After only three to six weeks of continuous operation, the power costs associated with low-rated electric motors and drives can already have equalled their purchase price.
Saving Energy With High Efficiency Motors
Stefan Fassbinder | Leonardo ENERGY
After only three to six weeks of continuous operation, the power costs associated with low-rated electric motors and drives can already have equalled their purchase price. |
![]() |
Stefan Fassbinder, Leonardo ENERGY |
Once upon a time there was a buyer at a large company who had to purchase a large three-phase induction motor with a power rating of 1 MW that was to be used in a big machine. As usual, he invited suppliers to submit bids. Before drafting the tender documents he spoke to the head engineer and technicians at the relevant technical department about the expected number of operating hours per year, the machine’s level of utilization and its load profile. Talks then began with potential suppliers about what sort of efficiencies could be achieved. As is normal, the buyer and supplier agreed on a penalty clause that would allow a price reduction to be imposed should the motor fall short of the efficiency level agreed in the sales contract. Equally, in the event of the motor exceeding specifications, the supplier would receive a bonus.
Once upon another time there was another buyer at another large company – or perhaps it was even the same buyer at the same company. This buyer needed to buy 1000 small three-phase induction motors each with a 1 kW rating that were to be built into the numerous small machines at his large company. He put out requests for quotes, specifying the voltage, design and configuration and the number of poles, and then placed his order with the cheapest supplier. The word ‘efficiency’ was nowhere to be seen: neither in the request for quotes, nor on the motor’s rating plates. Perhaps it was mentioned in the manufacturer’s catalogue, but, as so often, it remained unread. The sad thing about these two fairy tales is that they aren’t actually
fictional at all, but a fair description of current industrial
practice. Had we swapped the two stories, then we would at least have
avoided the most absurd aspect of the situation: the fact that large
motors are inherently far more efficient than small ones. 1 Room for improvement
After only three to six weeks of continuous operation, the power costs associated with low-rated electric motors and drives can already have equalled their purchase price. Anyone hearing this for the first time, doesn’t usually believe it; even the experts look sceptical and reach for their calculators. The initial response is often that in view of the already very high efficiency levels, there is little point spending time on trying to make further improvements. An almost identical reaction was evident when similar claims were first made about with operation of transformers.
Fig. 1: One third of all the electricity consumed is used to power electric motors and drives
Fig. 2: Reviewing efficiency levels is worthwhile whatever the size of the motor In Germany, about 536 TWh (2005) of electric power is consumed every year, half of which is used for industrial applications. Two thirds of that energy is in turn converted into useful mechanical energy in motors (Fig. 1). Given these overall orders of magnitude, it is well worth thinking about how efficiency can be improved – irrespective of the size of the motor (Fig. 2) – and despite the fact that improvements to an individual motor or drive might appear negligible at first sight. The preferential consideration given to the efficiencies of large motors is justified to the extent that, on average, large motors tend to live longer than smaller ones (Fig. 3). Nevertheless, the lifetime of a small motor is similar to that of an average car, the difference being that at that the end of its service life, it will have racked up twenty times the number of operating hours! Clearly, efforts to reduce the power consumption of a small electric motor by 1 % are going to be more worthwhile than attempts to lower fuel consumption in cars by 10 % (see Fig. 4).
Fig. 3: Larger motors live longer
Fig. 4: Purchase costs are almost laughably small when compared to energy costs. The example shown is for a standard 11 kW motor, with electricity costs of €0.066 per kWh, 3000 hours of full-load operation per year and a service life of 10 years. 2 Energy-efficient motors have been around for a long time
Typically, a standard off-the-shelf three-phase induction motor will have been designed not to maximize efficiency but to minimize manufacturing costs. But there are still a number of elements that can be designed differently to achieve appreciable savings (Fig. 5). In addition to a number of aspects that can be fine tuned for better performance, the main improvement comes from using more and / or better active materials, such as the die-cast copper squirrel-cage rotors that have recently reached a commerciable state of development (see section 8). In 1994, the German Copper Institute (DKI) decided to become more actively involved with the markets in the electrical engineering sector and employed a specialist for this purpose – an understandable move given that these markets account for 60 % of all copper used. The DKI specialist looked into the question of motor efficiency and did some basic calculations. Having got over his initial astonishment, he then asked the manufacturers why higher efficiency motors and drives were not available. Siemens: ‘We’ve got them, but nobody wants them.’ ABB: ‘We have had them for ten years now. It’s just that no one buys them.’ Perhaps this is not really surprising given that 80% of all standard electric motors and drives are sold to original equipment manufacturers (OEMs) who have no real incentive to buy the more expensive high-efficiency motors (HEMs) as they only manufacture but don’t actually use the equipment into which the motors are built. What followed was a visit to see colleagues at the Copper Development Association in Great Britain. CDA UK is the only other copper association to have employed a specialist electrical engineer longer than the DKI and it offers software packages to help in the economic sizing of power cables, busbars and motors. In response to a CDA UK initiative, the motor manufacturer Brook Hansen decided to restructure its product portfolio. Initially the company offered both low-price and energy-efficient models of its motors. Later on, the decision was taken to sell certain motor sizes and types only in the high-efficiency version – a move that was well received in both the national and international markets. In most cases, a high-efficiency motor can simply replace a more conventional low-price variant. While the use of more material certainly makes these motors heavier (Fig. 6), they are not necessarily larger in volume. In most cases only the stator and rotor laminations are a little longer and this can be compensated in part by using a smaller fan, as the thermal losses to be dissipated are lower. The high-efficiency motor is therefore not necessarily longer than a cheaper standard motor. Other dimensions are standardized and remain unchanged.
Fig. 5: Numerous elements have been improved in the new high-efficiency motors (source: Brook Hansen, adapted by the Copper Development Centre South East Asia and DKI)
Fig. 6: Why using more material pays off 3 State regulation? No thanksAround this time, the USA prescribed statutory minimum efficiencies for different types of electric motors. But no similar moves were made in Germany or the EU where we already have enough state regulation as it is. Despite the fact that the American laws (Epact rules) were formulated to apply only to standard motors produced in high volumes and not to special-purpose motors that are often operated only occasionally, one still finds HEMs being installed where their only function is to power an actuator once in a blue moon. But using a HEM for that sort of job is a complete waste of money and materials. Equally, energy is being wasted and money drained away when special-purpose (but low-efficiency) motors, which do not have to comply with the EPact rules, are run continuously. But luckily, representatives from CDA USA were active. The electrical engineering specialist at CDA USA, who had been in the job only a month less than his German colleague, had performed a number of calculations and concluded that at the end of its serviceable life a cheap electric motor, even if it was given away free, ends up more expensive than a HEM (Fig. 4). A false economy if ever there was one and CDA USA’s attempts to publicize this message widely no doubt contributed to the introduction of motor efficiency regulations in the USA. The European Committee of Manufacturers of Electric Machines and Power Electronics (CEMEP) and the German Electrical and Electronic Manufacturers' Association (ZVEI) were both intimately involved in the debate, which began in 1997, on whether state regulation as established in North America should be introduced into Europe. Suddenly, the trade papers and journals were full of articles dealing with energy saving potentials in electric motors and drives. Another event that helped to publicize the issue was the press conference and discussion organized by the DKI on 26 January 1999 in Hamburg to which representatives from motor manufacturers and regional utilities companies and journalists from daily newspapers and especially the business press were invited. Relatively brief announcements noting the existence of energy-efficient drives and motors began to appear in local and regional newspapers and in business publications. One large company subsequently contacted Siemens and announced that it intended with immediate effect to replace all motors by high-efficiency models. ABB reported that they received over one hundred calls and requests all dealing specifically with this issue, and clearly representing only the tip of the iceberg. The unavoidable question of course was: ‘Why the sudden interest?’ The EU decided against issuing a directive specifying minimum efficiency levels. For their part, 31 CEMEP member companies signed a voluntary undertaking agreeing to reduce production levels of non-low-loss two- and four-pole standard motors with ratings of between 1 kW and 100 kW by at least 50% by 2003. But this first required a precise definition of what a high-efficiency motor and what a standard motor actually are. 4 Classification schemeA classification scheme was introduced that categorized motors into three efficiency classes depending on motor type, number of poles, and, most importantly, size (see Fig. 7). The importance of the classification scheme is evident when one considers the significant differences between the motors shown in the figure. Previously, the higher efficiency motors would have been found alongside products of supposedly equal quality, either gracing the pages of the dealer’s catalogue or his shelves – and that undoubtedly is where they would have remained. Motors above the green line fall within the highest efficiency class EFF1, previously known as HEM. Motors lying between the green and the red line are the improved efficiency motors, now classified as EFF2 motors, while those below the red line are in class EFF3 – motors previously referred to as standard motors. According to the voluntary undertaking these labels and logos should be displayed on the motors, and practically all manufacturers are now complying. Even manufacturers from Eastern Europe, who previously had not enjoyed the best of reputations, have been labelling the majority of their products since 2003 – a fact that can be readily verified at the annual Hannover Messe, the major international trade fair and exhibition in Hanover. Labelling tends to be restricted to motors whose energy efficiency is of the class EFF2 standard or better. Products in class EFF3 are not being labelled as such, as motors in this category do not have to comply with any efficiency requirements at all and no manufacturer, unless expressly obliged to do so, is going to draw his customer’s attention to the fact that these products fall into the lowest efficiency category.
Fig. 7: Energy efficiency classification scheme for a range of two-pole motors from different manufacturers
Fig. 8: Details about the classification scheme and the associated efficiency levels are available on the internet 5 Other ways to saveThere are of course other means by which energy can be saved without the use of HEMs and/or variable-frequency drives (VFDs). The simplest method to save energy is the often forgotten option of just switching off drives or motors that are not being used. While this might appear a very trivial proposal, if it is to be implemented in an industrial production process it requires the installation of appropriate logistics systems. Manual deactivation is unlikely to be a realistic option given how often we fail to turn off the lights in a room even though we can see that they are not needed – something that is certainly not the case when we are dealing with drives used in an industrial application.There are also drives that only have to operate at full power for short periods and spend the greatest part of their operational life running at very low loads or even idling. However, switching off these drives may not be worthwhile because the cycle time is too short and the motor’s moment inertia too great. A typical example is the saws that are used in steel mills to cut the steel to the right dimensions as it lengthens during the rolling process. This involves swinging the movable saw blade into position during a pause in the rolling process. From an operational point of view these intervals must be kept as short as possible and particular care is therefore given to establishing the right size, type and configuration of the saw drive. In view of the relatively large size of the motor used, it is worthwhile switching back to a star connection when the motor is running at low load or idling (the motor may well already have a star-delta configuration to assist start-up). Switching should be achieved preferentially using electronic load relays as this helps to lessen wear and reduce EMC problems. Switching to a star configuration is equivalent to reducing the operating voltage by a factor of √3, a substantial saving in this case given that the motor would spend a considerable portion of its operating life in idle mode. This is one of the reasons why the operating point for optimum efficiency (Fig. 9) is much higher than in a transformer. Because motor design can vary individually, and as motors with specific power ratings are not always available off the shelf, and are often dimensioned to include reserve capacity, catalogues now tend to specify not just efficiencies for full load operation, but also for 75 % and sometimes 50 % loads. Another supplementary measure is installing a separately driven fan that only runs when cooling is essential. A wide range of these cooling fans has become available since the introduction of variable-frequency drives that can provide large torques at low motor speeds or even from a standing start and where self-cooling therefore no longer functions. 6 Measuring techniquesQuantifying what has been said so far requires the exact measurement of the losses that occur in a motor, and that is something easier said than done. A transformer takes up electrical energy and releases electrical energy and the measurement of losses is in this case relatively simple. The secondary windings are shorted and the short-circuit voltage is applied to the primary side. The short-circuit voltage is the voltage required to produce the rated (i.e. full load) current in the shorted secondary winding. The copper loss in watts is then measured on the primary side at this voltage. The iron loss is then determined by measuring the power at the rated voltage of the transformer when operating under no load (open circuit) conditions. With a motor, the situation is not as simple. A motor transforms electrical energy into mechanical energy and measuring the mechanical energy means measuring the torque and speed of the motor when running under load. That, roughly speaking, is the approach taken in the direct method of measurement specified in IEC standard 60034-2 (or in modified form in IEC 61972 CDV, method 1) and in IEEE 112B. Even when the measurement is performed with the greatest possible care and high-precision instruments are used, the efficiency can be determined only to ± 0.5 of a percentage point. If a machine has an efficiency of 95%, this imprecision means that the efficiency can fluctuate between 94.5% and 95.5%; expressed relative to the size of the overall losses, this represents an uncertainty of ± 10%. That is unsatisfactory and achieving a higher level of precision is both difficult and costly. Instead of measuring the difference between the (electrical) input and (mechanical) output power, power losses can be measured directly using the so-called calorimetric method. The motor is run in an adiabatic chamber and the ensuing heat losses are then determined. However, the complexity of the calorimetric technique has led to another method, the so-called loss-summation method, being used in practice. This approach is similar to that used in transformers and involves separate determination of the open-circuit and load losses, which are then summed and added to an estimate of the stray loss that depends only on the size of the motor and the frequency. This method is considered to be sufficiently exact by many manufacturers in continental Europe, but is criticized in the USA, where unsurprisingly they favour their own method, and by the British. The USA and UK believe that motors tested using the European / German method end up with significantly better energy efficiency ratings (see Fig. 9). This controversy was the reason why selecting the right measuring technique was the central topic under discussion at the triennial EEMODS conference (Energy Efficiency in Motor-Driven Systems) in London in September 1999. At the EEMODS conference held in Treviso in September 2002, the subject seemed to have run its course. At the Treviso meeting, speakers were invited to a special session on ‘Pumps and Fan Systems’ aimed at improving the efficiency of the overall system. So progress is being made. A view supported by the fact that after the EEMODS 2005 in Heidelberg, the conference will be held every two rather than every three years. The latest one took place in Beijing in June 2007. One topic not on the agenda is the influence of poor power quality (undervoltage, overvoltage, voltage asymmetry, harmonics) on motor performance. The effects of power quality on performance characteristics such as starting torque and especially motor efficiency are far greater than initially thought. Poor power quality can more than wipe out the beneficial effects of deploying a HEM; on the other hand, the difference between motors in the three energy efficiency classes become even more apparent as the quality of the power supply voltage deteriorates.
Fig. 9: Differences in the results of motor efficiency measurements using a range of measurement methods
Fig. 10: The energy used in obtaining the copper is rapidly recouped – even faster than the time taken to recover the financial outlay 7 Environmental paybackAny proposal to save energy by using more material is always accompanied by the objection that energy is used in making the extra material required. Obviously, this energy has to be included in the energy balance and in the case of copper, the required figures are as follows: Manufacturing copper from ore requires about 50 GJ/t of primary energy, manufacturing copper from scrap requires 30 GJ/t. Approximately 45% of the copper produced in Germany is from reprocessed scrap. (As most copper products enjoy a long service life that averages about 30 years and as the copper market thirty years ago was only half as big as it is today, the real rate of recovery and reuse of the copper used at that time is an impressive 90%. For our purposes here, however, we shall express recovery rates relative to today’s production levels.) For the sake of simplicity, we assume a recovery and reuse rate of 50% and a mean average energy consumption of 40 GJ per tonne. The resulting energy loss relationships are shown in Fig. 10. The table can be read as follows: A current density of, for instance, 3 A/mm² generates power losses of 17.64 W in 1 kg of copper windings, as these ohmic losses are dependent only on the size of the current density.1 If the current density is lowered from some arbitrary higher value to this value of 3 A/mm², it will take 206 hours operating at full load to save the energy necessary to produce the additional copper needed in the manufacture of the HEM. This time can be thought of as an ‘environmental payback period’ and is clearly very short, significantly shorter than the already short financial payback period. However, the environmental payback period is strongly dependent on the target loss level. More ambitious loss reduction targets are typically far harder to achieve. The first step to achieving improved efficiency is the easiest. The environmental payback period (in this case: 206 hours) does not depend on how far the starting current density is from the target current density (in our example: 3 A/mm²). If the desired improvement is small, then the requisite amount of material (in this case, copper) is also small. The calculation aimed to compute primary energy savings and assumed an overall efficiency for the generation and distribution of electric power of 33% (i.e. every kilowatt-hour of electricity saved in the motor saves 3 kWh of primary energy), which approximately reflects the situation in Germany. 8 Turning to efficiency: copper rotorsAn energy-optimized three-phase motor in the efficiency class EFF1 does not actually contain much that is new. The rating is achieved because of relatively minor improvements to design details, principally the use of more conducting material and improved magnetic material. There is one improvement that does indeed represent a transition to a new type of technology, but it has still to be fully exploited in today’s HEMs and EFF1 motors. Nevertheless the potential for improvement is so great that it would, when combined with the other efficiency-optimization factors, justify the introduction of a wholly new energy-efficiency class, which could be dubbed the ‘EFF0’ class (cf. Fig. 11 and Fig. 12). The improvement we are talking about can be achieved by changing the material used to manufacture the squirrel-cage rotor.
Fig. 11: Comparison of the efficiency of an aluminium and a copper rotor in an otherwise identical motor
Fig. 12: Comparison of the efficiency of a simple EFF3 motor with that of an efficiency-optimized motor containing a copper rotor The rotors used in today’s industrial motors contain at most two conducting materials. Of these, aluminium was until recently the material of choice for cast rotor cages because it melts at 660 °C whereas copper, which was for a long time considered only a theoretical alternative, melts at 1083 °C. However, as the conductivity of copper is 35 % better than that of aluminium, considerable effort was made over a number of years to develop a casting die that would have an economically viable lifetime when used at the much higher temperatures needed to cast copper.2 This has now been achieved.The first motors with these novel rotors were exhibited at Hannover Messe in 2003. The copper rotors, which were and continue to be developed and produced in France, were exhibited both on their own and integrated into motors. Since 2006, Siemens has been offering its own die-cast copper rotors using its in-house technology in the USA. Obviously, the better conductivity of the copper helps to reduce power losses, but that is not the only benefit that this new technology offers. During the development process, there were several obstacles to overcome and a number of open questions needed to be resolved.
Fig. 13: Copper rotors – now available in nearly every shape and size
Fig. 14: The design was revised and simplified compared to that used for aluminium rotors 8.1 Preliminary work 1: the hot iron effectOne of the issues was the effect that the high casting temperatures would have on the rotor laminations. Simple visual inspection suggested that this would have an effect – and more likely a detrimental rather than a beneficial one (see Fig. 15). After all, the Curie point of iron is at 770 °C (the temperature at which the material loses its ferromagnetic properties) and if the magnetic sheet steel is heated above that temperature there might well be permanent consequences. There certainly is an effect, but surprisingly it turns out to be one that is advantageous and not detrimental to the motor. A range of experiments were performed to measure a number of different parameters of untreated iron and of iron that had been annealed at various temperatures . What was found was that the iron losses get smaller rather than bigger (Fig. 17) and the magentizability increases rather than decreases provided the annealing temperature is not too high (Fig. 18). Subsequent investigations showed that the high temperature does not penetrate the iron to any great depth (see Fig. 16). As the thermal conductivity of iron is less than one tenth that of copper, the copper is able to conduct the heat to the outside faster than the heat can penetrate the iron.
Fig. 15: View of a rotor lamination before assembly (left) and after die-casting with copper (right). (source: Favi)
Fig. 16: Temperature distribution during die-casting (source: Favi)
Fig. 17: Influence of the higher casting temperature for copper on the rotor lamination: the iron losses get smaller …
Fig. 18: … and magnetizability improves! 8.2 Preliminary work 2: start-up behaviourBut how do these new die-cast copper rotors behave at start-up? It is well-known that the starting torque in a three-phase induction motor is significantly smaller than the maximum torque, which is achieved just below the motor’s nominal speed. This difference is greater, the larger the motor and the lower its ohmic losses. Relatively speaking, the ohmic losses in a larger motor will always be smaller. If the rotor suffered no ohmic losses whatsoever, the angle between the rotating magnetic fields of the stator and rotor would be exactly 90° and the force between these two magnetic fields would act purely radially, i.e. its tangential component would be zero, and this purely ‘reactive’ or ‘wattless’ force would contribute nothing to the motor’s torque. A certain ohmic component is therefore necessary even though it does result in power loss. As the motor ramps up to speed, the frequency of the rotor current gets smaller and smaller and the inductive component of the rotor’s impedance decreases accordingly. The relative significance of the ohmic component, whose absolute magnitude remains constant, increases as a result, and as the phase angle decreases so too does the angle between the stator and rotor fields. The torque increases despite the decreasing current in the stator and rotor windings. At the rated operating point, e.g. 2940 rpm, which is only 60 rpm (i.e. 1 rps) below the synchronous speed, the frequency of the rotor current has decreased to a mere 1 Hz. At this frequency, the reactance, i.e. the inductive component of the impedance, is negligible (whole just before, at 50 Hz, things were inverse). Although the force is now lower (as a result of the lower current) it now acts almost entirely tangentially with practically the entire magnetic force now being converted into mechanical torque. A certain amount of resistance in the cage winding is therefore required. However, using copper in place of aluminium in the rotor cage lowers this resistance and lowers the starting torque accordingly. A measurement performed on a 5.5 kW motor showed that the torque reduction was minimal, falling from 90 Nm to 85 Nm. Calculations indicated that the difference should have been greater, but the actual measured value is what counts. If this small drop in the starting torque is unacceptable, the shape of the rotor slots will need to be modified so that skin effects during ramp-up limit the effective cross-sectional area of the conductor bars and the resistance rises accordingly. Once the motor is running at close to full speed, the frequency will be so low that the skin effect is no longer relevant and the entire conductor cross-section can be used to carry current. If the resistance in the squirrel-cage rotor is smaller, the current will be correspondingly greater. An operating induction motor can be viewed as a transformer, and if the rotor current increases so too will the current in the stator. It was therefore also necessary to test the extent to which the starting current increased. Fortunately, in the motor under test, the starting current rose from 6.5 times the rated current for a motor with an aluminium rotor to only 7.5 times the rated current when a die-cast copper rotor was used. The result is in fact what one would expect, as the starting current is for the most part limited by the greater inductive component of the impedance and this inductive component is independent of the conductive material used. 8.3 Advantage 1: more torque, more powerHaving cleared up all the reservations associated with die-cast copper motors, we can now turn to the benefits of this technology. Erring on the side of caution, we assumed for all the calculations and discussions in this work that we were dealing with Cu97, i.e. copper with a conductivity that is 97% of the IACS value. According to the IACS, a 100 % conductivity rating for pure copper is equivalent to a conductivity of 58 MS/m. However, there are engineering coppers of greater purity whose conductivity is 58.5 MS/m or greater and the corresponding ICAS conductivity rating is therefore above 100 %. As the process of die-casting a rotor may lead to the incorporation of traces of iron and other impurities into the copper, we assume that the manufactured die-cast copper rotor has a conductivity of only 97% IACS. The casting method, which involves pre-filling the slots of the iron rotor core with a special powder that vaporizes or decomposes during casting, guarantees that the final conductivity is not lower than this minimum assumed value of 97% IACS. Whereas the torque is smaller when the rotor is stationary due to the greater conductivity of copper, it is far larger when the motor has reached its nominal speed. One can now effectively choose whether to benefit from higher torque or from higher rotational speed (see Fig. 19). In the former case, the greater mechanical power delivered by the motor requires a corresponding increase in the electric power input. The advantage of using a copper rotor is in this case not a reduction in power losses, but increased power density, that is, the same power from a smaller motor or more power from the same sized motor. Normally, however, the benefit of using a copper rotor cage will be exploited by running the motor at a higher speed than could be achieved with an aluminium cage at the same current and power input levels (Fig. 20). Theoretically, the design of the motor will effectively determine whether or not more weight is given to achieving additional torque or a higher motor speed.
Fig. 19: Increased torque or higher motor speed (source: Favi)
Fig. 20: Operating points for the same output power (5.5 kW) for Cu and Al rotors 8.4 Advantage 2: simplified rotor designAlthough copper with a 100% IACS conductivity rating is a better conductor than aluminium by a factor of ‘only’ about 50 %, the conductivity factor measured in squirrel-cage rotors cast using Cu97 was even higher than that in the equivalent aluminium rotors. This is because die-cast aluminium tends to contain cavities and defects that are absent in the cast copper product. Also, the aluminium used for casting is usually an alloy containing ‘only’ 99.5% aluminium. This alloy is used as it offers improved mechanical strength, but its conductivity is lower because the other alloying elements are effectively impurities. An additional disadvantage of using aluminium is that the defects in the die-cast material mentioned above can lead to the rotor becoming unbalanced. When a copper rotor is used, not only can one dispense with cooling fins as there is less heat to be dissipated, but the rotor does not need to be balanced if the motor is not going to be driven at frequencies much above the supply frequency. The much simpler design of a copper rotor compared to an aluminium rotor is apparent in Fig. 14. This helps to compensate to some degree for the additional costs of using what is a substantially more expensive conducting material. As end-of-life products are increasingly being recycled and fed back into the production cycle, the higher scrap value must also be subtracted from the additional cost of procurement. Electromagnetic equipment is primarily composed of easy-to-separate combinations of iron and copper. Once it has reached the end of its – often long – service life, such equipment is not treated as waste but as a highly sought-after source of secondary raw materials. With a density of 8.9 kg/l copper belongs to the class of heavy metals, whereas aluminium has a density of only 2.7 kg/l and is classified accordingly as a light metal. Because it is the cross-sectional area of the conductor, and hence its volume, that is relevant, the greater density of copper means that a copper rotor cage will have a much greater mass, and as the kilogram price of copper is significantly larger than that of aluminium, material costs will be substantially higher. A copper rotor is thus significantly heavier than an aluminium rotor and, more significantly, its moment of inertia is greater too, as the extra mass is located around the periphery of the rotor. This may need to be taken into account when adjusting the control response of the VFD and in extreme cases it may well mean that the copper rotor cannot be used. Applications involving machine tools, for instance, demand that the rotor is stopped or reversed extremely frequently, possibly even every second. In this type of application, it is simply not possible to decelerate and re-accelerate the copper rotor fast enough. And even if it is possible, it wastes the energy saved by using the copper rotor. But these are rare cases. As a rule, the greater mass of the copper rotor is beneficial, as the motor can be overloaded for longer. Despite the fact that aluminium has a significantly larger heat capacity (900 kJ/(kg*K)) than copper (380 kJ/(kg*K)), when expressed relative to material volume, the order of the heat capacities reverses: 2.43 kJ/(l*K) for aluminium compared to 3.39 kJ/(l*K) for copper. Using copper for the squirrel-cage rotor therefore provides an overload capacity some 40% greater. In this context, ‘overload’ includes the start-up phase in which, as already mentioned, the starting current rises to 7.5 times the rated current. The (ohmic) power loss during ramp-up is thus more than 50 times greater than that at the motor’s rated operating point. This can cause problems in some applications, as a motor with an aluminium rotor that was switched off (possibly because of an unscheduled shutdown) and is still warm can only be switched on again after being allowed to cool for a specified period – and this can prove very costly in today’s tightly scheduled production environments. In contrast, the copper rotor is better able to store the excess heat loss without suffering or causing damage and to gradually dissipate this thermal energy once the motor is back up and running. 8.5 Advantage 3: extreme conditions and special motorsAs already mentioned, HEMs and EFF1 motors can also be manufactured using aluminium rotor cages and this has in fact been the norm so far. Copper rotor cages come into their own when a high-efficiency motor with an aluminium rotor is inadequate for the proposed task. This can arise when:
The introduction of the die-cast copper rotor has, for instance, made possible the manufacture of certain watertight encapsulated motors. If the motor were to be totally immersed in water and only operated in this state, one would have optimal cooling conditions, though it pays to remember that optimal cooling conditions is also the most efficient means of wasting energy. However, although the motors in question were fully encapsulated, they were not necessarily nor exclusively to be used under water, meaning that heat dissipation through the encapsulation was seriously impeded. Initial trials involved aluminium rotors, but the stator windings were 5 K and the rotor 15 K hotter than when a copper rotor was used. This had obvious consequences for the lifetime of these components, which, according to a rule of thumb, is halved for every increase in temperature of 10 K. This effect can prove to be decisive when planning the deployment of this sort of expensive and potentially hard-to-replace motor. Copper rotors also proved more than welcome to an engineer at HDW Howaldtswerke Deutsche Werft AG whose specialist field is the electrical systems and installations in submarines. The engineer was even contemplating using silver, even though its conductivity is only 6 % better than that of copper. Silver, however, was too soft to withstand the centrifugal forces generated. If you were awarding medals for conductivity, copper would get silver and silver gold. Gold “only” gets bronze and aluminium just fails to make the podium. 9 But a variable-frequency drive saves more energy than a better motor…This argument crops up time and again in discussions about EFF1 motors and copper rotors – and perfectly justifiably so. It has been estimated that using only EFF1 motors in the EU would save 1.3% of total electricity consumption. In absolute terms this is equivalent to 150 TWh/a − a massive quantity of energy. An additional savings potential of 8% can be achieved from the systematic deployment of variable-speed drives wherever possible. However, the requisite VFDs are a lot more expensive than the premium paid when purchasing a HEM. As a result, the rates of payback for both these measures are of the same order of magnitude. Both are short, and in extreme cases investment can be recouped within a year. Other sources quote energy saving potentials of 3% for the use of HEMs and 10% for variable-frequency drives, a figure that can be increased to 20% if the entire process is optimized, but this is correspondingly more expensive. Unfortunately, the source does not specify what the percentage figures refer to. It is likely that they refer not to total electricity consumption, but only to that part used to operate motors. In that case, there is approximate agreement between the two sets of figures. Ultimately, the numbers quoted are only estimates. As controlling the speed of a rotating-field machine only became possible with the introduction of power electronics, there are still numerous drives in use that are literally brake-controlled. Fans and pumps make up the greatest fraction of all motors. Despite the fact that the torque generated in these drives grows with the square of the spindle speed and power output is therefore proportional to the speed cubed, it is very often fans and pumps that are simply left to run at their fixed rated speed with throttling achieved via cocks and valves. In this situation, the best solution is a combination of a variable-frequency drive (VFD) and a high-efficiency motor. While a VFD adjusts the motor speed to match the load, it does not create a clean sinusoidal output voltage. This increases the power losses in the motor particularly the stray losses. The difference, though small if modern VFDs are used, increases the relative savings that can be achieved by using a HEM rather than a standard motor. And incidentally, VFDs and EFF1 motors are two further examples of the observation that copper or additional copper is always in use whenever it comes to saving electrical energy. According to estimates by the DKI and the ERA, the amount of copper contained in a VFD (smoothing reactor, interference suppression coil, fuses, connectors) contains about the same amount of additional copper required when an EFF1 motor is deployed in place of an EFF3 rated motor.
Fig. 21: The financial savings to be made from the use of a variable-frequency drive is strongly dependent on the size of the motor
Fig. 22: Efficiency of a three-phase induction motor as a function of load 10 SummaryAs shows, the efficiency of three-phase induction motors can be improved through optimization of materials and operational parameters. If these improvements are realized, practically any motor that is operated more than just occasionally will, over the lifetime of the motor, yield savings equivalent to the purchase of several new motors (see Fig. 4 and Fig. 24). More detailed analyses are available from DKI and from the major motor manufacturers who also offer programs for selecting the best motors and drives for specific applications. Classifying motors into energy efficiency bands simplifies product selection and dispenses with the need for statutory control. The new labelling scheme is a major step forward as up until recently motor rating plates did not contain any information on power losses and efficiency. It would have been more expedient, however, to assign the label ‘EFF1’ to the lowest rather than the highest efficiency category, as this would have meant the ‘EFF’ series could be readily extended upward as future efficiency improvements are introduced. Recent developments in the USA have seen the production of motors whose losses are now lower than those stipulated in statutory regulations. As a result, these new high-efficiency motors have received the rather ungainly moniker ‘NEMA Premium™’ and only time will tell what awkward lexical construction will be created to describe the next phase of motor efficiency improvements. And with motors becoming ever more efficient, there is clearly going to be little need to extend the existing classification system in the other direction beyond EFF3.
Fig. 23: Improvements across the board, if all the elements highlighted in Fig. 5 are optimized
Fig. 24: It’s the running costs and not the purchase price that counts While there may be a few disreputable suppliers from the Far East (in contrast to the encouraging developments now seen in Eastern Europe) who will attempt to sell products with fake labels, that cannot be used as an argument against the labelling scheme itself. Replacing a standard motor by a HEM does not always lead to lower power consumption. Some users have registered an increase rather than a decrease in energy consumption due primarily to the smaller slip that accompanies the use of copper rotors. In view of the quadratic torque characteristics observed for many loads, this is certainly plausible. Increasing the motor speed by for example 1% (of the nominal value) is equivalent to an increase in output power of almost 3% (of the nominal value) that more than compensates the reduction in losses from say 5% to 4% (of rated power). Whether or not this additional input power, which is delivered to the motor’s shaft as additional mechanical output power, is regarded as a loss depends on the specific application. If treated as a loss and if a power output of 103% of the rated value is seen as ‘too high’, it is highly improbable that 100% is ‘just right’. In all likelihood the motor’s output power can be reduced further, at least occasionally. In this case, the motor is wrongly dimensioned or a VFD should be used. If not treated as a loss, then we are dealing with some kind of process improvement which has nevertheless been achieved by reducing losses in the motor. Discussions are still needed concerning the ‘correct’ method of measuring motor efficiency. By far the largest energy savings are anyway achieved using variable-speed controllers, but using them also makes deployment of the HEM even more important. The best approach is to optimize the entire drive train and that, as is so often the case, is most simply and cheaply done during the planning phase, retroactive corrections tend to be expensive and hard to realize. All this was appreciated during the EEMODS conference in 1999. If the benefits of energy-efficient motors are to be fully exploited what is needed is a willingness to see the big picture and to venture outside one’s own backyard. Even though motors and electric power are purchased by different cost centres within a company, it is still the one and the same company that actually pays the bills. However, the additional cost of purchasing a high-efficiency motor is printed on an invoice for all to see, the far greater savings made by deploying that motor are sadly not documented so directly. Overcoming these inequalities in company-internal market mechanisms is a mammoth task, but history is on our side: didn’t our ancestors successfully deal with mammoth problems during the ice age? |
|
The content & opinions in this article are the author’s and do not necessarily represent the views of AltEnergyMag
Comments (0)
This post does not have any comments. Be the first to leave a comment below.
Featured Product
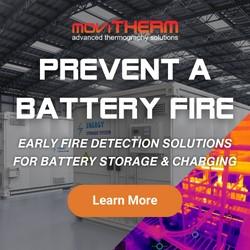