Implementing AI for Energy Efficiency in Manufacturing
Manufacturing facilities have a golden opportunity to reduce costs, improve productivity and embrace digital transformation to achieve their energy-efficient goals with one asset — artificial intelligence (AI). Every team can use this tool, but where does implementation begin?
Apply these accessible best practices to make AI part of any sustainability enhancements. Manufacturing corporations should also know the specific technologies and hurdles they might encounter so they can prepare accordingly.
Assessing Energy Consumption
Cutting usage helps facilities develop long-term energy efficiency. AI streamlines the lengthy, tedious process of data mining for power metrics across hundreds of thousands of square feet. Necessary technologies include smart meters, data analytics tools, and the Internet of Things to track real-time activity and create performance visualizations.
The AI energy audit quantifies previously nebulous consumption patterns. The insights could mitigate up to 10% of greenhouse gas emissions by 2030. Stakeholders may even compare their numbers against competitive benchmarks or regulatory expectations by asking generative AI. Data overload is a potential hurdle, but curated training and regular data cleaning will maintain integrity and accuracy.
The model’s machine learning algorithms become more proficient at determining energetic anomalies over time, the sources pulling the most power, and numeric references the manufacturers use to frame their goals.
Implementing Predictive Maintenance
Once the AI knows the facility’s energy consumption, it can suggest areas of opportunity. It may notice the HVAC system is overdue for a filter change and uses more energy than it should for its model and age. AI dashboards could also reveal that lights remain on overnight, even without occupants. After AI discovers unwanted technical behavior, it may inspire technicians to review faults in the motion-detection system.
Condition monitoring systems are also powerful tools for preserving production quality and preventing downtime. Corporate machine-learning platforms detect faults, predict equipment failures and send reminders when preventive maintenance is due. These applications may not be compatible with all machinery, primarily legacy systems. However, agencies may undergo gradual retrofits and install middleware to facilitate AI predictive maintenance assistance until a complete rollout can occur.
Optimizing Production Processes
AI made maintenance for energy-intensive equipment attentive. Now, it can help improve production workflow habits and employee behaviors to make a more widespread impact. Stakeholders should consider lean manufacturing principles with AI suggestions to find energy efficiency optimization opportunities. They might lie within these production areas:
- Scheduling machines to run during off-peak times
- Finding renewable energy generators
- Harnessing electrification
- Adopting Industry 4.0 strategies like automated energy systems
- Replacing antiquated equipment
- Addressing poor energy hygiene from lack of employee training
Staff may resist change, but management can ease this by offering incentives at training workshops to encourage buy-in. Increasing familiarity with AI tools and learning how important energy efficiency is may be the only difference between stubborn staff and people willing to upskill. Simulation software with AI integrations is useful for modeling process changes before implementing them to test if they will have the projected energy impact.
AI’s beauty is in its versatility and compatibility with other technologies and realms of the business. For example, if companies want employees to train on the job, AI enhances spatial computing experiences, known as expanded realities (XRs). The data crafts a realistic, virtual setting for operators to test their skills in low-stakes situations with real-time, hands-on interactivity that online training modules lack.
Continuous Monitoring and Feedback Loops
Energy oversight with an AI is a constant process. It should never stop because it could discover anomalies or signify employees are deviating from sustainability training. Establishing a perpetual observation system means complacency never develops, leading to dips in energy efficiency.
However, data silos and third parties make this a challenge because manufacturing resources are usually dispersed. Solve this problem by making AI a cross-departmental requirement and partner expectation.
For example, the AI and data centers sectors both increase their carbon footprints yearly. However, the industrial and manufacturing industries rely on them to compute vast amounts of information quickly. Leveraging AI in data centers connected to manufacturers could reduce their energy consumption by 96% because of optimizations inspired by round-the-clock monitoring. Continuous surveillance happens within and outside of the facility for comprehensive energy efficiency gains.
High-Energy Implementation, Low-Energy Results
Incorporating AI for energy efficiency gains requires dedication, but the effort yields an optimized, self-sufficient machine. Early AI adopters using it to progress corporate social responsibility and lower building emissions garner favor among client bases for their initiative. Additionally, they establish thought leadership during this next generation of industrial overhauls powered by the environmental revolution. The only way to obtain results as swiftly and accurately as the current market demands is with AI.
Comments (0)
This post does not have any comments. Be the first to leave a comment below.
Featured Product
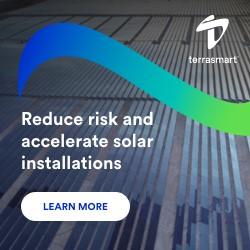