ULVAC Launches Sales of Two Ion Implanters for Power Devices
Low-acceleration ion implanter "SOPHI-30" and high-acceleration ion implanter "SOPHI-400" used for ultrathin wafers processing for power devices
Chigasaki, Japan - (JCN Newswire) - ULVAC, Inc. launches sales of low-acceleration ion implanter "SOPHI-30" and high-acceleration ion implanter "SOPHI-400" used for ultrathin wafers processing for power devices.
Background
There is an increasing demand for power devices in the automobile, railway and home appliance markets, and various technologies such as Insulated Gate Bipolar Transistor (IGBT), Silicon Carbide (SiC) and Gallium Nitride (GaN) are being developed.
In addition to the products developed and sold for power devices, ULVAC developed and launches sales of two types of ion implanters for IGBT.
In recent years, productivity improvement in the low-acceleration and high-concentration ion implantation process is required for the products (RC-IGBT)*1 that IGBT and diode are integrated into a single chip in order to reduce drive power loss, increase switching speed, improve characteristics and downsize the module.
ULVAC developed and has launched sales of two ion implanters; SOPHI-30 and SOPHI-400. "SOPHI-30" is an ion implanter to perform low-acceleration and high-concentration ion implantation achieving extremely high productivity by reducing the process time to 1/60 in comparison by ULVAC previous models. "SOPHI-400" is a high-acceleration ion implanter, which reduces drive power loss, increases switching speed and performs the process with acceleration voltage up to 2.4MeV. (Applicable ranges are shown in Fig.1 and Fig.2).
Outline of the technology
1. Low-acceleration and high-concentration ion implanter, "SOPHI-30"
When IGBT and diode are integrated into a single chip, reverse-conducting IGBT (RC-IGBT) requires the low acceleration and high concentration process to reverse P-shape part in the collector on the backside of the thin wafer to N-shape.
Conventional ion implanter using low acceleration and high concentration process require long process time thus productivity was low and was a bottleneck. In the low acceleration and high concentration process of the large current ion implanter with high productivity, several wafers are rotated by the discs during the process, which may break thin wafers. Therefore, single-wafer medium current ion implanter has been used for this process although productivity in the low acceleration and high concentration range is low.
We have solved the problems of the conventional ion implant process and developed a new ion implanter to perform low acceleration and high concentration (1/60 process time in comparison to ULVAC previous models). Also, single-wafer processing is utilized for the ultrathin wafers to overcome wafer breakage.
In the existing ion implanter, the distance between ion generationer and wafer is long and beam current is lost during beam transport with low acceleration, and it takes 10 minutes to process 2E15ions/cm2 for one wafer with 20keV.
In SOPHI-30, beam transport distant is maximally shortened to improve beam transport efficiency, and one wafer can be processed with the same recipe in 10 seconds (1/60 in comparison to ULVAC previous models) and footprint is reduced by two-third (in comparison to ULVAC previous models).
Features of SOPHI-30
(1) Low acceleration and high concentration process: 10 seconds for one wafer
1/60 in comparison to ULVAC previous models (10 min -> 10 sec)
(2) Footprint is reduced by two-third and price is reduced by half (in comparison to ULVAC previous models)
(3) Applicable for ultrathin wafers
2. High-acceleration ion implanter, "SOPHI-400"
As IGBT characteristics improvement, reduction of drive power loss and increase of switching speed are required. To realize this characteristics improvement, high-accelerating ion implantation with acceleration voltage of approx. 2MeV (2,000keV) from the back side of the ultrathin wafer to the field stop layer*2 is necessary. SOPHI-400 enables ultrathin wafers to be handled by single-wafer processing with acceleration up to 2.4MeV. In addition, field stop layer can be formed by using hydrogen (H) as a next-generation process. Hydrogen forms approx. 4um-deep profile, which reduces drive power loss and improves switching characteristics.*3 Also, hydrogen enables activation at low temperature and process by furnace (annealing) equipment without using expensive laser anneal, which can reduce total production cost.
Features of "SOPHI-400"
(1) Phosphorus (P) ion implantation up to 2.4MeV (2,400keV) is available
(2) Field stop layer process using hydrogen (H) is available
(3) Applicable for ultrathin wafers
*1 Reverse-Conducting Insulated Gate Bipolar Transistor
Device that IGBT and diode are integrated into a single chip
*2 Field stop layer: When thin wafer is used for characteristics improvement, withstand voltage is insufficient. To compensate thick n+ layer is implanted into n-base layer. This n+ layer is called FS layer. The term, Field here means high electrical field and Field Stop layer (FS layer) means the layer to stop high electrical field.
*3 Patent-pending technology
Future prospects
ULVAC believes that this technology contributes greatly to process time reduction and characteristics improvement in the IGBT manufacturing process. We continue to provide ion implanters, sputtering equipment and etching equipment as "ULVAC Solutions" to enhance performances of power devices and environmental devices.
ULVAC will be exhibiting at SEMICON WEST at Moscone Center in San Fransisco, CA, USA on 7/11-13.
Full release with Figures can be viewed at https://www.ulvac.co.jp/en/information/20170706/
System appearance
Low-energy ion implanter "SOPHI-30" -- http://bit.ly/2tOEFzZ
High-energy ion implanter "SOPHI-400" -- http://bit.ly/2tTqY3T
Featured Product
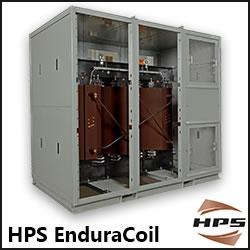
HPS EnduraCoilTM Cast Resin Medium Voltage Transformer
HPS EnduraCoil is a high-performance cast resin transformer designed for many demanding and diverse applications while minimizing both installation and maintenance costs. Coils are formed with mineral-filled epoxy, reinforced with fiberglass and cast to provide complete void-free resin impregnation throughout the entire insulation system. HPS EnduraCoil complies with the new NRCan 2019 and DOE 2016 efficiency regulations and is approved by both UL and CSA standards. It is also seismic qualified per IBC 2012/ASCE 7-10/CBC 2013. Cast resin transformers are self-extinguishing in the unlikely event of fire, environmentally friendly and offer greater resistance to short circuits. HPS also offers wide range of accessories for transformer protection and monitoring requirements.