Supply chain roadblocks problematic for Indian CSP
CSP Today explore the difficulties that the Indian CSP industry have faced in treading the fine line between reliance on foreign expertise and building a local manufacturing base, as solar power ramps up in the country.
Developing an indigenous supply chain for solar thermal power projects in India was a fundamental goal of the National Solar Mission (NSM), launched by the Indian Government in 2010. The aim, like in many regions where CSP technologies exist, is to achieve significant cost reductions through increased demand, economies of scale in production and improvements in component efficiencies. It was predicted that India would be able to make significant steps in achieving grid-parity for CSP through the use of local manpower and materials, all at lower costs than those seen in more established markets in Europe and the US.
Under Phase I of the NSM the domestic content requirement made it mandatory for projects to source 30% of their components from local sources, a target that has since been scrutinized by experts in the industry. The unconventional components used in CSP plants and the lack of experience in India to manufacture such components has led to a reliance on foreign manufactures, that has made this target unrealistic if low costs are to be maintained by developers.
The supply of important solar field and power block components has primarily come from Europe. Recent weeks have seen Siemens, General Electric and Areva announcing orders from Indian developers to supply turbines for Phase I projects. Godawari Power & Ispat, Megha Engineering, Reliance Power, Corporate Ispat Alloys and Lanco, all developing projects under the NSM, have placed these orders.
Although solar field components such as pumps and motors could be sourced from local manufacturers there has been little evidence to suggest that Phase I developers have placed these orders. Furthermore, the reliance on foreign EPC groups to undertake plant construction and design, has led to questions surrounding the tension between training local manpower in the long-term and finishing projects within the required time frame and budget.
To overcome the challenge of creating a local manufacturing base in India, CSP Today has announced this week that the World Bank, Cargo Power & Infrastructure, FAST and Lauren CCL will participate at the 3rd CSP Today India Summit 2012 (New Delhi, 14-15 March). The impact of Phase I on indigenisation and the steps that must be taken to ramp up future manufacturing in India will form a critical part of the discussion in New Delhi. In addition experts from Siemens, Areva and Thermosol Glass will outline the key supply chain challenges facing Indian CSP and the role they have played to lower costs and improve efficiencies for Phase I projects.
Other confirmed participants include the Ministry of New and Renewable Energy, Central Electricity Regulatory Commission, Solar Energy Centre, Torresol Energy, Abengoa, Godawari Power and Ispat, Siemens, Reliance power and many more leading CSP players.
The event is set to take place on 14-15 March in New Delhi, with over 350 delegates in attendance. For more details about the summit go to the website: www.csptoday.com/india
Or contact:
Jack Ahearne
CSP Today
jack@csptoday.com
Featured Product
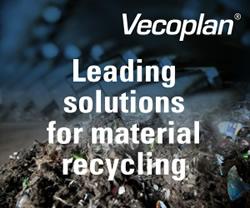