This article explores the application of vibro-thermography as an effective non-destructive testing (NDT) technique for detecting both surface and subsurface cracks in turbine blades.
Turbine Blade Inspection Using Vibro-Thermography
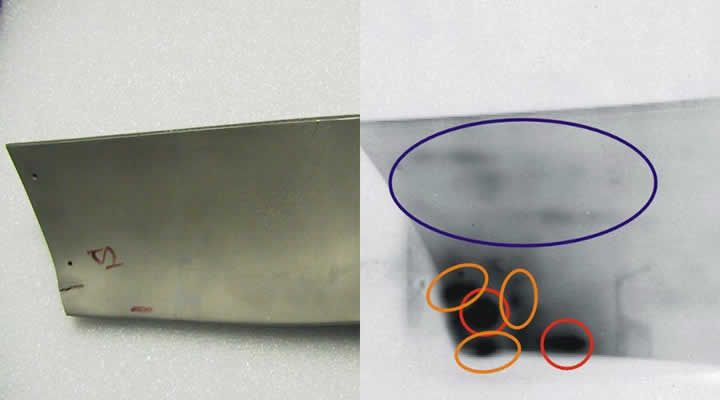
Article from | MoviTHERM
A Reliable NDT Technique for Detecting Surface and Subsurface Cracks in Turbine Blades
Turbine blade inspection plays a crucial role in aerospace, power generation, and industrial applications, where the structural integrity of these components directly impacts operational efficiency and safety. Detecting cracks in turbine blades is of utmost importance to ensure their reliable performance. Traditional inspection methods, such as dye penetrant testing, have limitations in detecting subsurface cracks.
This article explores the application of vibro-thermography as an effective non-destructive testing (NDT) technique for detecting both surface and subsurface cracks in turbine blades. Additionally, we will discuss the limitations of dye penetrant testing in detecting subsurface cracks and the reasons behind them.
Challenges with Traditional Inspection Methods
Limitations of Dye Penetrant Testing
Large turbine blade with ultrasonic horn in test fixture.
Dye penetrant testing, a commonly used method for crack detection, primarily focuses on surface-breaking cracks. However, it has inherent limitations when it comes to detecting subsurface cracks in turbine blades. The nature of subsurface cracks makes it challenging for liquid penetrants to reach the crack depths, resulting in limited or no indication of their presence. Additionally, visual examination is often insufficient for identifying subsurface cracks, especially when they are located deep within the material.
Insufficient Crack Visualization
Surface examinations alone may not provide an accurate representation of the extent and severity of turbine blade cracks. Without clear visualization, it becomes challenging to characterize cracks in terms of size, depth, and extent, hindering effective maintenance and repair decisions.
Vibro-Thermography for Turbine Blade Inspection
To overcome the limitations of traditional inspection methods, advanced techniques like vibro-thermography have emerged as promising solutions for more comprehensive turbine blade inspections.
How Vibro-Thermography Works
Thermal result image with large crack indication on bottom edge of blade.
Vibro-thermography combines the principles of vibration excitation and thermal imaging to detect cracks in turbine blades. The technique involves inducing mechanical vibrations into the blade and monitoring the surface temperature response using an infrared camera. By analyzing the thermal patterns, it is possible to identify both surface and subsurface cracks.
Vibration Excitation
Vibro-thermography utilizes various methods to induce vibrations in turbine blades. These include mechanical excitation using shakers, air-coupled excitation, or piezoelectric actuators. The vibrations cause dynamic stress redistribution, leading to localized heating at crack sites. This phenomenon enables the detection of subsurface cracks that may not be visible to the naked eye.
Thermal Imaging
An infrared camera captures the surface temperature response of the turbine blade during vibration excitation. Subsurface cracks disrupt heat flow, resulting in thermal anomalies that can be visualized and analyzed. Advanced image processing techniques can enhance crack visibility and aid in quantitative characterization, providing valuable insights for maintenance and repair decisions.
Advantages of Vibro-Thermography for Turbine Blade Inspection
Subsurface Crack Detection
Vibro-thermography excels in detecting subsurface cracks in turbine blades. By inducing vibrations and monitoring the resulting thermal patterns, the technique can identify cracks even when they are not visible on the surface. This capability enables comprehensive inspection, ensuring the integrity of turbine blades, even in critical areas prone to subsurface cracking.
Enhanced Crack Visualization
Thermal results image – front view of turbine blade with crack indications.
The thermal imaging component of vibro-thermography provides a visual representation of cracks, making them easier to identify and characterize. The contrast between crack-induced thermal anomalies and the surrounding material facilitates accurate detection and quantification of crack size, depth, and extent. This information allows maintenance teams to make informed decisions regarding repairs or replacements.
Non-Destructive Testing
Vibro-thermography is a non-destructive testing technique that does not alter or damage the turbine blade during inspection. The vibrations applied are controlled and within safe limits, allowing for repeated inspections without compromising the structural integrity of the blade. This advantage is particularly significant in critical applications where turbine blade performance is crucial.
Turbine blade rear view with sub-surface micro-cracking indications.
Time-Efficient Inspection
Vibro-thermography offers a time-efficient inspection process, allowing for rapid scanning of turbine blades. The application of controlled vibrations and the real-time monitoring of thermal responses enable quick assessment of the blade’s condition. This time-saving advantage is particularly valuable in industries where minimizing downtime is essential.
Emerging Trends in Vibro-Thermography
As technology continues to advance, new trends and developments are emerging in the field of vibro-thermography, enhancing its capabilities and expanding its applications. Here are some notable trends to watch out for:
Multi-Frequency Excitation
Traditional vibro-thermography techniques rely on single-frequency excitation to induce vibrations in turbine blades. However, researchers are exploring the benefits of multi-frequency excitation, where multiple vibration frequencies are applied simultaneously. This approach can provide more detailed information about the structural integrity of the blades, improving crack detection accuracy and reducing false positives.
Integration of Artificial Intelligence
The integration of artificial intelligence (AI) techniques with vibro-thermography is gaining traction. AI algorithms can analyze the thermal response data collected during inspections, enabling automated crack detection and characterization. Machine learning algorithms can learn from past inspection data to improve the accuracy and efficiency of future inspections, making the process even more reliable and cost-effective.
Real-Time Monitoring
Real-time monitoring during vibro-thermography inspections is becoming increasingly important. By continuously monitoring the thermal response of turbine blades as vibrations are applied, potential defects or changes in crack behavior can be identified promptly. Real-time monitoring enables proactive maintenance and repair decisions, minimizing the risk of unexpected failures and maximizing the lifespan of turbine blades.
Portable and Handheld Systems
With advancements in sensor technology and miniaturization, portable and handheld vibro-thermography systems are becoming more accessible. These compact systems allow for on-site inspections and can be easily transported to different locations. Portable systems offer convenience and flexibility, particularly in situations where transporting large equipment is challenging or time-consuming.
Interested in Implementing Vibro-Thermography for Your Inspections?
If you’re looking to optimize your inspection processes and enhance the reliability of crack detection in turbine blades or other critical components, we can help. MoviTHERM offers state-of-the-art vibro-thermography systems that can revolutionize your inspection capabilities.
Our experienced team can assess your specific needs and provide tailored solutions to meet your requirements. Whether you operate in the aerospace, power generation, or industrial sector, vibro-thermography can offer significant advantages in ensuring the integrity and safety of your parts.
Contact us today to schedule a consultation and find out how our systems can help you detect and characterize cracks in your turbine blades or other critical components.
The content & opinions in this article are the author’s and do not necessarily represent the views of AltEnergyMag
Comments (0)
This post does not have any comments. Be the first to leave a comment below.
Featured Product
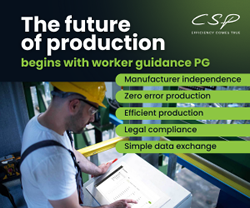