Automated cleaning process for printed photovoltaic modules manufactured using roll-to-roll technology
The compact cleaning module can be adapted to the respective web width and easily integrated into roll-to-roll production lines.
Photo credit: Research project team PV-CO2
Roll-to-roll production lines enable printed photovoltaic modules to be produced particularly cost-effectively. To avoid short circuits, however, conductive burrs created when the front electrode is laser structured previously had to be removed manually in a way that was not compatible with the industrial process. In a joint project, a fully automated CO2 snow-jet cleaning solution was developed that can be integrated into the production line to eliminate this problem.
With a layer thickness of between 0.5 and one micrometer and high efficiency even when solar radiation levels are low, flexible, printed photovoltaic cells open up a wide range of applications when it comes to supplying solar energy. In the field of printed photovoltaics, the roll-to-roll process offers major advantages in terms of production speed, volume and costs. The five layers of the modules, which are based on organic and perovskite semiconductors, can be processed individually. The bottom layer - a transparent IMI electrode (structure: indium tin oxide, silver, indium tin oxide) - is structured by laser. Burrs are formed along the structured edges, which are conductive and protrude a few micrometers from the surface. If they are not removed, they will cause damage and short circuits due to the thinness of the modules. The current practice is to remove the burrs mechanically at very low web speeds. However, there is a risk of the structured layers becoming damaged due to the mechanical impact.
Development of an automated, in-line cleaning solution
To solve this problem when manufacturing printed photovoltaic modules on roll-to-roll production lines, the Institute Materials for Electronics and Energy Technology (I-MEET) together with the Solar Factory of the Future at Friedrich-Alexander-Universität Erlangen-Nürnberg, Sciprios GmbH and acp systems AG, initiated the “PV-CO2” research project funded by the Federal Ministry for Economic Affairs and Climate Action (BMWK). The aim was to develop a fully automated CO2 snow jet cleaning system for industrial use based on acp's quattroClean snow jet technology. This is a dry process which is used for full-surface and selective cleaning applications. The cleaning medium is liquid carbon dioxide recycled from chemical production processes and energy generation from biomass. The carbon dioxide is guided through a wear-free two-substance ring nozzle and expands on exiting to form fine snow crystals. These are bundled by a separate jacket jet of compressed air and accelerated to supersonic speed. When the easily-focused jet of snow and compressed air impacts on the surface to be cleaned, a combination of thermal, mechanical, solvent and sublimation effects occur, which is the basis of the cleaning action. The crystalline carbon dioxide sublimates completely during the process, leaving the treated surfaces completely dry.
The effects of deburring were demonstrated by measuring the IV curve of modules produced on substrates that were untreated (d), manually cleaned (e) and cleaned using the CO2 snow jet technology (f). b and c show the light and dark curves of the three differently-treated modules. In the DLIT images of the modules (d, e, f), the bright areas indicate hot, localized spots, which are particularly visible in the interconnection zones of the uncleaned modules.
Photo credit: Research project team PV-CO2
Proven efficient burr removal and enhanced efficiency
A roll-to-roll pilot line was set up for cleaning the laser-structured electrode substrates and fitted with several quattroClean snow jet nozzles arranged above the electrode web. The first step was to optimize the jet parameters so as to significantly reduce the burr height without damaging the electrode. In addition to the capillary diameter, which determines the flow rate of the liquid carbon dioxide, and the pressure of the compressed air jacket, the distance between the nozzle and the substrate needed to be adjusted, as well as the web speed and the inclination of the nozzles in relation to the substrate. After each cleaning process, the maximum burr height was measured by confocal microscopy. This procedure was repeated for a large number of parameter combinations until an optimum cleaning result was achieved.
To evaluate how deburring affects photovoltaic efficiency, organic photovoltaic modules eight centimeters wide were produced on substrates that had been cleaned using the CO2 snow-jet process. These were compared with modules produced on untreated substrates and manually-cleaned substrates of the same size. As expected, the modules on the uncleaned substrate had a high leakage current, which reduced Photovoltaic Cell Efficiency (PCE ) to 2.3 %. For the manually cleaned modules, the PCE was 4.8 %, and for the modules cleaned using the CO2 snow-jet process, it was as high as 5.3 %. The difference in efficiency is explained by the fact that manual cleaning causes scratches to be formed on the electrode, which can significantly reduce the active area. This is because the scratched area does not generate any current and also because areas can be cut off from the charge extraction by the scratch.
Dark Lock-In Thermography (DLIT) was used to confirm that deburring is responsible for the difference in efficiency of the differently-treated substrates.
Ready for series production for various applications
The fully automated cleaning solution has now been integrated into the standard production process for printed photovoltaics at the Institute Materials for Electronics and Energy Technology. Here, an array with seven nozzles is used to reliably remove the laser-induced burrs on a 25 cm-wide web. At Sciprios, too, the CO2 cleaning process is now one of the equipment options for roll-to-roll production lines for printed photovoltaic modules.
The cleaning solution, which is easily integrated into roll-to-roll production lines, makes the manufacture of any type of printed electronics involving laser structuring more economical, more productive and more sustainable. Another application is electrode production in battery manufacturing.
Comments (0)
This post does not have any comments. Be the first to leave a comment below.
Featured Product
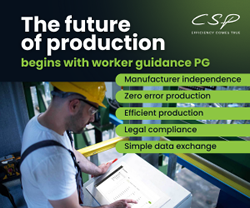