Intersolar - BMZ Updated ESS 7.0 Energy Storage System shown at InterSolar North America
ESS Scalable to six units totaling 40.44kWh of Energy Storage
VIRGINIA BEACH, Va., July 12, 2016 /PRNewswire/ -- BMZ USA, Inc., The Innovation Group, the U.S. subsidiary of BMZ GmbH, Germany, Europe's largest and most recognized battery assembler and known worldwide for innovative battery assembly and integration, announces their latest Energy Storage Solution, the ESS 7.0 with scalability.
The ESS 7.0 is now scalable to a total of six units with an additional combiner box and latest firmware, for a total of 40.44kWh of storage, with additional future testing to be expandable to 12 units totaling 80.88 kWh.
Currently being delivered, the new ESS offers exceptionally high performance in a modern, aesthetically pleasing design intended for residential and small commercial grid-tied or off-grid backup, and peak shaving/time of use configurations.
This product is the only lithium battery energy storage device currently on the market that is certified by SMA to work with the Sunny Island battery inverters, worldwide.
See full product details on company web site: http://www.bmz-usa.com/products/pv-energy-storage/ees-70/0,2,504846,373.html
The 48V system with CAN BUS communication has an 80% Depth of Discharge, offering 5.39kWh usable storage. This high efficiency unit offers a great total return on investment when considering the now ten year warranty at 5,000 cycles, with an expected potential life span of up to 20 years.
About BMZ USA
BMZ USA, Inc. headquartered in Virginia Beach, VA is the North American subsidiary of BMZ GmbH and a worldwide leader in battery assembly and innovation. With a global network of offices and representatives the company has over 1,400 employees and manufacturing in Germany, Poland, China and the U.S. The company provides battery assembly solutions for commercial, industrial, medical, military, recreational, transportation, energy-storage and e-mobility applications.
Featured Product
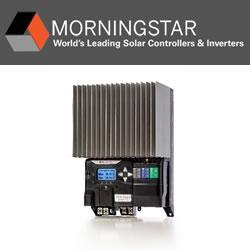
MORNINGSTAR - GenStar MPPT
GenStar MPPT is the industry's first fully integrated solar DC charging system, an all-new design with "lithium DNA" from the leader in charge controllers. Out of the box, GenStar is an overachiever-delivering legendary Morningstar quality, efficiency, power and reliability along with the latest in advanced communications and control technologies. All the most installer-requested features are on-board; additional features can be easily added via Morningstar's ReadyBlock expansion technology, with snap-in blocks that provide battery metering and monitoring, signaling and load control, and lithium battery communications/control