As energy costs increase and governments offer incentives for increased use of renewable energy, utilities are building more large solar farms, and pushing to increase their efficiency.
Pulling the Strings: a Look at the Latest Trends in Utility Solar Farm Designs and How Their Efficiency Can Be Improved
Contributed by | LEM
Large solar power farms are changing the way they work to boost efficiency and draw the most power from their assets. The solar market is split into three sectors—residential, commercial and utility. Of these, the utility sector is the largest, and the one that can most benefit from an increase in efficiency.
Increasing the maximum power point
Large solar plants use a central inverter system between 500 kW and 2 MW. String of solar panels run to combiner boxes, which then connect to a central inverter. These photovoltaic strings normally contain around twenty panels.
To draw the most power from a panel, there is what is known as the maximum power point (MPP) for voltage and current, and systems to detect this are called maximum power point trackers (MPPTs). To find the MPP, the current through the panel is steadily increased until it reaches the point where the most power is being drawn. If the current is increased beyond that, the power drawn goes down again. The MPP is influenced by how much sun falls on the panel.
The way solar plants traditionally operate is by running all the panels at the same MPP. With the panels in series, the same current flows through them all. The various strings are wired in parallel with each other and all have the same voltage.
As long as all the panels are relatively similar and have the same orientation and view of the sun, running them all with the same MPP is fine. But this is rarely the case with large solar farms. The sun will be hitting the panels at different intensities. For example, a cloud going over the farm will mean that some panels are in shade while others are in bright sunshine and some in between.
If the system is set up so that all the panels run from the same MPP, this effectively means the MPP of the least efficient panel and thus the efficiency of the whole plant decreases significantly.
Creating zones
The trend, therefore, is to split the plants into smaller zones with each zone having its own MPPT. This means that separate areas of the plant will be running at different MPPs depending on the state of the sun.
An MPPT is basically a DC-DC converter. In the past, with a switching frequency of around 20 kHz, plant operators baulked at installing inverters with MPPTs because the extra cost outweighed the efficiency savings.
Today those costs have been significantly reduced thanks to power electronics that can switch at frequencies around 50 kHz or higher.
The higher frequency means that the size of the inductor can be reduced, making the whole system smaller and thus cheaper. It also means the IGBTs and other power components are more efficient, so they generate less heat and so need a smaller heatsink.
The rise of string inverters
Growing in popularity is to take this further and have an inverter at the end of each six to ten strings; this is the string inverter. Each string inverter is only about 30 to 50kW and this has the added advantage that if one inverter fails then only a small zone is offline while that panel is replaced. It also makes it easier for on-site engineers to trace and replace the faulty panel or string inverter, reducing downtime dramatically.
Such installations can involve as many as 200 MPPTs for each megawatt. Although expensive, the price is falling with increased volume and improvements in power electronics. Market analysts forecast that the utilities installed with string inverters will overtake those with central inverters by 2018.
Intelligent combiner boxes
Rather than having the MPPTs in the inverters, an alternative is to put them into the combiner boxes and use intelligent control to run each at the MPP for the string to which it is connected. Typically, there will be between four and eight MPPTs in a combiner box.
LEM HSLR current transducers
LEM’s HSLR current transducers lead the way for more efficient MPPTs at a lower cost. HLSR transducers, which can be used in either string inverters or intelligent combiner boxes, are the simplest, most reliable and efficient on the market. They provide around 1% accuracy and have a 2 µs reaction time, fast enough for the 50kHz switching frequencies. Their isolation suits 1500V designs, the level at which most large plants run or are aiming to run, and their robust design can withstand lightning strikes of 5 to 10 kA for 8 to 20 µs pulses.
The HLSR series uses LEM’s proprietary ASIC, specially designed and optimized for open-loop current transducers. Every step of the production process was optimized to support the inverter manufacturers with the huge price pressures they face.
For more demanding users, LEM also offers the HO series. In addition to the same features as the HLSR, the HO series provides an additional OCD output. This digital output indicates if the current has exceeded a defined threshold of typically three IPN. It can be used as hardware protection for the transistors, reducing the component count and the complexity of the design.
Conclusion
As energy costs increase and governments offer incentives for increased use of renewable energy, utilities are building more large solar farms, and pushing to increase their efficiency. According to the Solar Energy Industries Association, the U.S. solar market reached 58 GW of capacity in 2017 and is expected to more than double over the next five years, with two thirds of that capacity being utility-scale projects.
Improvements in power electronics mean it is now viable to use more MPPTs so that each part of the plant can run at its maximum efficiency. However, to do this requires highly accurate current measurement—which LEM’s HLSR provides. With LEM, whatever the weather, utilities will know they are getting the best out of their solar farms.
The content & opinions in this article are the author’s and do not necessarily represent the views of AltEnergyMag
Comments (0)
This post does not have any comments. Be the first to leave a comment below.
Featured Product
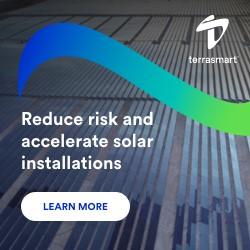