The reliance on sodium sourced from soda ash supports environmentally friendly practices that avoid the energy-intensive process that is often associated with lithium mining. Further innovations in sodium battery technology further enhance its sustainability and performance
Sodium Batteries for Use in Grid-Storage Systems and Electric Vehicles
Dr. Raj Shah, Mr. Mathew Roshan and Dr. Vikram Mittal | Koehler Instrument Company
Abstract
The future of sodium-ion batteries holds immense potential as a sustainable and cost-effective alternative to traditional lithium-ion batteries by addressing critical challenges in energy storage, scarcity of lithium, and sustainability. A key benefit of sodium-ion is its reliance on soda ash, an abundant material synthesized from trona, a common mineral found in the earth’s crust. Soda ash offers a sustainable and ethically sourced supply of sodium. The abundance of this material reduces material costs, mitigates ethical issues, and avoids the supply chain bottlenecks associated with lithium. The usage of soda ash as a primary sodium source enables several advantages in sodium-ion battery applications, particularly in plug-in electric vehicles (PEV) and grid storage. Beyond cost-effectiveness, the reliance on sodium sourced from soda ash supports environmentally friendly practices that avoid the energy-intensive process that is often associated with lithium mining. Further innovations in sodium battery technology further enhance its sustainability and performance. Developments in anode and cathode materials, including advanced carbon anodes and layered oxide cathodes, have improved energy density, cycle life, and recyclability. Additionally, researchers have made strides in stabilizing electrolytes, boosting efficiency and safety. These advancements bring sodium-ion batteries closer to competing with lithium-ion systems in terms of energy storage capacity and operational lifespan. However, sodium-ion batteries remain particularly advantageous for stationary energy storage systems, such as solar and wind energy storage, where their lower cost and scalability excel. Despite their progress, Na-ion batteries face challenges, particularly in energy density, which limits their suitability for weight-constrained applications like long-range electric vehicles. However, their ability to support large-scale energy storage makes them a critical component of a sustainable energy future.
Introduction
The growing demand for efficient and sustainable energy sources and storage systems has positioned rechargeable batteries at the forefront of technological innovation. Among these, lithium-ion batteries are the most prevalent of the options available as sources of energy for smartphones and electric vehicles. The usage of batteries in electric vehicles is especially notable environmentally since 44% of greenhouse gas emissions as a result of the transport industry come from passenger vehicles (Sheldon, 2023). The usage of plug-in electric vehicles (PEV) which employ lithium-ion batteries can be used to dramatically reduce carbon emissions which poses a large environmental incentive for automotive companies to invest in lithium as a substitute for gasoline as the primary fuel for commercial and passenger vehicles.
Since their commercialization in the 1990s, lithium batteries have revolutionized energy storage in portable devices (Li, 2018) and have become an industry standard. Despite their widespread adoption, concerns over lithium resources, long-term sustainability, and rising costs have led to an explosion of research into alternative technologies. The advancement of such alternatives not only addresses concerns over resource scarcity but also aligns with global efforts to reduce carbon footprints and transition to a circular economy. Sodium batteries have emerged as a potential alternative to lithium-ion batteries as a result of the abundance and low cost of soda ash. However, the development of these batteries is not without challenges, including achieving competitive energy densities and ensuring long-term stability. By examining the potential of soda ash batteries, this review aims to contribute to the growing body of research dedicated to creating efficient, cost-effective, and sustainable energy storage solutions for a rapidly evolving world.
Background
Battery Design
A battery is a colloquial term for a voltaic cell comprised of an anode, cathode, and electrolyte. These voltaic cells are based on an electrochemical reaction that involves the oxidation of an electrode at the anode while electrons flow through a current toward the cathode where reduction occurs. These two half-reactions take place in distinct halves which are kept apart by a separator, with an electrolyte medium for ions to flow through. Modern-day batteries function on a 3-step electrochemical reaction. In the case of common lithium-ion batteries, lithium-intercalated graphite is split into lithium-ion, graphite, and a free electron. The lithium-ion and free electron combine with cobalt (IV) oxide at the anode forming lithium-cobalt oxide. These two half-reactions form a dynamic equilibrium which is the reason that lithium-ion batteries are rechargeable (Takada, 2003)
Although graphite’s role in this reaction can be feasibly substituted with alternate chemicals like silicon (Zuo 2017), the process by which the cell is recharged remains the same. Alternatively, other ion cells use oxygen in an alternative redox reaction. In this reaction, oxygen gas is reduced at the cathode to produce the superoxide ion. This ion combines with lithium-ion or sodium-ion to produce lithium superoxide or sodium superoxide, unstable molecules that coordinate with other molecules to form metal peroxides. Ion batteries are recharged by passing an external current through the battery, forcing electrons to move from the positive to the negative electrode. This process is called intercalation, where ions become embedded in the porous material of the negative electrode. When the battery is empty, an external source of voltage called the charger applies an over-voltage to the cell, which forces electrons to move from the positive to the negative electrode while lithium ions simultaneously move from the positive to the negative electrode through an electrolyte (Shu 1993). A diagram of this process is shown below in Figure 1 where the ions in solution are depicted as green circles.
Figure 1 (Diagram of a voltaic cell during intercalation (left) and after intercalation shown on the right)
This process is essentially the same for both sodium and lithium batteries with the only meaningful change in the process being the substitution of the sodium ion in place of the lithium ion.
Socio-environmental Consequences of Lithium-Ion Batteries
As mentioned earlier, the depleted lithium-ion cells contain harmful elements to the environment which must be properly regulated. This is one of the main drawbacks of the lithium-ion cell system, which is its complex life cycle. The lithium-ion life cycle is summarized in Figure 2.
Figure 2 (Summary of Lithium Battery Life Cycle)
As shown in Figure 2, the mass production of lithium-ion cells requires the mining of raw lithium, and the waste byproducts of depleted cells must be sorted and disposed of (Dai, 2019). Both processes are incredibly socioenvironmental and questionable. 53% of the world’s lithium content is mined in the so-called “lithium triangle” which consists of Chile, Argentina, and Bolivia. The lithium mined in these regions typically is sourced from land belonging to indigenous people with unethical mining practices (Murguía, 2024). The ethical concerns raised by mass lithium mining are a major reason why alternative sources must be explored.
Similar to other highly efficient fuel sources that are traditionally used in the energy sector, such as gasoline and other hydrocarbons, lithium is a nonrenewable resource. In 2022, 180000 tons of lithium were consumed which was a 22% increase from the previous year (U.S. Geological Survey, 2024). The trend of increasing lithium production annually is summarized in Figure 3. With increasing lithium consumption due to the demand caused by PEV lithium will eventually run out, making alternatives necessary. The complexity of the lithium supply chain leads to bottlenecks in the supply chain which drive lithium costs up (Olivetti, 2017). This problem is contributed to by the lack of recycling of lithium in batteries. According to a report by the United Nations Environment Programme (UNEP) less than one percent of lithium is recycled (Swain, 2017)
Figure 3 (Annual worldwide lithium production based on US geological survey data)
Lithium mining also damages the local ecosystem through water pollution and ecological damage. Lithium is mined through a process called brining, where underground water is pumped to the surface and evaporated (Khalil, 2022). While cost-efficient, this process releases pollutants into freshwater, causes salinization of groundwater, and depletes freshwater reservoirs (Lakshman, 2024). Environmental damage due to lithium mining has been documented globally, with researchers identifying water pollution in the Jinjiang River (Yang, 2024) and north Chile (Figueroa, 2012).
2.3. Safety Issues with Lithium-Ion Batteries
While their incredible efficiency has led to their widespread use, one major issue with lithium-ion batteries is the safety risks associated with their use. According to the National Fire Protection Agency (NFPA), the risk of overheating, short-circuiting, and explosion dramatically increases when the battery is damaged or improperly constructed. This safety issue came to mainstream media attention after a series of explosions occurred in the Samsung Galaxy Note 7 smartphone (Lan, 2023) which were a result of internal short circuits and incorrect electrode lengths (Lan, 2023). Following the 2017 recall of the Note 7, the U.S. Consumer Product Safety Commission reported 25,000 incidents involving defective lithium-ion batteries.
The primary source of lithium-ion defects is a result of thermal runaway. Thermal runaway refers to a dangerous phenomenon where the battery rapidly and uncontrollably heats, potentially causing the battery to vent gas, smoke, catch fire, or even explode. The main causes of this phenomenon include mechanical, thermal, and electrical abuse (Shahid, 2022) which are outlined in Table 1. Some important terms to define include deposition and overcharging. Deposition refers to the gain in mass of the cathode due to the reduction of ions and overcharging refers to the excessive charging of a voltaic cell beyond its capacity (Ohsaki, 2005).
Table 1 (Causes and Results of Mechanical/Thermal/Electrical Abuse)
|
Mechanical Abuse |
Thermal Abuse |
Electrical Abuse |
Causes |
Collisions Local forces Squeezing/bending |
Poor battery design Airborne combustibles |
Inconsistency of cells Electrolyte decomposition Excessive deposition1 Anode/cathode contact |
Results |
Internal short circuits Thermal runaway |
Rapid oxygen generation Explosions Overcharging2 Production of volatile side products |
Continuous Li+ release Overcharging2 Oxygen release Thermal runaway |
While these issues are still present in sodium-ion batteries, they happen to a far lesser extent because of sodium's lower energy density (Li, 2025).
Factors Affecting Battery Life in Sodium and Lithium Batteries
It is also important to note that even pristine care of a perfectly designed battery will result in a gradual loss of efficiency. This is because every time the battery is recharged it is so slightly chemically altered, a phenomenon referred to as battery degradation (Edge, 2021). Battery efficiency is also affected by the formation of solid electrolyte interphase (SEI). SEI refers to an electronically insulating layer formed where the electrode and electrolyte meet which is caused by the decomposition of the electrolyte (Peled, 2017). The formation of this layer can help to slow down the degradation of a battery by preventing the decomposition of the electrolyte and reducing damage to the electrode (Wang, 2022). Even in the presence of SEI, a battery will inevitably be depleted and after an ion cell is fully depleted, all that remains is the cell casing, electrodes, and an electrolyte solution depleted of lithium ions.
Sodium Battery Design
Sodium batteries function on a similar principle to lithium-ion batteries. They are composed of anode, cathode, and electrolyte with the role of the anode being performed by sodium. Most commonly, sodium cells use diatomic oxygen combined with sodium ions to produce sodium peroxide as shown in reaction 6 (Song, 2017).
2Na+ + 2e- + O2 → Na2O2 (6)
Comparisons of both Na2O2 and Li2O2 show that both compounds have extremely similar hexagonal crystal structures, but sodium peroxide has roughly half of the energy density of lithium peroxide. Lithium is also considerably more conductive and has a higher cell voltage, likely due to a larger band gap (Song, 2017).
Table 3 (Sodium and Lithium Peroxide, adapted from Song et. Al)
|
Energy Density (W h kg-1) |
Energy Density (W h L-1) |
Potential (V) |
Band Gap (eV) |
Conductivity (S cm-1) |
Li2O2 |
3456 |
7983 |
2.96 |
4.60 |
5 x 10-20 |
Na2O2 |
1602 |
4493 |
2.33 |
2.94 |
1 x 10-20 |
For all of these reasons, it remains unlikely that sodium can completely replace lithium for extremely small batteries. Instead, it can be used in combination with lithium for PEV and large-scale energy storage (Muhammed, 2022). New developments in sodium battery materials have led to developments that could pave the way for lower-cost sodium-ion batteries that can compete with lithium-ion batteries for large-scale grid energy storage.
Characteristics of Sodium-Ion Batteries
Table 4 (Characteristics of Lithium and Sodium, adapted from Chayambuka, 2018)
|
Atomic mass [g mol−1] |
Cationic radius [Å] |
Standard electrode potential [V] |
First ionization energy [kJ mol−1] |
Theoretical gravimetric capacity [mAh g−1 ] |
Theoretical volumetric capacity [mAhcm−3] |
Li |
6.94 |
0.76 |
-3.04 |
520.2 |
3861 |
2062 |
Na |
22.99 |
1.02 |
-2.71 |
495.8 |
1165 |
1131 |
The properties of sodium and its energy inferiority to lithium are due to the chemical properties of the metals themselves. Sodium has lower gravimetric and volumetric capacities due to its greater cationic radius, as shown in Table 4. Like all batteries, sodium-ion batteries have performance degradation at low voltages. The performance of sodium batteries is inhibited by the degradation of SEI at low temperatures which was discovered by researchers using impedance analyses, ex-situ X-ray photoelectron spectroscopy, and operando optical sensing (Desai, 2022). Despite this, 0V stable cells can be manufactured with relative ease. This is because sodium-ion cells use current collectors that are resistant to oxidation which enables zero voltage stability (Desai, 2022). Lithium batteries do not share the same characteristics, which explains why lithium batteries are widely regarded as unstable at low voltages (Ong, 2011). Another notable physical difference between the two metals is their ionic conductivity as an electrolyte in a battery. In the battery industry, lithium salt polymer electrolytes have been the most widely used electrolyte in next-generation batteries. This has been called into question by recent research which indicates that Na+ ions provide a comparable conductivity to that of Li+ ions in the same basic material when compared with impedance spectroscopy (Fuentes, 2024).
Lithium salt polymer electrolytes have been the most convenient, and thus the most widely used in the design of the new generation of batteries. However, in recent research it has been observed that Na+ ions provide higher conductivity, or at least a comparable conductivity to that of Li+ ions in the same basic material (Fuentes, 2017). This is contributed to novel methods of improving conduction such as doping (Fu, 2024 and Yu, 2022) and (Radjendirane, 2024).
Soda Ash
Soda ash, often called washing soda, is a colloquial name given to sodium carbonate (Na2CO3). In the environment, it is often found as a mineral deposit most commonly referred to as “trona” (Glanville, 1973). Naturally occurring sodium carbonate can be processed and purified in a process patented by Allan Turner which involves combining trona with saturated sodium carbonate solution at 117° C and then cooling and collecting the crystals (Turner, 2000). Alternatively, it can be synthetically produced using the Solvay process which involves limestone (CaCO3) reacting with a cold saturated sodium chloride solution in the presence of ammonia (NH3) outlined in Figure 4.
Figure 4 (Reaction mechanism of the Solvay process, adapted from Creative Commons)
The production of soda ash via the Solvay method and its synthesis from trona is essential to producing high-purity sodium compounds, which are used as electrodes in sodium batteries. The efficient and scalable production of soda ash from trona, with its lower environmental impact compared to the Solvay process, is critical for supporting the growing demand for sodium-ion batteries.
Benefits of Sodium-Based Batteries
Due to their superior energy density, much early research into ion batteries was focused on lithium rather than sodium. Recently, with rising lithium costs and concerns over scarcity, there has been an explosion of research into sodium as a possible substitute (Delmas, 2018). The reason for this is due to the abundance of sodium. In Earth's crust, sodium is 1,180 times more concentrated than sodium, as shown in Table 2 which outlines the difference in concentration of both metals in both the Earth’s crust and the oceans. This makes sodium far more available than lithium for use in batteries and a viable option to replace lithium as the primary metal used in cells for some sectors.
Table 2 (Sodium and Lithium Concentrations. Source: CRC Handbook of Chemistry and Physics 103rd Edition (2022-2023))
|
Crust (mg/kg) |
Sea (mg/L) |
Sodium |
2.36 × 104 |
1.08 × 104 |
Lithium |
2.0 × 101 |
1.8 × 10-1 |
The scarcity of lithium when compared to sodium, as shown in Table 2, is reflected in the difference between prices. Before the swell in demand for batteries, lithium was wholesaled for $5000/ton while sodium can be priced at $150/ton (Slater, 2012). Following the explosion in lithium battery usage the price disparity continued to grow as supply chain shortages in lithium production occurred (Egbue, 2012). This price difference is the main reason for the explosion of research into sodium batteries to fill the gaps in certain niche industries where lithium cannot be sourced in high enough quantities. The price of lithium has continued to increase with lithium prices increasing at a compound annual growth rate of 23% from 2018-2022 according to the 2023 Mineral Commodity Survey performed by the US Geological Survey. The same survey points out the disparity of price on the raw material level with one metric ton of soda ash costing 140$ compared to the $37,000 cost of one metric ton of lithium carbonate as of 2023.
Challenges of Sodium Batteries
Several challenges have yet to be addressed in the field of sodium batteries, one of which is its sustainability. Much research into sodium-ion batteries involves increasing the lifespan of sodium-ion batteries (Fang, 2018), (Peng, 2023), (Song, 2023), (Wang, 2017), (Zhang, 2018) which has the benefit of reducing the number of used batteries that end up in landfills. The lifespan of a sodium battery is dependent on several optimizations of cell design including electrode materials and design (Tapia-Ruiz et al, 2021). In order to make sodium cells last longer, many researchers have sought to stabilize the interface between electrode and electrolyte which is particularly difficult for sodium when compared to lithium. This difference results in lithium generally having a longer life cycle than sodium (Darwiche, 2016) which is a major challenge that must be overcome to make sodium batteries more sustainable. Fortunately, much of the innovation in lithium-ion batteries can be translated into the design of sodium batteries due to similarities in their structure.
Battery Disposal
The disposal of battery waste is also a major issue with ion batteries. There are several ways to recycle batteries sustainably. The first is referred to as direct recycling, which is the physical separation of the anode and cathode sections with the materials reused to make future cells. Alternatively, pyrometallurgical or hydrometallurgical methods can be used to recoup precious battery components using thermal energy and aqueous solutions respectively (Bird, 2022). Unfortunately, the lack of legislature mandating or incentivizing recycling (Bird, 2022) has led to minimal recycling by large corporations. The ecological, ethical, and environmental issues associated with batteries are another driving factor that leads researchers to find ways to improve the recyclability of cells. This can be done by minimizing the use of polymeric binders which are adhesives used to hold the electrodes together. The removal of these binders can improve energy density (Tapia-Ruiz et al, 2021) and make end-of-life disposal of electrodes easier. One novel method has been proposed by researchers at Lawrence Berkeley National Laboratory using biomass-based binders derived from cellulose (Taskin, 2021). Binders of this kind have the benefit of being water-soluble, which makes it easier to recycle.
Thermal Variance
While lithium-ion batteries have extensively documented losses in performance in low temperatures and increased battery aging in high temperatures, there are very few papers that explore similar phenomena in sodium-ion batteries (Velumani, 2022). While similar issues are predicted to arise in sodium, the actual degree to which this degradation will occur is slightly different.
At lower temperatures, a drop in performance in sodium-ion batteries occurs primarily due to the liquid electrolyte used in these batteries. Aqueous liquid electrolytes, which are used for their low cost and viscosity, suffer a major drawback of a high freezing point (Zhang, 2024). Alternatively, organic liquid electrolytes can be used to circumvent this weakness. Organic liquid electrolytes can be combined to form a mixture that can best meet the requirements the battery needs by maximizing the ionic conductivity and SEI formation while minimizing the viscosity at a wider temperature range (Wang, 2022). This can be circumvented by increasing the concentration of electrolytes such as in the case of water in salt (WIS) electrolytes. WIS electrolytes have been proven to have superior performance and impressive SEI generation (Suo, 2017). Sodium-ion batteries typically operate at their best at higher than ambient temperatures, with much of the research into temperature effects focusing on bringing the optimal operation temperature down to intermediate temperatures between 100-170 °C (Hueso, 2013).
Overview of Sodium-Ion Battery Research
Sodium-Ion Batteries as a Drop-In Solution
In the pursuit of sustainability, one important characteristic of any proposed alternative fuel source is its ability to act as a “drop-in” solution, or seamlessly integrate into existing infrastructure with minimal initial investment. Due to the similar chemical properties of lithium and sodium and the nearly identical design of their ion batteries, sodium can act as a drop-in solution. For example, to account for the predicted rise in demand for cells caused by increased interest in electric vehicles some companies have turned to sodium-based cells for usage in PEV. CATL, a major Chinese battery manufacturer, has launched full-scale sodium battery packs for electric vehicles and invested heavily in technology that integrates sodium and lithium into the same battery pack (Hu, 2021). Another industry that is investing in sodium-ion batteries is grid storage. The grid storage industry refers to a large energy storage system that helps to store large quantities of energy for usage depending on the needs of the consumer by storing excess energy and providing energy when a deficiency occurs (Chen, 2020). Sodium-ion batteries can play a valuable role in grid storage due to their environmental abundance, and competitive energy storage capacity (Hirsh, 2020). The industry standard for grid storage is lithium-ion batteries, reflected by their 77% usage in stabilizing power storage systems in the USA (Chen, 2020). The usage of lithium batteries in grid storage is not without its flaws, however, as the usage of lithium-ion batteries has its associated safety risks because of overcharge and thermal runaway between cells connected in series (Chen, 2020). Sodium cells can easily be modified to use the same processing and manufacturing methods as lithium-ion batteries, meaning no new manufacturing lines must be made and no new infrastructure is required. Although this is a major benefit for sodium batteries as a replacement, this limits the design of the batteries themselves (Tapia-Ruiz et. al, 2021). This is because the existing infrastructure to make lithium-ion cells has defined standards for the design that are not optimized for sodium (Tapia-Ruiz et. al, 2021). Regardless of this, the ability of sodium to seamlessly integrate into regions previously occupied by lithium, such as grid storage is a major financial incentive for corporations to use sodium, ion batteries.
Research Into Anode Selection for Sodium-Ion Batteries
In order to find a suitable anode for sodium batteries, one commonly used material is hard carbon. Hard carbon is typically used as an anode due to the tendency of sodium ions to fill disordered carbon layers rather than the layers of intercalated carbon used in lithium-ion batteries (Zhao, 2017). The usage of carbon also avoids the production of dendrites which are microscopic structures that reduce the overall efficiency of the battery (Lee, 2024). In addition to organic anode, recent research has focused on transition-metal oxides due to their relatively low cost. Particularly, titanium-based anodes have been explored due to their relatively low cost (Zhao, 2017).
Other recent innovations in anodes focus on improving their sustainability. One method to do this was recently proposed by Zhou et al which explores the development of hard carbon-based anodes that are derived from olive-shell biomass. The anodes made using this method were characterized by good sodium storage capacity, which diminishes by a mere 13% capacity after 1000 cycles at 1000 mA g−1. This indicates that carbon-based anodes using biomass is an acceptable anode for use in high-capacity sodium batteries (Zhou, 2025). Hard carbon does suffer its drawbacks, such as low electrical conductivity and volume expansion. To solve these issues, some researchers propose soft carbon anodes which are structural intermediates between graphite and hard carbon (Qi, 2025). Soft carbon anodes have seen little widespread use, but some researchers find interest in their properties in combination with hard carbon anodes. When soft carbon coats hard carbon anodes to form a hybrid electrode, promising results indicate that the electrode can be a viable choice for industrial applications. The hybrid electrode demonstrates a reversible specific capacity of 335.3 mAh g−1 at 30 mA g−1 and an initial coulombic efficiency of 86.8%. They were also found to be viable long-term, and they retained 95.2% of their capacity after 150 cycles at 300 mA g-1 (Kuai, 2025). Other hybrid anodes have been recent topics of interest, especially anodes that involve waste materials of other chemical processes. For example, Dongsheng et al recently proposed a hybrid electrode derived from petroleum coke and glucose. 5.3. Anode Free Cells
Another recent breakthrough in the selection of electrodes for batteries is “anode-free” cells. An anode-free or anode-less cell refers to a unique design of an electrochemical cell that involves multiple steps that eliminate the need for a solid electrode. The initial configuration of the cell consists of a cathode, a current collector (serving as the anode during operation), and an electrolyte that facilitates the movement of ions. At the start, the current collector does not contain any pre-deposited lithium, sodium, or other active material. During charging, metal ions are extracted from the cathode and move through the electrolyte towards the current collector. The ions are then reduced and deposited as a metallic layer directly on the surface of the current collector. When discharging occurs, the deposited metal oxidizes and the ions are released back into the electrolyte where they migrate back to the cathode (Zhao, 2023). These batteries have the advantage of not requiring a solid anode which drastically reduces the weight of the battery and improves the energy density of the cell by allowing more space for cathode material (Zhao, 2023). The elimination of potentially volatile metals in the production and consumption of anode-free cells also makes them more environmentally sustainable and improves the safety of these cells. Lithium anode-free cells have been a topic of great interest amongst researchers which culminated in a recent patent by Tesla. Similar batteries using sodium were created but face drawbacks such as unstable changes to the anodes morphology and interactions at the anode-electrolyte interface (Deysher, 2024). Regardless of this these batteries were shown to last several hundred cycles (Deysher, 2024) and have superior energy densities to traditional sodium-ion designs (Chen, 2024).
Research Into Cathode Selection for Sodium-Ion Batteries
Much research has gone into finding suitable cathodes for sodium-ion batteries. The most well-researched cathode is the usage of sodium-layered transition metal oxides, a type of material where sodium ions are layered between sheets of transition metal oxide (Zuo, 2023). Several transition metals have been tested, with nickel oxides being proposed as a feasible option with manganese and cobalt alternatives (Guo, 2024). Cobalt oxides are considered to be a feasible “drop-in” solution since they are seen as analogous to the commonly used lithium counterpart but typically fail to match the performance due to the higher atomic radius of the sodium ion. Other cathodes include tunnel-type oxides where the oxygen atoms are arranged in a way that creates interconnected channels or "tunnels" within the crystal lattice (Feng, 2022). Research into these novel cathodes has dramatically improved the competitiveness of sodium batteries but also has revealed some weaknesses in the batteries' structure. Layered type oxides have poor air/moisture stability which was reported by Zhang and Yao. With the advent of novel battery designs such as anode-free cells, the improvements of cathodes help to improve the energy density of sodium cells to compete with lithium cells.
Recent Novel Methods of Improving Transition Metal Oxide Cathodes
Much of the research performed in the past five years to improve sodium battery cathodes has focused on improving existing metal oxide cathodes for use industrially. Notably, researchers have proposed doping and co-doping as methods to improve the electrochemical properties of metal oxide cathodes. Bibi et al successfully demonstrated the creation of several high-capacity electrode materials through a high-temperature solid-state co-doping reaction. When compared with a sodium-based layered oxide cathode material (NaNiFeMnO₂), an alternate electrode with titanium and copper co-doping outperformed its traditional counterpart with a initial discharge capacity of 124 mAh g−1 (Bibi, 2025). Other researchers
The Future of Sodium Batteries
Sodium batteries have begun to reach levels of demand that require large-scale production. In 2020, sodium-ion battery manufacturers Faradion received large orders in Australia and India to align with targets set by both countries to meet environmental standards (Faradion, 2020). Fortunately, since sodium and lithium batteries are so similar most factories that produce lithium batteries can also produce sodium-based batteries with little to no added investment. With the recent swell in battery demands, multiple “Gigafactories” have been made in order to meet the growing interest. These gigafactories can easily be adapted to produce sodium-ion batteries (Nekahi, 2024).
Even though the production of sodium batteries is feasible using existing infrastructure, the superiority of lithium in terms of energy density likely means that for the foreseeable future, sodium batteries will remain a secondary option that will not be used in many fields such as small portable electronic devices such as smartphones. Instead, sodium-based batteries will likely fill niches in the battery market such as large-scale grid storage and other large-scale deployments. With additional research and optimization, sodium can become a complementary fuel source that could help partially replace lithium. Interest in sodium-ion batteries continues to increase and the global sodium-ion battery is projected to increase to $838.5 million in 2029 at a compound annual growth rate of 18.6% from 2024 to 2029 (Arora, 2024).
Due to their early inferiority to lithium in terms of energy density, sodium batteries remain insufficiently researched. This trend seems to be changing, however, with an increase in publications occurring in the early 2010s, likely due to lithium scarcity becoming an increasing topic of discussion. These trends are reflected in figure 7 & 8 showing increasing interest in sodium-ion batteries as a solution to the looming exhaustion of lithium reserves.
Figure 5 (Number of Publications mentioning “Sodium-Ion Battery” and “Lithium Scarcity” on Google Scholar by Year)
Applications of Soda Ash in Batteries
Soda ash has long since been an essential part of the production of lithium-ion batteries. The production of lithium carbonate electrodes requires soda ash to be used to convert lithium-rich brine into lithium carbonate via precipitation (Tran, 2015). It is also used to recover lead in battery residue by carbothermic reduction (Guerrero, 1997). Recently, soda ash and its application as a source of sodium for sodium-ion batteries has been a trending field of research. Peak Energy, a renewable energy storage startup, uses natural sources of sodium as a source of ions for use in their grid storage systems (Kamoji, 2023). The goal of using soda ash generated from trona is to massively reduce the cost of the electrodes and create more stability in the energy generation market. Due to soda ash having its cost remaining relatively constant, it remains a more consistent option than the lithium brine used to make the solid lithium used in batteries. Soda ash is the key to overcoming the bottleneck that exists in the grid storage market that results whenever lithium supply chain issues arrive.
Conclusion
The future of sodium-ion batteries holds significant promise as a sustainable alternative to traditional lithium-ion batteries, particularly in addressing global energy storage demands and resource limitations. Although sodium-ion batteries remain unable to compete with lithium-ion batteries in energy density, they remain a valuable complementary cell material. One of the most compelling aspects of sodium batteries is their reliance on sodium, an abundant and widely distributed element, unlike lithium, which is geographically concentrated and increasingly scarce. This abundance could reduce material costs and the geopolitical tensions associated with lithium mining, paving the way for more equitable energy solutions. In certain wide-scale deployments, such as medium-sized PEV and grid storage sodium cells have the potential to become the dominant cell material based on the low cost and abundance of soda ash, a commonly found material synthesized from trona. Sodium-ion batteries using soda ash have already been tested by electric vehicle companies in China and by US-based grid storage companies.
Sodium-ion batteries can dramatically improve the sustainability of the lithium supply chain by reducing the amount of lithium that must be mined using environmentally damaging practices. The extraction of lithium often involves energy-intensive processes that can harm local ecosystems and water supplies. Sodium, on the other hand, can be sourced more sustainably from soda ash. Due to the abundance of soda ash, batteries that use them can also be used in times of need as a substitute for lithium when bottlenecks in the lithium supply chain occur. Sodium-based batteries can also be mass-produced using existing infrastructure. For the past two decades, an explosion of research into sodium batteries has resulted in innovations in the sustainability of batteries such as improvements in anode and cathode materials and more sustainable cell materials which make the batteries have a longer life cycle and improve their recyclability. Additional innovations such as the development of advanced carbon anodes and layered oxide cathodes, have significantly improved energy density and cycle life—two areas where sodium batteries have traditionally lagged behind lithium-ion counterparts. Researchers are also making strides in enhancing the stability and performance of electrolytes, which are crucial for improving the efficiency and safety of these batteries.
Despite these advances, challenges remain. Sodium batteries generally have a lower energy density compared to lithium-ion batteries, which means they store less energy for the same weight or volume. This limitation makes them less suitable for applications requiring high energy density, such as long-range electric vehicles. However, for stationary energy storage systems, such as those used to store energy from solar and wind power, sodium batteries are highly competitive due to their lower cost and better performance in large-scale deployments. Additionally, ongoing research into hybrid systems that combine sodium with other materials aims to overcome energy density constraints, further expanding their applicability. The global energy landscape is shifting toward a future that prioritizes sustainability and resource efficiency, and sodium-ion batteries are well-positioned to contribute significantly to this transition. With continued research, investment, and industrial scaling, sodium batteries could complement or even partially replace lithium-ion systems in many areas, reducing reliance on critical raw materials and supporting the broader adoption of renewable energy. As these technologies mature, sodium batteries have the potential to reshape energy storage paradigms, fostering a cleaner, more sustainable, and more inclusive energy future.
Authors
Dr. Raj Shah is a Director at Koehler Instrument Company in New York, Holtsville, NY. He is an elected Fellow by his peers at IChemE, CMI, STLE, AIC, NLGI, INSTMC, AOCS, Institute of Physics, The Energy Institute and The Royal Society of Chemistry. An ASTM Eagle award recipient, Dr. Shah recently coedited the bestseller, “Fuels and Lubricants handbook”, details of which are available at ASTM’s Long-Awaited Fuels and Lubricants Handbook 2nd Edition Now Available (https://bit.ly/3u2e6GY). He earned his doctorate in Chemical Engineering from The Pennsylvania State University and is a Fellow from The Chartered Management Institute, London. Dr. Shah is also a Chartered Scientist with the Science Council, a Chartered Petroleum Engineer with the Energy Institute and a Chartered Engineer with the Engineering council, UK. Dr. Shah was recently granted the honourific of “Eminent engineer” with Tau beta Pi, the largest engineering society in the USA. He is on the Advisory board of directors at Farmingdale university (Mechanical Technology) , Auburn Univ ( Tribology ), SUNY, Farmingdale, (Engineering Management) and State university of NY, Stony Brook ( Chemical engineering/ Material Science and engineering). An Adjunct Professor at the State University of New York, Stony Brook, in the Department of Material Science and Chemical engineering, Raj also has approximately 700 publications and has been active in the energy industry for over 3 decades. More information on Raj can be found at https://bit.ly/3QvfaLX
Contact: rshah@koehlerinstrument.com
Dr. Vikram Mittal, PhD is an Associate Professor in the Department of Systems Engineering at the United States Military Academy. His research interests include energy modeling, technology forecasting, and Alternative fuels. Previously, he was a senior mechanical engineer at the Charles Stark Draper Laboratory. He holds a PhD in Mechanical Engineering from MIT, an MS in Engineering Sciences from Oxford, and a BS in Aeronautics from Caltech. Dr. Mittal is also a combat veteran and a major in the U.S. Army Reserve.
Mr. Mathew Roshan is part of a thriving internship program at Koehler Instrument company in Holtsville, and is a student of Chemical Engineering at Stony Brook University, Long Island, NY where Dr.’s Shah and Mittal are on the external advisory board of directors.
Works Cited
Arora, Karishma. “Sodium-Ion Batteries Market Trends and Innovations to Watch.” BCC Research Blog, BCC Research, 24 Oct. 2024, blog.bccresearch.com/sodium-ion-batteries-market-trends-and-innovations-to watch#:~:text=Offering%20affordability%2C%20sustainability%2C%20and%20efficiency%2C%20sodium%2Dion%20batteries,ranging%20from%20renewable%20energy%20to%20electric%20vehicles.&text=The%20global%20market%20for%20sodium%2Dion%20batteries%20(SIB),(CAGR)%20of%2018.6%%20from%202024%20through%202029.
Bibi, Safia, et al. “Unleashing the electrochemical potential of NaNiFeMnO2 layered oxide cathodes through titanium and copper co-enhancement for sodium ion batteries.” Journal of Electroanalytical Chemistry, vol. 978, Feb. 2025, p. 118870, https://doi.org/10.1016/j.jelechem.2024.118870.
Bird, Robert, et al. “The regulatory environment for Lithium-Ion Battery Recycling.” ACS Energy Letters, vol. 7, no. 2, 20 Jan. 2022, pp. 736–740, https://doi.org/10.1021/acsenergylett.1c02724.
Chayambuka, Kudakwashe, et al. “Sodium‐Ion battery materials and electrochemical properties reviewed.” Advanced Energy Materials, vol. 8, no. 16, 30 Apr. 2018, https://doi.org/10.1002/aenm.201800079.
Chen, Tianmei, et al. “Applications of lithium-ion batteries in grid-scale energy storage systems.” Transactions of Tianjin University, vol. 26, no. 3, 8 Feb. 2020, pp. 208–217, https://doi.org/10.1007/s12209-020-00236-w.
Chen, Yujie, et al. “Prospects for practical anode-free sodium batteries.” Materials Today, vol. 73, Mar. 2024, pp. 260–274, https://doi.org/10.1016/j.mattod.2024.01.002.
Dai, Qiang, et al. “Life cycle analysis of lithium-ion batteries for Automotive Applications.” Batteries, vol. 5, no. 2, 1 June 2019, p. 48, https://doi.org/10.3390/batteries5020048.
Darwiche, Ali, et al. “Impact of the salts and solvents on the SEI formation in SB/Na batteries: An XPS analysis.” Electrochimica Acta, vol. 207, July 2016, pp. 284–292, https://doi.org/10.1016/j.electacta.2016.03.089.
Delmas, Claude. “Sodium and sodium‐ion batteries: 50 Years of research.” Advanced Energy Materials, vol. 8, no. 17, 19 Feb. 2018, https://doi.org/10.1002/aenm.201703137.
Desai, Parth, et al. “Zero volt storage of na-ion batteries: Performance dependence on cell chemistry!” Journal of Power Sources, vol. 551, Dec. 2022, p. 232177, https://doi.org/10.1016/j.jpowsour.2022.232177.
Deysher, Grayson, et al. “Design principles for enabling an anode-free sodium all-solid-state battery.” Nature Energy, 3 July 2024, https://doi.org/10.1038/s41560-024-01569-9.
Edge, Jacqueline S., et al. “Lithium-ion battery degradation: What you need to know.” Physical Chemistry Chemical Physics, vol. 23, no. 14, Mar. 2021, pp. 8200–8221, https://doi.org/10.1039/d1cp00359c.
Egbue, Ona, and Suzanna Long. “Critical issues in the supply chain of lithium for electric vehicle batteries.” Engineering Management Journal, vol. 24, no. 3, 20 Sept. 2012, pp. 52–62, https://doi.org/10.1080/10429247.2012.11431947.
Fang, Yongjin, et al. “A fully sodiated Navopo4 with layered structure for high-voltage and long-lifespan sodium-ion batteries.” Chem, vol. 4, no. 5, May 2018, pp. 1167–1180, https://doi.org/10.1016/j.chempr.2018.03.006.
Faradion 2020 Press release: faradion announces major partnership for developing sodium-ion batteries for commercial vehicles in India (available at: www.faradion.co.uk/faradion-announces-partnership-for-developing-sodium-ion-batteries-in-india/) (Accessed 3 Jan 2025)
Feng, Jie, et al. “Research progress of tunnel-type sodium manganese oxide cathodes for SIBS.” Chinese Chemical Letters, vol. 33, no. 5, May 2022, pp. 2316–2326, https://doi.org/10.1016/j.cclet.2021.09.077.
Figueroa, L., et al. “Environmental lithium exposure in the north of Chile—I. natural water sources.” Biological Trace Element Research, vol. 149, no. 2, 12 May 2012, pp. 280–290, https://doi.org/10.1007/s12011-012-9417-6.
Fu, Yuan, et al. “Zn doping for enhanced sodium-ion conductivity and air stability in NA3SBS4 solid electrolyte.” Journal of Materials Science, vol. 59, no. 7, Feb. 2024, pp. 3009–3017, https://doi.org/10.1007/s10853-023-09263-z.
Fuentes, Isabel, et al. “Enhanced conductivity of sodium versus lithium salts measured by impedance spectroscopy. Sodium Cobaltacarboranes as electrolytes of choice.” Physical Chemistry Chemical Physics, vol. 19, no. 23, 31 May 2017, pp. 15177–15186, https://doi.org/10.1039/c7cp02526b.
Glanville, Jim, and Eric Rau. “Soda ash manufacture - an example of what?” Journal of Chemical Education, vol. 50, no. 1, Jan. 1973, p. 64, https://doi.org/10.1021/ed050p64.
Guerrero, A., et al. “Thermodynamic analysis of the soda ash smelting of lead acid battery residue in a Rotary Furnace.” Canadian Metallurgical Quarterly, vol. 36, no. 2, Apr. 1997, pp. 121–130, https://doi.org/10.1179/cmq.1997.36.2.121.
Guo, Yu-Jie, et al. “Sodium layered oxide cathodes: Properties, practicality and prospects.” Chemical Society Reviews, vol. 53, no. 15, 30 Apr. 2024, pp. 7828–7874, https://doi.org/10.1039/d4cs00415a.
Hirsh, Hayley S., et al. “Sodium‐ion batteries paving the way for grid energy storage.” Advanced Energy Materials, vol. 10, no. 32, 6 July 2020, https://doi.org/10.1002/aenm.202001274.
Hu, Yong-Sheng, and Yuqi Li. “Unlocking sustainable NA-ion batteries into industry.” ACS Energy Letters, vol. 6, no. 11, 12 Nov. 2021, pp. 4115–4117, https://doi.org/10.1021/acsenergylett.1c02292.
Hueso, Karina B., et al. “High temperature sodium batteries: Status, challenges and future trends.” Energy & Environmental Science, vol. 6, no. 3, 11 Jan. 2013, p. 734, https://doi.org/10.1039/c3ee24086j.
Kamoji, Jerusha. “USA: Peak Energy to Set up Domestic Market for Sodium-Ion Batteries.” Pv Magazine India, pv Magazine, 27 Oct. 2023, www.pv-magazine-india.com/2023/10/27/usa-peak-energy-to-set-up-domestic-market-for-sodium-ion-batteries/.
Khalil, Abdullah, et al. “Lithium recovery from brine: Recent developments and challenges.” Desalination, vol. 528, Apr. 2022, p. 115611, https://doi.org/10.1016/j.desal.2022.115611.
Kuai, J., et al. “Optimizing hard carbon materials for sodium-ion batteries: Insights from particle size and soft carbon-coating strategy.” Journal of Power Sources, vol. 627, Jan. 2025, p. 235792, https://doi.org/10.1016/j.jpowsour.2024.235792.
Lakshman, Shivani. “More Critical Minerals Mining Could Strain Water Supplies in Stressed Regions.” More Critical Minerals Mining Could Strain Water Supplies in Stressed Regions, World Resources Institute, 10 Jan. 2024, www.wri.org/insights/critical-minerals-mining-water-impacts#:~:text=This%20evaporation%20method%20uses%20up,graphite%20in%20China%2C%20among%20others.
Lan, Tianlan. “A critical case report of Samsung Note 7 recall.” Frontiers in Art Research, vol. 5, no. 11, 2023, https://doi.org/10.25236/far.2023.051101.
Lee, Sang Jun, et al. “Stable sodium-metal batteries with a hierarchical structured electrode toward reversible confinement of Na dendrites.” Energy Storage Materials, vol. 64, Jan. 2024, p. 103047, https://doi.org/10.1016/j.ensm.2023.103047.
Li, Matthew, et al. “30 years of lithium‐Ion Batteries.” Advanced Materials, vol. 30, no. 33, 14 June 2018, https://doi.org/10.1002/adma.201800561.
Li, Zhiyuan, et al. “Thermal runaway comparison and assessment between sodium-ion and lithium-ion batteries.” Process Safety and Environmental Protection, vol. 193, Jan. 2025, pp. 842–855, https://doi.org/10.1016/j.psep.2024.11.118.
"Mineral Commodity Summaries 2023. U.S. Geological Survey, January 2023.
Muhammed Hafiz, N S, et al. “Next generation sodium-ion battery: A replacement of Lithium.” Materials Today: Proceedings, Dec. 2022, https://doi.org/10.1016/j.matpr.2022.11.245.
Murguía, Diego I, and Martín Obaya. “Exploring conditions for just lithium mining in South America. the case of the EU responsible sourcing strategy.” Environmental Research Letters, vol. 19, no. 12, 1 Dec. 2024, p. 124098, https://doi.org/10.1088/1748-9326/ad948d.
Nekahi, Atiyeh, et al. “Comparative issues of metal-ion batteries toward sustainable energy storage: Lithium vs. sodium.” Batteries, vol. 10, no. 8, 4 Aug. 2024, p. 279, https://doi.org/10.3390/batteries10080279.
Ohsaki, Takahisa, et al. “Overcharge reaction of lithium-ion batteries.” Journal of Power Sources, vol. 146, no. 1–2, Aug. 2005, pp. 97–100, https://doi.org/10.1016/j.jpowsour.2005.03.105.
Olivetti, Elsa A., et al. “Lithium-ion battery supply chain considerations: Analysis of potential bottlenecks in critical metals.” Joule, vol. 1, no. 2, 11 Oct. 2017, pp. 229–243, https://doi.org/10.1016/j.joule.2017.08.019.
Ong, Shyue Ping, et al. “Voltage, stability and diffusion barrier differences between sodium-ion and lithium-ion intercalation materials.” Energy & Environmental Science, vol. 4, no. 9, 2 Aug. 2011, p. 3680, https://doi.org/10.1039/c1ee01782a.
Peled, E., and S. Menkin. “Review—sei: Past, present and future.” Journal of The Electrochemical Society, vol. 164, no. 7, 2017, https://doi.org/10.1149/2.1441707jes.
Peng, Jian, et al. “A disordered Rubik’s cube‐inspired framework for sodium‐ion batteries with Ultralong Cycle Lifespan.” Angewandte Chemie International Edition, vol. 62, no. 6, 2 Jan. 2023, https://doi.org/10.1002/anie.202215865.
Qi, Tianshuang, et al. “Research progress of carbon materials in the anodes of sodium-ion batteries.” Journal of Power Sources, vol. 626, Jan. 2025, p. 235721, https://doi.org/10.1016/j.jpowsour.2024.235721.
Radjendirane, Aakash Carthick, et al. “Overview of inorganic electrolytes for all-solid-state sodium batteries.” Langmuir, vol. 40, no. 32, 30 July 2024, pp. 16690–16712, https://doi.org/10.1021/acs.langmuir.4c01845.
Shahid, Seham, and Martin Agelin-Chaab. “A review of Thermal runaway prevention and mitigation strategies for lithium-ion batteries.” Energy Conversion and Management: X, vol. 16, Dec. 2022, p. 100310, https://doi.org/10.1016/j.ecmx.2022.100310.
Sheldon, Tamara L., et al. “How cost-effective are electric vehicle subsidies in reducing tailpipe-CO2 emissions? an analysis of major electric vehicle markets.” The Energy Journal, vol. 44, no. 3, May 2023, pp. 223–250, https://doi.org/10.5547/01956574.44.2.tshe.
Shu, Z. X., et al. “Electrochemical intercalation of lithium into graphite.” Journal of The Electrochemical Society, vol. 140, no. 4, 1 Apr. 1993, pp. 922–927, https://doi.org/10.1149/1.2056228.
Slater, Michael D., et al. “Sodium‐Ion Batteries.” Advanced Functional Materials, vol. 23, no. 8, 21 May 2012, pp. 947–958, https://doi.org/10.1002/adfm.201200691.
Song, Kyeongse, et al. “High‐energy‐density metal–oxygen batteries: Lithium–oxygen batteries vs sodium–oxygen batteries.” Advanced Materials, vol. 29, no. 48, 21 Sept. 2017, https://doi.org/10.1002/adma.201606572.
Song, Xuexia, et al. “V-O-C bonding of heterointerface boosting kinetics of free‐standing na5V12O32 cathode for ultralong lifespan sodium‐Ion Batteries.” Advanced Functional Materials, vol. 34, no. 5, 8 July 2023, https://doi.org/10.1002/adfm.202303211.
Suo, Liumin, et al. “‘water‐in‐salt’ electrolyte makes aqueous sodium‐ion battery safe, green, and
The content & opinions in this article are the author’s and do not necessarily represent the views of AltEnergyMag
Comments (0)
This post does not have any comments. Be the first to leave a comment below.
Featured Product
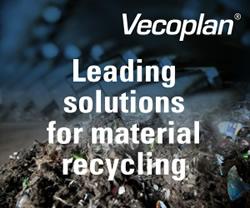