How to Design a Lithium Ion Battery with Lower Material Costs
The cost, weight and volume of lithium ion cells can be reduced by using a low cost, high rate separator. Cells using the Dreamweaver Silver™ separator and electrodes that were 20% thicker gave similar discharge performance over a range of rates. In this paper, the material costs of manufacturing these cells are compared, and result is that the cell using the Dreamweaver separator is 6% lighter, has 4% less volume, has 17% lower foil costs and 42% lower separator costs, resulting in 16% lower total material costs. For higher power cells, the savings could be up to 20% of material costs. For common automotive batteries, the savings could be 8 – 42 kg and $608 - $3,240/automobile.
Introduction: The common understanding of designing lithium ion batteries for higher energy density is to use a separator of minimum thickness, because the separator does not carry energy, but rather is a necessary safety device. The usual assumption is that the battery performance cannot be affected by changing the properties of the separator.
So what if the separator had higher ionic conductivity, allowing a battery to work faster, getting optimum performance out of the electrodes at high rates? The answer is that a lighter, more efficient and lower cost battery could be made with these materials.
Method and Results: To test this, Polystor made two cells with NMC cathodes loaded at 2.5 mAh/cm2, one with a standard tri-layer 25 micron separator and one with a Dreamweaver Silver™ 30 separator. These cells were tested for capacity at various discharge rates. Cells were also made with the Dreamweaver separator at 3.0 mAh/cm2 electrode loading which had similar performance to the cell with the standard tri-layer 25 micron separator at 2.5 mAh/cm2 electrode loading up to 2C, and higher performance at faster rate.
If these results are normalized on a per kWh energy basis, the standard separator cell will require 9.5 m2 of electrode, separator and current collectors, while the Dreamweaver cell would require only 7.9 m2 of these materials. Estimates of the weight, volume and cost of materials per kWh are shown in Table 1, below. In these estimates, the cost, weight and volume assumptions were taken from "Modeling the Performance and Cost of Lithium Ion Batteries for Electric Drive Vehicles," a report from Argonne National Laboratories and a cost for the Dreamweaver separator that is 30% lower than the cost for the standard separator.
Conclusions: The cells made with Dreamweaver Silver™ separator use less separator and foil materials and achieve similar rate performance. The weight is reduced by 250 g/kWh, or 6% of the total material weight. The volume is reduced by 50 cm2/kWh, or 4% of the total material volume. The cost of the separator is reduced by 42%, and the cost of the current collector foils reduced by 17%, resulting in a total material cost savings of $19/kWh, or 16% of total materials cost.
If similar results (20% increased electrode coating) were achievable for high power cells typical of automomotive batteries (1.25 mAh/cm2), the Dreamweaver Silver™ cell would weigh 500 g/kWh less (8%), have 100 cm3/kWh less volume (5%). The cost of the separator would be reduced by 42%, and the cost of the current collector foils reduced by 17%, resulting in a total material cost savings of $38/kWh, or 20% of total materials cost.
The weight, volume and cost savings are shown below per kWh and for the batteries included in the Chevrolet Volt, the Nissan Leaf and the Tesla S Luxury model.
These are solely material savings, and do not include potential savings in inventory, waste and efficiency in the battery or pack manufacture. This test was done with the Dreamweaver Silver™ 30. Further reductions should be achievable using the Dreamweaver Silver™ 25 separator.
Featured Product
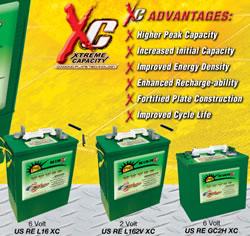