Module Preparation & Strategic String Design - Part I. By strategically designing module and string layouts, prepping modules in staging areas and performing repeatable installation procedures, all hurdles to installing rail-less solar can be overcome.
Wire Management of Rail-Less Solar PV Systems on Low-Slope Metal Roofing
Article from | S-5!
Rooftop rail-less solar PV systems have been around for many years, and year-over-year, continue to be a growing part of the solar market. With the adoption of rail-less technology and the many benefits, including significant cost savings, hesitancies still exist with both the technology and with learning new methodologies. One of these hesitancies is wire management.
With rail-based systems, installers tie everything and anything to the rails. With rail-less systems, there are subtle differences in methodologies and some relearning to ensure installation efficiency but the important elements exist with both conventions—pre-planning and strategic thinking.
By strategically designing module and string layouts, prepping modules in staging areas and performing repeatable installation procedures, all hurdles to installing rail-less solar can be overcome.
Today, we take a look at the importance of module preparation and strategic string design.
Module preparation on the ground means less work on the roof
Module Preparation
Prepping modules is one of the highly critical steps that must be planned, designed and executed to minimize installation time on the roof. When you are on a roof, likely tied-in to fall protection by a harness, the more that module is prepped in advance, the easier and faster it is to install. If the leads and connectors are clipped to the exact necessary position, you can just plug-n-play on the spot…less time on the roof means reduced costs.
Begin preparation at the office before you even get to the job site. Start with the design of the PV array; know all of the products at your disposal to achieve good wire management; and map out all configurations, module-level wire management and module-to-module connections. Then, try it out with real products to ensure your configurations will actually work as planned.
Once on site, begin with teams of one or two installers on the ground or at a rooftop staging area preparing the modules using a string diagram and wire management maps as guides so installers know how to properly prep the leads, connectors and other equipment. Then, your team of installers can install the prepped modules and make any necessary electrical connections with incredible efficiency.
With pre-planning and effective module preparation, installers can set the modules and don’t have to mess around with wire management. They can lay modules in a plug-n-play, ultra-fast way, building the system as they go. Follow your methodology consistently step-by-step with robotic repetition, which will save you time and make it easier for the installers.
Strategic String Design
Take the time to strategically design your string layouts. This will enable installers to minimize wire length, reduce the time it takes to clip up wires and plug in jumpers, and also provide easy access to string ends, optimizers or microinverters. A few hours at the desk optimizing string design can save many hours or even days on the roof.
Strategic string design minimizes labor and material
On the front end, by creating logical string layouts and grouping home runs, the system designer can make or break the job for installers on the roof, as well as for future O&M activities.
The S-5! Solution
S-5! offers a rail-less, direct-attach™ solar mounting solution for metal roofs. S-5! PVKIT® pre-assembled components provide a simple, economical method for installers to “lay & play” modules with tested, engineered, attachment of modules to any metal roof type. Even first-time installers of S-5’s new rail-less system have reported installation times of 90 seconds/module—a savings of up to 50%, so it is certainly worth a look.
Benefits of Direct Attaching to Metal Roofing Compared with Rail Mounting
-
Far fewer parts
-
Huge reduction in freight cost
-
Labor Reduction
-
Reduced handling/logistics
-
Reduced dead load to the roof
-
25% better load distribution
-
Speed of system installation
-
Better wind resistance
For information, videos and webinars on this topic and more, please visit www.s-5.com.
S-5! PVKIT® offers a rail-less, direct-attach™ solar mounting solution for metal roofing
Stay tuned for Part 2 Wire Management of Rail-Less Solar PV Systems on Low-Slope Metal Roofing in our next issue which will focus on Correction Gaps, Trunk and Branch Wire Management and Module-Level Power Electronic.
The content & opinions in this article are the author’s and do not necessarily represent the views of AltEnergyMag
Comments (0)
This post does not have any comments. Be the first to leave a comment below.
Featured Product
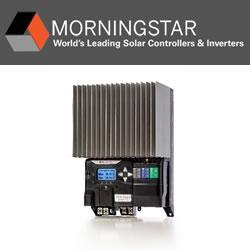