How Can the Utilities Industry Benefit from Robotics?
Robotics technology has advanced quickly over the past few years, resulting in a range of new and expanded use-cases for industrial robots.
For the utility industry, these new robotics could offer significant benefits — and, in some cases, we’re already beginning to see how the adoption of robots can make utility work safer and more productive.
Improving Industry Safety With Remote Inspection
Drones and semi-autonomous robots can help keep workers safe by performing dangerous inspections that may otherwise put human workers at risk.
Inspection of tall structures, for example, can put workers at risk of falls. Inspecting power lines or damaged structures may expose workers to hazards like live wires and toxic fumes. Some structures — like incredibly narrow chimneys — may be too dangerous for human workers to inspect safely at all.
Businesses can use drones to inspect these structures, to reduce the risk of regular inspections, streamline the process, and minimize the needed equipment.
Drones, either piloted by an on-site human operator or controlled by innovative AI pathing algorithms, can scale structures, monitor power lines and inspect damaged assets, take photographs, or provide a live video stream that remote technicians can analyze.
These remote inspection drones are especially effective for isolated or hard-to-access structures typically, costly or time-consuming to inspect.
For example, it’s possible to inspect remote pipelines or power lines using drones that follow pre-programmed flight paths.
As the drone flies, it can take photos, capture video and gather other relevant data at regular intervals, providing the same information that human inspectors would gather without the same risks or labor requirements.
By simplifying and streamlining inspections, drones and other remote inspection robots can encourage businesses to investigate sites more frequently — allowing them to uncover problems that may have otherwise gone unnoticed.
For example, sites that need waterproofing may take advantage of sump pumps, which can be expensive to replace depending on the power required. Drones can inspect even smaller assets like pumps, allowing for the remote inspection of essential equipment.
Suppose a machine or asset has failed or is about to fail. In that case, data captured by drones can be used by a utility company to more effectively schedule maintenance or plan for a replacement, helping to reduce downtime and maintenance costs.
Combined with industrial IoT sensors and other devices that monitor asset performance, drones may enable utility companies to optimize the frequency of inspections. Checking in on sites when it’s likely that critical equipment has broken down or begun to malfunction, allowing for the fastest possible maintenance response.
Robot Tunneling and Demolition
Utility companies are experimenting with the use of robots to streamline tunnel construction and demolition.
In many cases, tunneling is accomplished with four to five-person crews equipped with hand tools — making the process of tunneling both labor-intensive and inefficient.
Projects like utility tunneling may also require heavy machinery, explosives and exposure to potentially dangerous chemicals or fumes, meaning that those crews may be exposed to hazards while at work.
Remote-controlled tunneling or demolition robots can replace human workers with remote operators that can work safely at a distance.
These robots can also be more consistent and more efficient at moving earth than human tunneling or demolition crews, helping accelerate the construction of new tunnels and allowing utility companies to utilize available labor power more efficiently.
Like most other industries, the utility industry faces a growing labor gap — automation and robotics are two strategies that may help the industry prepare for future labor shortages.
Various tunneling robots exist, enabling businesses to take advantage of different tunneling and demolition strategies. For example, novel hydrodemolition robots use high-pressure water to remove loose or deteriorating concrete from tunnel walls, allowing businesses to begin tunnel maintenance without requiring human workers for the demolition process.
These robots may be used with more conventional remote demolition robots — which can leverage tools like breakers, buckets and drum cutters — for new tunnels and tunnel maintenance.
Autonomous Line Repair and Digging
The timely repair of buried utility lines can be a significant challenge for any utility company. Often, the process takes several days and may require multiple lane closures and the deployment of heavy equipment. During the excavation process, workers can also be at serious risk. When ruptured by excavation, pipelines can release natural gas that is both toxic and flammable, potentially causing explosions.
New autonomous line repair robots are capable of excavating, repairing and reburying gas lines.
While the process of line excavation and repair is typically a two- or three-day effort, these robots may be able to complete the entire process of repairing and reburying lines in just over an hour. This faster construction time means less exposure to risk, less downtime and less need for extended lane closures.
As with other robots, the machines may help businesses use labor power more efficiently. Excavating lines by hand may require a crew of several workers equipped with hand tools. Heavy machinery can speed up the work, but requires a worker to sit in an excavator, potentially exposing them to hazards like the release of dangerous chemical fumes.
The robot excavator requires supervision from just two workers, both of whom can operate the robot at a safe distance. The excavator can accomplish this with a combination of custom tools and an AI platform that allows it to semi-autonomously navigate the dig site and complete tasks without significant human input.
In the event that a pipeline is struck, the workers won’t be in harm’s way.
Like other robotics use-cases, these robots may make the industry both more productive and safer. Using a robot to excavate buried utility lines and pipes can accelerate the process while keeping workers safe from associated hazards.
Utility Companies Can Adopt Robots to Increase Productivity and Safety
New robotics technology can help utility companies streamline work that is often difficult, tedious and unsafe.Drones, excavation robots and demolition robots are all operated remotely to perform work that puts employees at risk — like the inspection of unsafe structures or the excavation of buried gas lines.
As robot technology advances, these machines may become increasingly autonomous, allowing utility companies to accomplish even more with their labor.
Comments (0)
This post does not have any comments. Be the first to leave a comment below.
Featured Product
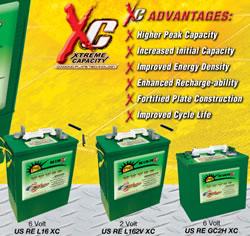