New process for manufacturing PV cells means cheaper solar power
Phys.org: A major roadblock to the mass use of solar energy are photovoltaic (PV) solar cells. This is because the cost, inefficiency and negative environmental impact that the manufacturing of these cells outweighs any potential savings provided by the resulting solar energy. If, however, cost could be were minimised, then solar power would be more able to compete with traditional fossil fuel-based methods for generating energy.
To overcome this hurdle, the EU-funded SOLNOWAT project has developed an innovative dry process for manufacturing PV solar cells.
PV cells are typically created via a wet chemical process that etches away layers of silicon from a crystalline wafer, leaving behind the solar cell. The SOLNOWAT process replaces the expensive and inefficient wet chemical process with the use of atmospheric pressure dry etching technology – a process that cuts costs and speeds up production. Because less silicon is removed during dry etching, the resulting cells are darker, making them very efficient at absorbing light. In fact, they are so efficient that they have been classified as having zero global warming potential. Cont'd...
Comments (0)
This post does not have any comments. Be the first to leave a comment below.
Featured Product
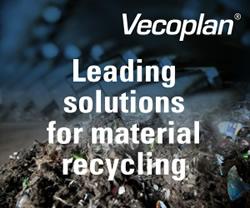