‘A 93% reduction in CO₂’: new report from Autocraft EV Solutions makes data-informed case for EV battery repair
The transition to electric vehicles (EVs) is well underway, but uncertainty around battery health remains a barrier to mass adoption. A report from Autocraft EV Solutions, a world leader in EV battery testing, repair and remanufacturing, challenges misconceptions around battery failure, presenting the case for repair over the conventional replace and recycle approach.
Titled ‘Closing the EV confidence gap: the role of battery remanufacturing’, the report draws on industry-leading in-warranty repair data and academically verified insights from the RECOVAS project, a collaboration between leading automotive businesses to quantify the impact of the battery life cycle, to demonstrate how remanufacturing can play a major role in boosting confidence in EV and preventing millions of tonnes of avoidable carbon emissions.
“Despite EV battery failure rates being very low, we need a better plan for when they do occur. The assumption that EV batteries need full replacement when a fault occurs is simply not true, given that most batteries can be repaired,” said Dr Sara Ridley, Engineering & Quality Director of Autocraft Solutions Group. “The mere possibility of battery failure undermines the perception of EVs, with many people unwilling to entertain the risk. Our goal is to change this narrative, giving buyers confidence that their EV batteries can be efficiently repaired rather than replaced at great expense or worse, prematurely scrapped.”
Contrary to common belief, entire EV batteries do not fail; individual cells do. With the right testing capability, it is possible to diagnose the root cause of failure, replace only the necessary components, and restore performance. Having successfully repaired thousands of in-warranty EV batteries on behalf of major OEMs, Autocraft is already demonstrating that this can be done at scale – and has the data to prove it.
Key report findings:
- Localised battery faults require targeted solutions – Based on in-warranty commercial repairs carried out by Autocraft in 2024, on average, only 1.1 modules needed to be replaced to restore a pack to optimal performance (above 90% of the original state-of-health)
- Same outcome, 93% CO2 reduction – For each battery (based on an 82.5 kWh pack) that is repaired instead of replacing and recycling it, 12 tonnes of avoidable carbon emissions is prevented
- 92% of modules in a “failed” battery are still suitable for automotive re-use – The benefits of utilising these critical components to repair other packs far outweighs any value derived from prematurely recycling them
To instil confidence in EVs and accelerate mass adoption, Autocraft’s report highlights three urgent industry-wide changes:
- Make battery repair the standard industry practice – For in-warranty battery failures, automakers can achieve substantial environmental and cost savings. Beyond the warranty period, the availability of reliable repair solutions eliminates much of the perceived risk of EV ownership, improving the market as a whole.
- End premature recycling of healthy battery components – While end-of-life recycling is necessary, the priority should be to reuse functional cells and modules whenever possible. Given the potential risk of future shortages of components which are integral to a sustainable repair process, this becomes all the more critical.
- Design EV batteries for repairability – Manufacturers and legislators must work together to ensure future battery designs allow for effective repairs, rather than making remanufacturing more difficult through increasingly complex architectures.
“A battery can only perform to the level of its weakest performing cell. Autocraft’s OptEVizer® dynamic testing protocols provide a comprehensive picture of battery state of health at a cellular level. While battery repair is far from simple, our REVIVE® remanufacturing capability means it can be done safely, reliably, and at scale. As EV adoption grows, consumer confidence in battery longevity and repairability will be crucial to sustaining momentum. By making battery repair an industry norm, we can help drive a stronger EV market,” explains Dr Ridley.
The data in this report is based on a sample group of 559 commercial repairs carried out in 2024, providing the most up-to-date picture of EV battery repair needs. Verified environmental data for the different stages of the battery life cycle was provided by different RECOVAS partners, with triage, repair and reassembly data provided by Autocraft. This allowed for an objective comparison of impact of a repair-focused approach compared with the default industry practice of replace-and-recycle.
For more information and to access the full report, please visit here.
Comments (0)
This post does not have any comments. Be the first to leave a comment below.
Featured Product
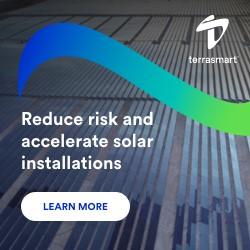