, the powder may accumulate and block the mesh, a phenomenon known as screen blinding. This is not an uncommon occurrence and, from Gough Engineerings experience in material processing, can be prevented by using screens that include an ultrasonic vibratory motor.
However, its also vital that no valuable electronics or metals are mixed in with the foam ahead of the grinding process. To ensure this, recycling plant managers must use a screening and separating system that can effectively sort the shreds of polyurethane from the steel fragments or gold-containing circuitry.
Each recycling processing plant will require something different from its screening and separation systems, whether its due to the flammability of processed items or granularity. As such, it is vital that recycling plant managers consult with a materials management specialist to determine the best equipment to maximise the value of their operations.
The EU anticipates there to be more than 12 million tonnes of electronic waste across Europe each year by 2020. By investing in the right equipment to sort through waste and recover valuable materials effectively and efficiently, recycling plant managers can be rewarded with lower output and input costs, less processing downtime and a greater contribution to Europes circular economy.
Featured Product
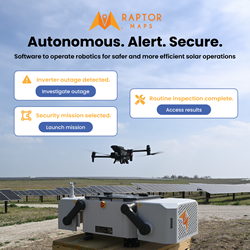