Parabolic Trough or Solar Tower? A technology decision
Securing cost reductions and carving out routes to grid parity remains as ever the most pressing issue for the CSP industry.
At the crux of this pursuit is understanding the associated costs of the CSP technologies themselves, whether it be Parabolic Trough, Solar Tower, Linear Fresnel or Dish Sterling. Delving even deeper, the ability to identify and successfully implement cost reduction strategies is dependent on understanding where exactly the bulk of costs currently rests within these technologies.
CSP Today's Technology reports has recently analysed the costs of Parabolic Trough and Solar Tower and found that CAPEX costs varied by only 1% between these technologies. However the percentage of costs distributed between EPC, developer and solar field provided more significant variation.
Parabolic Trough
For a reference plant with a 110 MW gross, 6 hours of TES and dry cooling located in the MENA region the CAPEX represented the largest portion of lifecycle costs, accounting for 48%.
The distribution of CAPEX costs revealed that within this 48%:
•EPC costs account for 92% of upfront costs
•Developer costs account for 8% of upfront costs
•The solar field (i.e. collector structure, mirrors, absorbers, hydraulic actuators and HTF piping) represents the largest proportion of CAPEX costs at 30%
Solar Tower
For a reference plant with a 100 MW capacity, 6 hours of TES and dry cooling located in the MENA region the CAPEX represented the largest portion of lifecycle costs, accounting for 49%.
The distribution of CAPEX costs revealed that within this 49%:
•EPC costs account for 91% of upfront costs
•Developer costs account for 9% of upfront costs
•The solar field (i.e. heliostats, the drives, the foundation, pedestal and support structure) represents the largest proportion of CAPEX costs at 24%
For more information about the CSP Today's Technology Reports, please visit: http://www.csptoday.com/csp-technology-report/index.php
Or contact:
Bea González
CSP Today
bea@csptoday.com
Featured Product
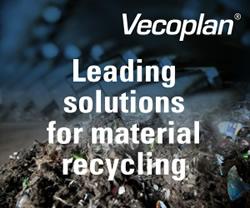
Vecoplan - Planning and implementation of complete processing plants in refuse derived fuel production
In order to reduce the costs involved in the energy-intensive production of cement, many manufacturers are turning to refuse-derived fuels (RDF), considerably reducing the proportion of expensive primary fuels they would normally use. Solid fuels are being increasingly used - these might be used tyres, waste wood or mixtures of plastics, paper, composite materials and textiles. Vecoplan provides operators of cement plants with proven and robust components for conveying the material and separating iron and impurities, efficient receiving stations, storage systems and, of course, efficient shredders for an output in various qualities.