Digital Manufacturing’s Role in the Future of U.S. Electric Vehicles
As has been widely discussed, electric vehicles and EV battery manufacturing will play an important role in U.S. manufacturing in 2025 and beyond. While there are shifting opinions on what the exact future may hold, it’s difficult to envision a scenario in which EVs do not feature prominently in this nation’s long journey toward more sustainable, lower-emission transportation.
Producing more EVs, EV batteries, and other technologies relevant to EV infrastructure and energy storage will remain a prominent agenda item as the United States continues to explore its options. While the exact path forward is unknown, there are a few key considerations for manufacturers when planning, building, or renovating plants, all of which will be critical if the U.S. is to compete on the global stage.
Remaining nimble and agile amid shifting production needs
U.S. manufacturing doesn’t have a crystal ball that can predict the needs of tomorrow — or the longer-term future. That said, reports suggest that U.S. industrial manufacturers have a sustained commitment to electrification and decarbonization of products. Digital technologies and platforms are critical to EV battery manufacturing because proactivity and predictability remain the gold standard of operational excellence. It’s the only way to remain nimble in the face of change.
Manufacturing execution systems (MES) and digital manufacturing platform (DMP) solutions are important tools. These systems bring a 30,000-foot view to the entire production line or process. MES and DMP solutions integrate into operations and connect previously disparate systems, extracting critical data from different points along the supply chain and bringing them into one centralized hub. The result is nimbler and more agile operations that can shift with speed thanks to greater machine-level monitoring, control, and programming. MES and DMP solutions can better position manufacturers to overcome factors that analysts say could impact the delivery of “clean” products, for example the availability of raw materials, clean energy sources or government incentives and rebates.
Recruiting and retaining talent, supported by digital technologies
A recent survey found that more than 70 percent of manufacturers rate both retaining existing talent and finding the right new talent as among the top five challenges for managing their workforce. Given the lack of sufficient labor to meet expected future needs, manufacturers are deploying digital manufacturing solutions to help workers be more productive and efficient. In addition to helping workers get more done, integrating the latest digital manufacturing technologies can help manufacturers attract digital natives who are adept at using the technologies.
The takeaway: EV battery manufacturers — both evolving and net-new — will need to lean heavily on digital manufacturing systems to run effective businesses. But, as we’ve heard at recent tradeshows and events, those digital systems must be easy to deploy, use, and maintain. EV battery manufacturing is incredibly complex, requiring very precise processes, from electrode coating to cell formation. Digital systems must be able to manage these intricacies. Working with a trusted partner with manufacturing experience is an effective way to digitize to support operations today, while building a workplace to attract digitally native talent.
Resiliency through a data-driven approach to manufacturing
The global battery market is growing steadily and expected to reach $423.9 billion by 2030. At the same time, material and input costs are expected to rise. So, how can production goals be met while navigating macroeconomic challenges and price volatility?
For EV battery manufacturing, atop the list of answers is to do more with data — and using data to better predict the supply chain. This is important for manufacturers looking to optimize every input and extract the most for every output. Manufacturers also need to evaluate the latest technology, such as AI, automation, and sensor-based IoT to find cost effective ways to speed up or scale business. In its 2025 manufacturing outlook, Deloitte noted that the industry must prioritize targeted investments in its digital and data foundation. This is not only to accelerate innovation but also to overcome skills gaps and supply chain challenges.
Digital manufacturing will play a significant part in this nation’s future
I’ve been on the road for much of 2024, and I’ve heard repeatedly from EV battery manufacturers that they are looking to do more with less, run more consistent and efficient operations, and meet production needs today while keeping a wary eye on the shifting landscape of tomorrow.
It’s a tricky proposition — and a journey that EV battery manufacturers won’t chart alone. Together, we must architect a future in which people, processes, and plants work in sustainable harmony. It won’t happen overnight, but the conversations we’re having today about our digital manufacturing future will go a long way in making this vision a reality.
Eric Symon is Head of Smart Manufacturing at Panasonic Connect North America. Eric has held executive positions at market-leading software and professional services companies delivering value through digital transformation to customers in manufacturing, aerospace and defense, and retail industries. Eric holds a B.S. from the Pennsylvania State University.
Comments (0)
This post does not have any comments. Be the first to leave a comment below.
Featured Product
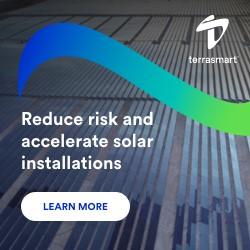