Stainless steel lends long life to Merkur wind farm structure
High-performance duplex stainless steel is playing an important role in ensuring a long life for key components at Merkur Offshore Wind Farm near Borkum Island in the North Sea. The wind farm is one of Germany’s largest, with 66 turbines generating 1,750 gigawatt-hours per year, enough to cover the energy needs of about half a million homes.
With offshore wind farms like Merkur expected to generate energy over an operating life of 25 years, operation and maintenance typically accounts for 15-25 percent of their total lifecycle cost.
Smart specification of materials for important components can minimise the need for inspection and maintenance and help operators to control costs. This is particularly true for the transition pieces that form part of the foundation structure of the monopile turbines supplied by Windar Renovables and Idesa for Merkur.
In monopile construction, a single pile is driven into the sea bed and a transition piece is fed over it like a sleeve, with the turbine secured on top. Once in operation, the turbine will export power through a cable connection that runs through the transition piece, which must be water and air tight to protect the interior from corrosion.
However, monopiles and transition pieces face tough conditions during operation, including freezing temperatures, strong currents and winds and corrosive sea water. As a result, the sealing grout can fail, leading to corrosive pitting of the interior, including the connecting bolted flanges or brackets that hold the transition pieces in place. These flanges are a critical part of the design. Not only do they carry the full weight of the turbine but there is no access to the interior, so it’s not possible to carry out inspection or apply protective coatings after installation.
Resisting stress corrosion cracking
Surface corrosion on its own may not be a major issue for a support bracket in a less challenging environment. But the bolted flanges in the turbine transition pieces are also subject to large cyclic stresses as the wind, waves and tides flow around the structure.
And the taller and more powerful the turbines, the greater the loads. In the case of Merkur, its GE Haliade 150-6MW turbines rise 177 metres above the water and generate up to 6 MW, while the foundations will need to withstand loads from constant winds and a large tidal range of up to 3.5 metres.
This combination of factors can lead to stress corrosion cracking on the bolted flange, with corrosion pitting sites forming the start of microscopic cracks, which could propagate and lead to catastrophic failure if left unchecked.
To avoid the formation of pitting sites in the first place, Windar and Idesa turned to Outokumpu to supply 40 tonnes of Forta DX 2205 duplex stainless steel for the brackets on the 6 metre diameter transition pieces.
Duplex stainless steel offers a good combination of corrosion resistance and high strength to provide a long and trouble-free life for the flanges.
Corrosion resistance and high strength
The properties of duplex grades of stainless steel are possible due to the alloy composition and microstructure, which combines the structures of the two other most important types of stainless steel: ferritic and austenitic. Duplex stainless steel also offers good resistance to abrasion and erosion, as well as fatigue. In addition, they have low thermal expansion.
Because duplex grades have around twice the strength of austenitic stainless steels, designers have the option to reduce the profile of components – saving both weight and cost of materials. Outokumpu has developed duplex counterparts to the standard austenitic grades that offer similar corrosion resistance with twice the strength.
Extremely high mechanical loads
When asked about the steel for the brackets, Sergio Altolaguirre, Sales Manager for Marine Energy Projects at Idesa said: “Duplex is used in special support parts that bear metal-on-metal contact, exposed to extremely high mechanical loads. The choice of duplex relates to two reasons. First, the project required a high resistance to corrosion. Second, the support parts required a material with a yield strength higher than 355 megapascals. The grade offered and supplied by Outokumpu complies with both criteria.”
“At Idesa and Windar we have a long relationship with Outokumpu, based on our close collaboration in previous projects. Outokumpu is part of our list of approved suppliers and is one of our preferred options for stainless steel plates with special requirements.”
Comments (0)
This post does not have any comments. Be the first to leave a comment below.
Featured Product
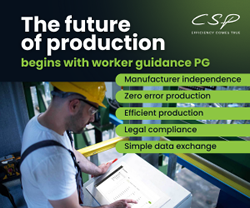