Morgan Advanced Materials Produces Plasma Cavity for ANU
Morgan Advanced Materials provided a prototype plasma cavity for the Helicon Double Layer Thruster (HDLT), a new gas plasma space engine for use on satellites being developed by the Australian National University (ANU).
Morgan Advanced Materials, a leading supplier of high purity Alumina custom-made, high precision ceramic components, provided a prototype plasma cavity for the Helicon Double Layer Thruster (HDLT), a new gas plasma space engine for use on satellites being developed by the Australian National University (ANU). Gas plasma engines are used in electric propulsion, a technology becoming more and more popular, because it uses "greener" propellants, rather than more toxic chemicals.
Engineers at Morgan provided design feedback and a review of tolerances before developing the cavity prototype, made of its proprietary material, AL300, a high purity alumina known for its excellent electrical properties. After developing an in-house process to produce the components, Morgan was able to achieve first pass success, getting prototypes into ANU's hands with an extremely short lead time so the finished components could be used for the space-qualification testing.
The project, under the direction of ANU's Space Plasma, Power and Propulsion Laboratory, is funded by the Australian Space Research Program, Astrium, an aerospace manufacturer that is a subsidiary of the European Aeronautic Defence and Space Company (EADS), the Surrey Space Centre, ANU, and Vipac, a multi-disciplinary technical consultancy.
Zachary Waddle, Engineering Manager at Morgan Advanced Materials,worked closely with ANU to develop the component. The AL300 97.6% purity Alumina has been used for decades in extremely high-voltage applications, as well as RF applications. "The material had been successfully used in the manufacture of plasma generation components and also for high voltage insulation used in new and emerging scanning electron microscopes, so I thought it would be an excellent match for this project." He adds, "It was very gratifying to be able to help a customer with such a unique requirement, and to collaborate on the technical specifications to get prototypes into their hands quite quickly."
Featured Product
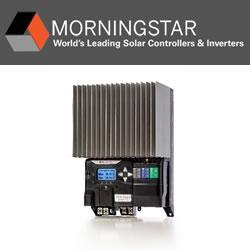