Smooth Operator
Castrol Industrial warns wine turbine operators about taking chances with their investments.
Lubricant specialist Castrol Industrial is urging wind turbine operators not to take chances with their investments by using inferior lubrication products to achieve short-term cost savings.
As turbine technology develops to generate greater yields, the microscopic films of oil protecting vital components are put under huge stresses, often in extreme conditions. Any underperformance in these products could cause components to fail resulting in higher maintenance costs and costly downtime.
To help operators mitigate this risk, Castrol Industrial's flagship Castrol Optigear Synthetic X 320 gear oil product has been proven in an independent study to outperform existing technologies and prolong gearbox life.
The same trials found that Castrol Optigear Synthetic X 320 lubricant, used in accordance with manufacturer's recommendations, produced significant operational benefits over the global market leading product, including:
• Reduced incidence of micro-pitting, one of the leading causes of gearbox failure
• Lower friction coefficient - more power from less wind
• Greater film thicknesses, helping to extend gearbox life
• Lower levels of component damage, reducing potential maintenance costs and helping to avoid unplanned repairs
When used as specified, Castrol Industrial has calculated that the potential annual savings of switching to its Castrol Optigear Synthetic X 320 system could be up to $5,000 per wind turbine operated, taking into account associated reductions in the typical number of oil changes, changing parts (including labour). For example, based on these calculations, a typical operator managing 50 wind turbines could save up to $250,000 a year.
Castrol Industrial wind energy key account manager Sven Thiesen says: "The tests reveal significant and compelling evidence for both Original Equipment Manufacturers and those providing aftermarket service contracts for wind turbines and these benefits are hard to ignore.
"As wind turbines become larger, more powerful and, in the case of offshore sites, less accessible, there has never been a stronger need to reduce wear and tear and predicting service intervals to avoid component failure and unplanned downtime.
"While budgets are tight, the temptation to use lower-cost lubrication is high. Operators cannot afford to take any chances, or they risk facing the expense of replacing components and unplanned maintenance."
For wind turbine gearboxes already exhibiting signs of wear, the trials also revealed how Castrol Optigear Synthetic X 320 could actively smooth damaged surfaces through its advanced friction modifiers, prolonging the life of the gearbox.
Tests to measure component weight loss - a key indicator of micropitting and fatigue, which can lead to serious component failure - demonstrated Castrol Optigear Synthetic X 320 had superior performance compared with other products.
Today, Castrol supplies a line of wind turbine-specific lubricants that are the chosen ‘first fill' lubricant for a number of major players in wind turbine manufacturing. By working closely with customers and listening to their needs, the company has been able to engineer a product that meets increasing demands for long-term value and performance.
Sven Thiesen says: "The knowledge Castrol Industrial has built up in the design and development of Castrol Optigear Synthetic X 320 is a powerful tool for manufacturers and aftermarket service providers. With accurate data on recommended service and replacement intervals they can plan ahead and reap the significant dividends this has to offer."
1. Powertrib independent study using MPR (Micro, Macro, Pitting) conducted at 60°C on 6 May 2010
For further press information, please contact:
Graeme Jackson / Simon Williams
Tel: +44 (0)117 973 1173
Email: gjackson@brayleino.co.uk / swilliams@brayleino.co.uk
Featured Product
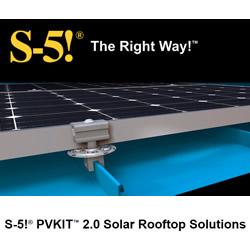
S-5!® PVKITâ„¢ 2.0 Solar Rooftop Solutions
The concept of combining PV arrays with standing seam metal roofing is growing-for good reasons. Metal roofs have a life expectancy of more than 40 years. Shouldn't the mounting system last as long? With S-5! zero-penetration attachment technology and PVKIT 2.0, the solarized metal roof is the most sustainable system available -and without compromising roof warranties! PVKIT 2.0 is the also the best solution for attaching PV modules directly to any exposed fastener metal roof.