Maintaining erosion control best management practices (BMPs) and preventing stormwater pollution is crucial at every phase of the solar project, but it can also be costly, time-intensive, and difficult to do at scale.
A New BMP for Erosion and Stormwater Management in Solar
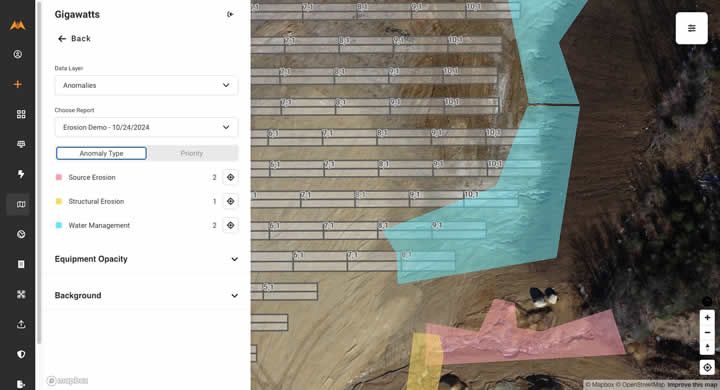
Peter Stovall | Raptor Maps
Maintaining erosion control best management practices (BMPs) and preventing stormwater pollution is crucial at every phase of the solar project, but it can also be costly, time-intensive, and difficult to do at scale. Especially during the construction phase as the land recovers from civil work and grading, vegetation is still taking root and there is a lot of heavy traffic on site. This article provides three (3) tips to increase the effectiveness of your SWPPPs and the efficiency of erosion-related inspection & maintenance efforts, applying to both the construction and operational phases of the solar project. In particular, these tips will help owners, operators, and EPCs reduce both the risk of regulatory non-compliance and the cost of compliance.
A Process-based BMP for Permit Compliance and SWPPP Implementation
As more solar gets installed and the average size of solar projects increases, mitigating erosion and stormwater runoff can become increasingly challenging, with more projects and more acres to manage. Even when structural best management practices (BMPs) are installed for erosion and sediment control (such as sediment fences, silt traps, and retention ponds), robust process-based BMPs are needed to make sure those structural BMPs are working as intended and in tandem with each other.
One such BMP? Erosion Control Inspection and Maintenance.
In the United States (US), the General Construction Permit (GCP) requires inspection every 7 days, or every 14 days and inspection within 24 hours of a stormwater or discharge event (part 4.2). However, regular and responsive inspections can be costly and difficult.
Under GCP requirements, that means at least one truck roll every 7-14 days, plus scrambling within 24 hours of stormwater and discharge events. With a truck roll averaging $750, costs quickly add up. In addition, environmental compliance teams and field teams may log erosion and stormwater issues in disparate, siloed systems - sometimes using only pen and paper.
But the costs of non-compliance with stormwater pollution prevention plans (SWPPPs) and post-construction requirements are also high with environmental damage, regulatory fines (such as a $16K per day fine from the EPA), potential litigation-related costs, and reputation damage with the communities impacted by the stormwater discharge and soil erosion. In the worst cases of erosion damage, this can lead to project shutdowns or delays that carry further financial ramifications.
Managing erosion and sediment begins on day one and continues throughout the entire life of the solar project, especially in more storm-prone regions like the US Gulf Coast. Whether it is during the construction phase or when the solar project is operational, sending out a human inspector for regular erosion inspections can be challenging. Even where personnel are staffed on-site, the logistical and time costs remain high.
How can you implement a more robust erosion control inspection and maintenance program without eroding your budget and cash flows?
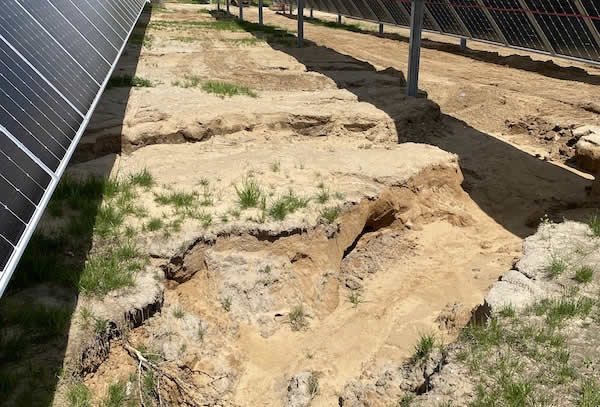
Photo credit: North American Clean Energy
Challenges with Manual Erosion and Sediment Control Inspections
The US Environmental Protection Agency (EPA) stresses the importance of routine and responsive inspections and the maintenance of BMPs to ensure their effectiveness, with many permitting authorities requiring construction staff to perform self-inspections (source: US EPA). Those inspections must be properly documented, with clear visual documentation of any failing structural controls or other erosion issues. Corrective action and maintenance work must also be logged properly.
However, manual, human-led inspections pose several challenges.
First, human-led inspections are time-consuming and can require significant logistical planning - especially if a more rapid mobilization is needed due to changing weather forecasts. This can strain resources and budgets, particularly on large solar projects where erosion issues can be widespread. The sheer scale of modern solar projects - some covering hundreds or even thousands of acres - make it difficult to inspect the entire site manually in a timely and efficient manner. And even with thorough planning, manually mobilizing inspectors to perform pre- and post-storm checks can be logistically challenging and costly. We estimate the costs at upwards of $1,500 per MW per year.
Given the size of many utility-scale sites, there is a very real chance that issues are missed and can therefore escalate, causing damage before the next inspection and opening owners and operators up to regulatory and civil liability.
Relatedly, lack of adequate training can limit the success of an erosion and sediment control inspection program and increase the likelihood of human error when identifying deficiencies and related corrective actions that are needed.
After a storm, ponding from improperly drained stormwater might not be the only issues on site - there could be damaged or broken equipment, loose wiring in a wet environment, and other potential hazards, exposing human inspectors or technicians to unsafe environments.
And when inspections do occur, findings are often in physical, pen and paper documents or siloed in different systems across teams, which make it harder to analyze the findings, strategize at a portfolio-level or share across teams. The EPA also states that corrective actions taken should also be logged, which also often occur in siloed systems.

Photo credit: Compliance Resources, Inc.
3 Tips for Effective Erosion Control Maintenance
Based on EPA recommendations and the challenges associated with those recommendations, here are 3 tips for scaling and optimizing erosion and sediment control maintenance:
-
Instead of a human inspector, use drones
-
Collect imagery data and analyze through software
-
Inspect more frequently and remotely with autonomous drones
Tip #1: Instead of a human inspector, use drones
Compared to a boots-on-the-ground human inspection, drones can cover more ground and collect more data per acre/sq. km inspected. As the drone flies, it can capture high-resolution imagery for uploading to an analytics platform for identifying issues such as improper drainage underneath fencing or soil displacement underneath installed solar panels.
Based on method of operation, there are two main categories of drones for the solar industry: operated (1) via an on-site pilot or (2) through remote commands. Both types of drones can collect data faster than a human inspection, but drones that require an on-site pilot still run into the same obstacles of mobilizing inspectors, especially to more remote sites.
Autonomous drones, in contrast, reside on-site within a weatherproof “dock” (which has given it the nickname “drone-in-a-box”) and can be sent remote commands to conduct inspections using mission planning software. Because you do not need to send someone to the site, autonomous drones give you a lot more flexibility and cost efficiency when inspecting different parts of your solar project. You can “set and forget” your scheduled missions with peace of mind, and investigate a stormwater or discharge event remotely within 24 hours.
Tip #2: Collect imagery data and analyze with software
Rather than relying on human eyes during a manual erosion control inspection, collecting imagery data at scale (such as through a drone) and analyzing that data with software not only reduces the time taken to analyze a site for any issues, but also reduces the likelihood of human error and increases the likelihood of early detection of erosion issues that may benefit from proactive management.
Additionally, a software-based approach can help break down data siloes and digitize erosion inspection findings for use by multiple stakeholders. We recommend using a GPS-accurate Digital Twin to store your data and findings. A Digital Twin is an enhanced virtual replica of your physical asset which provides you a more intuitive and structured way to work with your data, especially when the data is geo-located. It also serves as an auditable system of record for your erosion inspections, corrective actions taken, and many other data points (such as equipment-driven underperformance or construction progress validation).
Centralized findings also make it much easier for asset managers, performance engineers and environmental compliance engineers to optimize for erosion control at a portfolio-level.
Identified Erosion in the Raptor Maps Digital Twin
Tip #3: Use autonomous drones for more frequent erosion and sediment control inspections
Using autonomous drones cuts the cost of having to send someone to inspect your site and increases your flexibility on when and how frequently you want to inspect your erosion and sediment controls. With the right software for autonomous drone operations, you can schedule regular erosion inspections that fly consistent routes each time, collect data before and after a weather event, and inspect targeted blocks or areas of the project with known erosion and sediment issues.
Images collected from those repeated erosion inspections build a timeline of visual data in the Digital Twin that you can use to compare changes over time, identify issues earlier, and prevent erosion from persisting and increasing the risk of environmental contamination.

Example Erosion Monitoring & Remediation Schedule with Autonomous Drones
Conclusion: Diligent and Scalable Erosion Inspection and Maintenance
As the solar industry continues to grow, it will be important to continue being good stewards of our land and water. Established structural BMPs for erosion, sediment, and stormwater control, such as silt fences or dry ponds, need to be monitored and maintained to remain effective in preventing stormwater and erosion from polluting the surrounding environment. With more and larger solar projects to build and operate, software-enabled strategies can be a force multiplier without straining your team and your budgets. Proactive management avoids costly damage, fines, and environmental harm — ultimately safeguarding both your investment and our planet. Autonomous drone inspections coupled with erosion analysis software can dramatically reduce the cost of that management.
If you are interested in learning more on how this might work for your projects, check out our most recent webinar - Keeping it Level: How to Automate Erosion and SWPPP Inspections
The content & opinions in this article are the author’s and do not necessarily represent the views of AltEnergyMag
Comments (0)
This post does not have any comments. Be the first to leave a comment below.
Featured Product
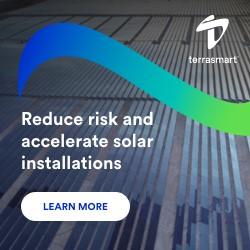