ESI Automotive Achieves 84 % Power Density Increase in EV Efficiency
The untapped potential of implementing vehicle efficiency improvements spearheaded by a systems-level approach to vehicle design have been further proven. The research, which was carried out by ESI Automotive and engineers of its customers, involved a series of real-world electric vehicle (EV) tests. The results clearly demonstrate the efficiency benefits of using silver sintering technology for inverter designs versus a soldered solution.
The findings are pivotal to further evidencing ESI Automotive’s vision that OEMs can generate valuable cost savings and vehicle efficiency improvements by taking a systems-level approach to the entire design and production process.
As part of its analysis, which focused on power cycling and thermal resistance measurements, ESI Automotive supported its customer replacing soldered die attach and wire bonding to a fully sintered top and die attach design. This enabled the inverter to operate at a higher power and temperature, facilitating miniaturization with a smaller cooling system. More specifically, the new SiC power module approach resulted in an increased power density of 84% and endurance of more than 10 times. A 33.8% reduction in weight was also reported.
Chris Klok, director of vehicle electrification at ESI Automotive says that these results are critical in demonstrating the widespread benefits OEMs can achieve, simply by switching from soldering to silver sintering for some EV designs.
“These latest real-life results are testimony to just how revolutionary silver sintering technology is. Not only can power density and reliability be increased, but silver sintering can also have a positive light weighting effect, which drives further vehicle efficiency improvements.
“These results are just a snapshot of what can be achieved now, and the direction cost-and-operationally-efficient EV design is heading in the future. By making the move to current SiC die technology, powertrain engineers benefit from numerous significant performance and reliability gains. This forms the foundation for optimising the traction inverter in the very near future.”
ESI Automotive utilizes ALPHA® Argomax® sintered silver, which has been successfully deployed in mass produced EV automotive inverter applications.
For more information about ESI Automotive’s pioneering systems led EV powertrain technology, visit
https://esiauto.com/evpowertrain/reliability/sintered-silver-technology-electric-vehicles
As part of its analysis, which focused on power cycling and thermal resistance measurements, ESI Automotive supported its customer replacing soldered die attach and wire bonding to a fully sintered top and die attach design. This enabled the inverter to operate at a higher power and temperature, facilitating miniaturization with a smaller cooling system. More specifically, the new SiC power module approach resulted in an increased power density of 84% and endurance of more than 10 times. A 33.8% reduction in weight was also reported.
Chris Klok, director of vehicle electrification at ESI Automotive says that these results are critical in demonstrating the widespread benefits OEMs can achieve, simply by switching from soldering to silver sintering for some EV designs.
“These latest real-life results are testimony to just how revolutionary silver sintering technology is. Not only can power density and reliability be increased, but silver sintering can also have a positive light weighting effect, which drives further vehicle efficiency improvements.
“These results are just a snapshot of what can be achieved now, and the direction cost-and-operationally-efficient EV design is heading in the future. By making the move to current SiC die technology, powertrain engineers benefit from numerous significant performance and reliability gains. This forms the foundation for optimising the traction inverter in the very near future.”
ESI Automotive utilizes ALPHA® Argomax® sintered silver, which has been successfully deployed in mass produced EV automotive inverter applications.
For more information about ESI Automotive’s pioneering systems led EV powertrain technology, visit
https://esiauto.com/evpowertrain/reliability/sintered-silver-technology-electric-vehicles
Comments (0)
This post does not have any comments. Be the first to leave a comment below.
Featured Product
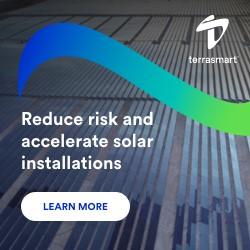
Terrasmart - Reduce Risk and Accelerate Solar Installations
We push the limits in renewable energy, focusing on innovation to drive progress. Pioneering new solutions and ground-breaking technology, and smarter ways of working to make progress for our clients and the industry.