Dutch-Belgian consortium builds the first commercial plastic-to-oil plant of Europe
The first commercial plant in Europe where waste plastic is recycled into valuable fuel will be built by the Dutch company BlueAlp on behalf of a Dutch-Belgian consortium. This means that The Netherlands and Belgium are at the forefront of giving end-of-life plastics a new future as fuel.
The plant will be built in Ostend, Belgium, on the site of the circular waste processor RenaSci and uses the Dutch BlueAlp technology and patent. The consortium consists of the Dutch technical service providers Mourik and Petrogas, oil and fuel supplier Den Hartog and the Belgian RenaSci. At the end of December 2019 the plastic-to-oil factory will be put into operation.
'Worldwide, wizards experimenting with the recovery of raw materials from waste plastic. We have succeeded in developing a process in which nearly 100% of the waste plastic is reused and money can also be earned. This is a great example of how the circular economy contributes to a sustainable future', says Chris van der Ree, managing director of Petrogas and co-initiator of the project.
Plastics are also circular
Van der Ree: 'The secret behind this innovative process is a patented way of converting plastic to oil. Simply explained, the plastic waste is first cleaned and sorted in a high-tech waste preparation installation. What remains are plastic shreds. Then the chips are melted and further heated in a reactor until vapor is formed. This vapor is collected and then cooled down, after which oil is formed. The process can yield different types of oil, but the most important product is diesel based on EN590.'
BlueAlp has developed its technology in such a way that it knows exactly the temperature at which the waste plastic can be slowly separated into smaller hydrocarbon chains. This method yields higher efficiency than the methods used in other experimental pilots. There the temperature is often increased too quickly and too high, causing part of the plastic to burn.
Van der Ree: 'We produce almost 1 liter of oil from 1 kg of plastic and we have a yield of more than 80%. In addition, the CO₂ that is released is not emitted but reused as raw material for the factory. Figures show that BlueAlp technology does not release 1,200 kg of CO₂ per ton of processed plastic waste and that the production of 1 liter of oil is 68% less environmentally harmful than the production of one liter of normal fossil fuel. The BlueAlp plant processes 21,000 tons of waste plastic on an annual basis.'
The cost of building a plastic-to-oil plant is a relatively low investment of €15 million. With the intended return has a return on investment relatively quickly and at the same time contributes to the circular economy.
The plant will be built on the site of the circular waste processor RenaSci in Ostend, Belgium. 'Every year, 120,000 tons of waste comes in. This is sorted and the plastics that are difficult to process enter the plastic-to-oil factory. 'In this way, for example, we reuse agricultural plastics and the plastic foils that are used to keep food fresh. That is normally all burned. We on the contrary, make new raw materials.'
According to Van der Ree there are many international parties that want to purchase such a factory. 'But we will only conclude contracts at the end of this year. We want to gain even more experience this year. If you put an IKEA cabinet together for the first time with a manual on paper, it is a puzzle. But the second one goes fast and efficient. For example, we see the construction of the first commercial plant as a training and experience trajectory for our professionals. After completion, we know exactly what the construction of an plastic-to-oil factory entails, and we can process this into new contracts. We are preparing for the construction and delivery of many factories.'
In total, only 20 employees are required to run the factory. A limited number of staff for the office and then another 5 teams of 4 employees to be able to run full-time.
The BlueAlp technology has been tested, demonstrated and successfully used in a test factory in Switzerland. After the successful completion of that experiment, the factory was dismantled again. The independent institute Energy Research Center Netherlands (ECN) has studied the entire process and assessed it positively.
Featured Product
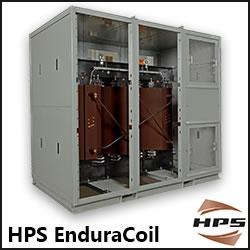
HPS EnduraCoilTM Cast Resin Medium Voltage Transformer
HPS EnduraCoil is a high-performance cast resin transformer designed for many demanding and diverse applications while minimizing both installation and maintenance costs. Coils are formed with mineral-filled epoxy, reinforced with fiberglass and cast to provide complete void-free resin impregnation throughout the entire insulation system. HPS EnduraCoil complies with the new NRCan 2019 and DOE 2016 efficiency regulations and is approved by both UL and CSA standards. It is also seismic qualified per IBC 2012/ASCE 7-10/CBC 2013. Cast resin transformers are self-extinguishing in the unlikely event of fire, environmentally friendly and offer greater resistance to short circuits. HPS also offers wide range of accessories for transformer protection and monitoring requirements.