DNV LEADS WIND ENERGY DEVELOPMENT WITH INDUSTRY STANDARD FOR NEXT GENERATION BLADES
The improved rotor blade certification standard was updated through a long-term joint industry project (JIP) to reflect the latest needs of wind turbine owners and manufacturers to ensure safe and reliable rotor blades
Høvik, 29 May 2024 — DNV, the independent energy expert and assurance provider, has led an innovative initiative resulting in the revision of the DNV-ST-0376 rotor blade standard, in response to the dynamic landscape of wind turbine development. This update, a product of joint industry collaboration, marks a significant milestone in enhancing reliability and safety within the wind energy sector.
"The pace of modern wind turbine development demands that industry standards keep pace with changing trends and technologies. Through the development of industry service documents such as service specifications, standards, and recommended practices, DNV is actively engaged in driving the renewable energy sector forward. This update underscores our commitment to driving innovation and quality within the wind energy sector," adds Kim Sandgaard-Mørk, Executive Vice President for Renewables Certification at DNV. "By prioritizing reliability and safety, we aim to bolster industry confidence and propel the global transition towards sustainable energy solutions."
"Not all wind turbine blades are created equal," says Christopher Harrison, Principal Engineer and Service Line Leader for Component Certification, Energy Systems at DNV. "Different design assumptions and methods, along with varying performance during validation tests, can result in differing blade performance over their lifespan. As stakeholders in the wind energy sector, it's crucial to understand and mitigate these risks."
During the project, 26 leading companies across the wind turbine sector, including manufacturers, operators, and certifiers, contributed to refining and reviewing the standard. This inclusive approach ensures a comprehensive framework that caters to the diverse needs of the industry ecosystem.
Key highlights of the updated standard include:
• Enhanced reliability through rigorous requirements and approaches.
• Alignment with international standards, facilitating streamlined certification processes.
• Introduction of novel concepts such as damage tolerance, elevating safety standards to new heights.
• Greater focus on design for manufacture and understanding the relationship between manufacturing quality and reliability.
Unlike previous standards solely focused on safety, DNV-ST-0376 sets a new benchmark by incorporating reliability as a cornerstone principle. The initiative focused on three key areas:
1. Quality Design Standard: DNV revised the blade standard DNV-ST-0376 to address real-world failure modes and defects for large flexible blades in multi-megawatt turbines.
2. Alignment with other international standards: DNV aligned requirements in DNV-ST-0376 with IEC 61400-5 where possible, with input from other certification bodies.
3. Stakeholder Education: DNV conducted seminars in Hamburg, Copenhagen, and Shanghai to educate developers, owners, and operators on the relationship between design assumptions, testing performance, and long-term blade functionality, enabling informed decisions in turbine certification.
"Our goal was to provide wind turbine stakeholders with the tools and knowledge necessary to navigate the complexities of blade development," concludes Christopher Harrison. "By working together through this point industry project, we could drive improvements in standards that benefited the entire industry."
For more information on DNV's commitment to wind turbine reliability and safety, please refer to the white paper.
Featured Product
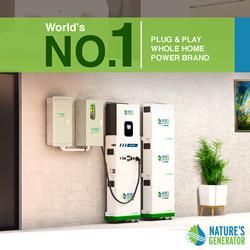