Thermal Storage Innovations are instrumental in increasing performance and reducing in CSP
Thermal storage will affect the Levelized Energy Cost (LCOE) of Parabolic Troughs. This is one of the findings of a new report from CSP Today "Concentrated Solar Power Parabolic Trough: Cost & Performance".
According to the report, when adding storage capacity, the capital cost rises with the increased solar field size, while the capacity factor - and therefore the annual energy yield - increases, (for example, <3700 hours at DNI 2000 for the reference plant with 7.5 hours of storage).
In the report, for each Thermal Energy Storage (TES) integer hour value, an optimal configuration was found regressively. As the model parameters were adjusted until the hours of storage reached a minimal LCOE cost. For this simulation, parasitic composition, O&M costs, component replacement frequency, and labour requirements were each adjusted to reflect the higher complexity of TES equipped plants. The resulting profitability impact was that a slight LCOE decrease can be observed from 5 to 10 hours of TES.
Finding how to achieve the most energy at the lowest cost from parabolic trough CSP is vital as parabolic trough accounts for more than 98% of total operating CSP plants and 70% of plants under construction.
The Concentrated Solar Power Parabolic Trough: Cost & Performance Report examines the technological, financial and commercial factors that shape the costs of Parabolic Trough CSP. The report's free selected findings are available to download at http://www.csptoday.com/parabolictrough/preview.shtml
For more information, please contact us:
Bea Gonzalez
CSP Today
bea@csptoday.com
CSP Today is a business unit of FC Business Intelligence providing focused news, events, reports, updates and information for the Concentrated Solar Thermal Power Industry.
Featured Product
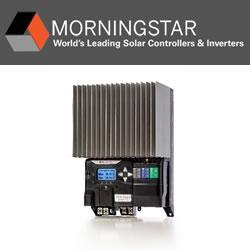
MORNINGSTAR - ReadyEdge
The ReadyEdgeTM (RE-1) accessory is an intelligent system controlling and reporting device meant to make monitoring your solar energy system more transparent. Enabling access to LiveViewTM 2.0 and Morningstar Solar ConnectTM, ReadyEdge provides data from all compatible Morningstar devices in your system. It is designed to be paired with the three ReadyBlock options, up to six total, with the possibility to use multiple ReadyShunts and ReadyRelays. The ReadyEdge is compatible with select Morningstar products.