Lead Acid Battery Install and Maintenance Tips
Steve Higgins, Technical Services Manager at Rolls Battery highlights some of the frequently asked questions when it comes to proper maintenance and service of lead acid batteries.
When do I perform an EQ Charge?
If you are properly charging a lead acid battery bank to full on a regular basis, you should never have to EQ a battery bank.
If you have developed a difference in measured SG's of more than .025 to .030 points then a corrective EQ may be required.
Corrective Equalizations should be performed when the battery bank is at 100% SOC. Review and complete the provided preparations before initiating the Equalization charge.
Equalization time will vary depending on the level of sulfation, balance of charge, size of the battery bank and available charging source. Typically, a corrective Equalization is necessary every 60 to 180 days to desulfate and balance a battery bank in systems which are deficit cycled and/or charged at lower charge currents. If multiple parallel strings show charge imbalance it may be necessary to equalize each string individually.
It is important to monitor specific gravity and voltage throughout the Equalization process. When specific gravity readings remain constant for 45-60 minutes this generally indicates completion.
Preparation:
- Required Equipment: protective goggles, rubber gloves & rubber boots, hydrometer or refractometer, voltmeter, distilled water, baking soda or soda ash for possible overflow or spills
- Standard 1/4-turn bayonet caps and Rolls R-Cap flip-top recombination caps may be left on during this procedure. Dirty or clogged caps may prevent the release of hydrogen gas. Inspect and clean caps as necessary. Hydrocaps must be removed.
- Check each cell for low electrolyte levels and/or exposed plates and top up with distilled water as necessary. If the cells require watering, do so before starting the Equalization process to allow sufficient mixing with the existing electrolyte. Be careful not to overfill as the electrolyte will bubble and may overflow during the process.
- Program the Equalization voltage as recommended in Rolls Flooded Charging Parameters starting at the lower end of the voltage range for newer models.
Procedure:
1. Complete a Bulk & Absorption charge to bring the battery bank to 100% SOC before starting a corrective Equalization.
2. Measure the temperature of a test cell and record the specific gravity of each cell in the battery bank. Identify cells with high/low readings.
3. Initiate the Equalization charge mode at a steady low DC current (5-10% of C/20 battery capacity). If grid power is not available, use a DC power source (generator) or PV array with sufficient current when possible.
4. Specific gravity will rise across the battery bank, ideally reaching 1.265-1.270 in each cell upon completion. Readings in some cells may be slightly elevated due to electrolyte temperature (Ex. 1.280) and will return to normal when cooled but should not exceed 1.30. If the cell temperature rises above 46ºC (115ºF) and approaches 52ºC (125ºF), terminate the Equalization process and allow the batteries to cool. If available, check individual cell temperatures using an IR temp sensor to isolate any possible damaged cells.
5. If cells are severely sulfated it may take several hours for the specific gravity to rise and/or balance. If the readings plateau for 45-60 minutes, but do not reach 1.265-1.270, stop the process to prevent cell damage and allow the batteries to cycle normally for 2-4 weeks before repeating. The cells will continue to desulfate following an Equalization as sulfate dissolves during normal charging.
Allow the battery bank to cool for 1-2 hours. Check and record the specific gravity of each cell. The gravities should be 1.265 ± 0.005 or lower. Check electrolyte levels and add distilled water as necessary.
It is recommended that a specific gravity reading of one pilot cell is measured and recorded on a regular basis when it is thought that the bank is fully charged. The measurement should be compared to previous readings. If the measurement is lower than the previous reading, longer absorption times and/or higher voltage setting should be used. The longer the Absorption time and the higher the Bulk voltage, the more water will be consumed but less Equalization will be required.
NOTE: The specific gravity should rise as the cells use water. Look for trends in the specific gravity over a period of time and make small adjustments as necessary.
When putting distilled water into a battery, where do you fill the water level to?
ELECTROLYTE - ADDING DISTILLED WATER
Only distilled (preferred), deionized or reverse osmosis water should be used in Flooded battery cells. Improper watering may cause internal cell damage. Test water to confirm a PH reading of 7 or less and no Total Dissolved Solids (TDS < 5 PPM).
NOTE: Do not add sulfuric acid to Flooded battery cells during normal top up. In the case of accidental spill, premixed electrolyte (1.265 S.G.) may be used to refill cells.
CAUTION: Do not add water or electrolyte to cells before initial charging unless plates are exposed. If so, add distilled water until plates are submerged. Please contact Rolls Technical Support if you have any questions or concerns.
NOTE: If the battery cells require watering more than once every two (2) months the programmed charging voltages may be too high. Adjust and monitor accordingly. If a particular cell requires significantly more water than others this may be a sign of charge imbalance in the battery bank caused by resistance and/or cell failure. Typically, Series 4000 & 4500 models will require watering every 30-60 days. Series 5000 batteries generally require watering every 60-90 days as these models are designed with a higher electrolyte reserve allowing longer watering intervals. Frequency may vary considerably due to operating temperature, depth of discharge, cycle frequency and humidity.
Water Levels should be no higher than 6 to 13mm from the bottom of the fill tube in the battery (See below drawing as an example).
For flooded model cell spacing reference information used in sizing watering systems, refer to the following Flooded Cell Spacing document.
Where should my battery temperature sensor be mounted?
For charge accuracy and safety, many systems use a sensor mounted to the battery to measure cell temperature and adjust charge voltage accordingly. Temperature sensors should be installed directly on the side of a cell or battery in the center of the bank and must be securely mounted below the electrolyte level to determine accurate cell temperature. When using chargers that do not feature temperature compensation, voltage settings should be monitored and adjusted based on actual cell temperature. Failure to use or properly install the provided sensor may cause damage due to over/undercharge which is not covered under Rolls Battery manufacturer warranty. As a precaution, this sensor may also trigger a programmed safety charge cut-off as the battery bank should not exceed an operating temperature of 52ºC (125ºF).
Series 4000, 4500, VRLA AGM & OPzV GEL models – the temperature sensor should be mounted on a battery in the middle of the string or battery bank. To ensure an accurate reading of cell temperature, the sensor must be mounted below the liquid level on Flooded models and not attached to a terminal or top of the battery case as these areas are generally cooler than the internal cell. For traditional Flooded, VRLA AGM & OPzV GEL models, Rolls recommends attaching the sensor half way down the side of the battery and/or 10-12cm (4-5”) from the top of the case for the most accurate temperature reading.
Dual-Container Models – If the battery has a modular, dual-container construction, the temperature sensor must be mounted directly to the side of an internal cell. To access the cell, disconnect the terminal connections and remove the outer cover which snaps on to the case or may use small removable plastic pins. Mount the sensor to the internal cell and run the connecting cable between the case, being careful not to pinch or damage the wire when placing the cover back on. Automotive silicone is used to seal around each terminal to protect against spills, dust & debris. This may be reapplied when the case has been reassembled.
Dual-Container Models - Remove case cover. Mount sensor to the side of internal cell below liquid level. Replace the cover and re-seal around terminals with silicone.
Sensors should not be mounted to the top of the battery case/cell or terminal as this does not provide an accurate temperature reading of the electrolyte.
See infrared temperature shown below:
Rolls product lines offer premium deep cycle batteries in a wide range of voltage and capacity options. The Rolls brand and distinctly red cases are well-recognized around the world and represent our longstanding commitment to deliver outstanding quality, dependablility and support. Rolls flooded & sealed batteries are chosen by industry professionals and customers time and time again.
Comments (0)
This post does not have any comments. Be the first to leave a comment below.
Featured Product
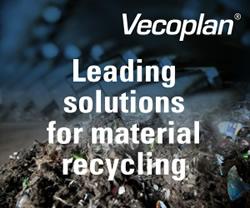