Improving Energy Efficiency of EV Manufacturing
The electric vehicle (EV) industry will pave the way for commercial and individualized sustainable transportation. The omission of oil as a fuel source would appear to be the solution, but the vehicle’s environmental impact after purchase doesn’t account for the resources utilized to create it in the first place.
What Goes Into Making an EV?
There are misleading oversimplifications concerning EVs all over the internet. Some state the production voids its entire environmental impact. Manufacturing EV parts uses fossil fuels like coal and oil to make, so does this outweigh the fact it won’t use oil at all in its lifetime?
When analyzing the environmental impact of EV batteries, the Department of Energy concluded through “cradle-to-grave” life cycle assessments (LCAs) that its efficiency mitigated the resources used to create it.
These LCAs provide a holistic view of the trade-offs in the resource extraction process to end-of-life care for the battery. Analyzing these steps is a more accurate measurement of greenhouse gas emissions for the life span of the materials instead of a narrow perspective from one stage.
Many of the traditional parts used in ICEs are not necessary for EVs, including:
- Pistons
- Clutches
- Oil pumps
- Exhausts
- Alternators
This provides an even more significant advantage for EVs since they produce fewer emissions by not using as many parts.
How Are Resources Used in EVs?
The lithium-ion batteries are the focal point of most sustainability conversations. What goes into making them, and are they durable enough? Are there widespread recycling programs for them and are they safe? There are two processes used in lithium-ion battery recycling, and both are time-consuming and require infrastructure.
The first is pyrometallurgy, which uses smelting to reduce the battery to more organic materials for retrieval. There is also hydrometallurgy, which uses leaching and soaks the battery in acids to reclaim materials like lithium. Due to the hazards and resources needed to do this, manufacturers do not perform it frequently. These processes cannot improve without sufficient assessment. EV owners will need to recycle more batteries for manufacturers to make informed process improvements.
It’s vital to see where the energy of a charge is used to understand the environmental impact of an EV. Gas-powered cars lose 64%-75% of their power, whereas EVs only lose 15%-20%. EVs can reuse or save energy, whereas an internal combustion engine (ICE) vehicle can’t. This includes power shifts when idling or regenerative braking.
This means EVs’ optimized energy use outweighs the fact that fossil fuels go into making the car since most of its stores keep it on the road longer. EV technology advancements could lead it to 100% efficiency, propelling it further as a sustainable staple.
How Can EV Manufacturing Get Better?
The key to optimization in manufacturing is streamlining. The process chain should prioritize reducing bottlenecks in manufacturing, especially for batteries. Production electrodes, assembling cells and finishing all go into a battery, leaving countless opportunities for downtime. Designing more fluid machines could improve energy efficiency, reducing resource consumption.
However, this is still being researched as adjustments to parts of the process could negatively influence later steps, making one portion energy-efficient and the next less. The number of moving parts means continued maintenance alongside simple action can improve the value and efficiency of any manufacturing process.
However, none of this matters if the plants extracting materials and assembling cars are not using renewable energy. Old gigafactories producing most lithium-ion batteries still use fossil fuels, as was the trend in the early stages of EV manufacturing.
These factories could shift to renewables, causing the resource expenditure of batteries to fall drastically — especially since they are one of the top arguments for the questionable sustainability of electromobility. With industry shifts, the industry is looking to reduce the 200 grams of carbon per mile down to 50 grams by 2050.
Manufacturing could also look into charging stations. There are improvements to make here, as EVs in standby mode are still wasting resources. Charging stations that meet Energy Star standards would use 40% less energy with increased efficiency.
The transparency of EV manufacturing is a step in the right direction, creating more productive discourse around progress. This leads to legislation informing lawmakers about the details so they can take appropriate action to instill widespread regulations.
Even More Eco-Friendly EVs
The complexity of EV manufacturing includes fossil fuels alongside long-term positive environmental impact. Though these seem dichotomous, they currently exist in the industry. Their efficiency over time offsets upfront resource expenditure. Advancements will propel it into an even cleaner electric vehicle, but for now, they are still more beneficial for consumers and the planet than gas-powered cars.
Comments (0)
This post does not have any comments. Be the first to leave a comment below.
Featured Product
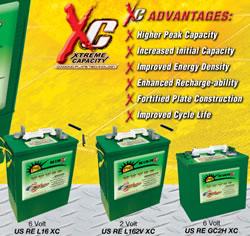