AllCell Technologies Working on ARPA-E Grant for Advanced EV Battery Development
The project objective is to develop an EV battery that can act as a structural component of the vehicle, supporting structural loads and absorbing impact energy during collisions.
April 22, 2014– AllCell Technologies, producer of safe and long-lasting lithium-ion batteries, is working on a program led by Stanford University to develop advanced electric vehicle (EV) batteries through an ARPA-E grant. The program, titled "Robust Multifunctional Battery Chassis Systems for Automotive Applications," will integrate lithium-ion battery systems into vehicle structures, generating significant savings in cost and weight, which in turn improve drive range and efficiency. The project team estimates the new battery would reduce total vehicle weight by more than 40%.
Supported by AllCell and lithium-ion cell producer Envia Systems, the project objective is to develop an EV battery that can act as a structural component of the vehicle, supporting structural loads and absorbing impact energy during collisions. AllCell's proprietary thermal management material, which employs phase change materials (PCM) to absorb and distribute heat to improve battery performance and safety, is a key component of the new battery design. University material research experts and AllCell's thermal management experts will collaborate to create a new generation of PCM-based materials that are optimized to both provide thermal management and improve crash worthiness by absorbing impact energy. The new material will be equipped with advanced sensors and will be integrated directly into the battery system.
"To date, lithium-ion batteries have been considered liabilities in automobile crashes," said AllCell CEO Dr. Said Al-Hallaj. "We are turning that notion on its head. With the support of this program, our new material will not only thermally protect the lithium-ion cells within the battery, but will also assist in mechanically protecting vehicle occupants from the physical force of a collision."
Featured Product
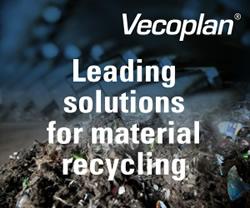