Schletter Group presents new ground mount system at SPI
The manufacturer of solar mounting solutions with international operations thus continues its innovation campaign, which focuses on yield optimization based on smart design decisions.
Charlotte, NC, September 13, 2019. Less material per kW of installed capacity, a faster assembly and a higher load capacity: The Schletter Group introduces the next generation of its ground mount system FS at the Solar Power International (SPI) fair in Salt Lake City. The manufacturer of solar mounting solutions with international operations thus continues its innovation campaign, which focuses on yield optimization based on smart design decisions.
"We have radically redesigned the third generation of our globally implemented FS open area system to optimize yields," says Florian Roos, CEO of the Schletter Group. The new FS Gen 3 uses less material per kilowatt output - with the same or even higher load-bearing capacity. In addition, the system is easier to assemble than ever before, thanks to the targeted optimization of individual components. "With our FS Gen 3, customers save time and money during the installation and optimize their return on investment," Roos adds.
20 percent span increase possible
For the pile driven foundations, girders and purlins of the FS Gen 3, Schletter is using high-tensile steel, which is usually only used in the automotive and the mechanical engineering industry. At the same time, the Schletter engineers have fundamentally redesigned the geometry of the purlins: instead of following a Z profile, the cross section of the purlins is formed as a downward opening, symmetrical trapezium.
The new shape in combination with the new material significantly increases the load capacity of the purlins. The new purlins can support spans of up to 6.5 meters, i.e. around 20 percent more than the previous generation. This means that with the FS Gen 3, more PV capacity can be installed on fewer supports.
And the new geometry also adds another functionality to the purlins: they also serve as cable tray. With the new FS Gen 3, string cables are fed through the purlins and thus protected against wind and weather as well as UV radiation. This renders the cumbersome and expensive application of cable ties obsolete.
Quick and cost-effective installation without drilling
In order to reduce the time needed to assemble the system, Schletter has also fully optimized and aligned its individual components. Most connections are based on clamps. The construction is so designed that no on-site drilling or pre-punching of holes, which used to require intensive planning, is necessary.
This allows for a maximum of flexibility during installation: as the clamping connections benefit from flexible connection points along their individual axes, they offer sufficient leeway to align them to the local conditions in a fast and simple manner. "At every installation, changes have to be made on-site that cannot be planned beforehand such as fine adjustments to the pile driving result," says Dr. Ing. Cedrik Zapfe, Chief Developer of the Schletter Group. "With the new FS Gen 3, this is not a problem."
Modules mounted without ladders and lifting platforms
In order to also simplify and accelerate the mounting of modules, the Schletter engineers have developed a new rafter lay-in system. The modules are simply pushed in from below between the tilted rafters and then fastened with a slip guard. "The modules can therefore be mounted without any ladders or lifting platforms," Zapfe stresses. "This is not only significantly faster but also safer and more economical - an enormous advantage, especially for customers in the USA and other Anglo-American markets with their strict health & safety regulations."
The rafter assembly can be used for frames of 30, 35 and 40mm in thickness. Frameless modules or other module strengths can still be fastened with clamp-based rafter systems.
Structural safety and geological survey
The system is available with one (FS Uno Gen 3) or two supports (FS Duo Gen 3) and is intended to become the Schletter Group's standard open space system in all of its markets. As for all other open-space systems, the Schletter Group can also provide the entire structural statics based on a geological survey. In addition, structural statics are adjusted to the applicable regional load values and country-specific standards. For sites with high wind loads or the risk of earthquakes, Schletter integrates these risks into its planning based on vibration and earthquake simulations.
Tracking system for bifacial modules
In addition to the new FS Gen 3, the Schletter Group will also present a version of its tracking system that has been optimized for bifacial modules at the SPI. The Schletter Tracker was launched in 2018 and has since been installed in Europe, Africa and Australia. Its specific design includes a patented, mechanical self-locking system: there is a mechanical locking element on each post, which locks automatically if the row is not moved. This eliminates all wind-induced vibrations (so-called galloping effect) for the entire row. When in the resting position, the system therefore has the characteristics and resilience of a fixed installation, suitable for wind speeds of up to 260 km/h. There is a mechanically locking element on each post, which locks automatically if the row is not moved.
The Schletter Group presents itself at SPI in Salt Lake City, September 23-26, booth 5407.
About the Schletter Group
The Schletter Group is one of the leading manufacturers in the world of photovoltaic mounting systems made of aluminium and steel. The Group manufactures mounting systems for roofs, façades and open areas (solar farms) as well as solar carports. With production facilities in Germany and China as well as an international network of distribution and service companies, the Schletter Group is active in all important international markets. The Schletter Group has around 700 employees in total.
www.schletter-group.com
Featured Product
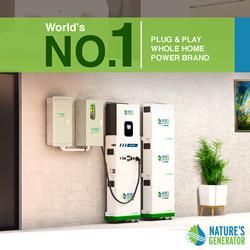