Uni-Solar Going Outer Space
AUBURN HILLS, MI, Aug. 11--United Solar Ovonic Corp., a subsidiary of Energy Conversion Devices, Inc., announced that the Air Force Research Laboratory (AFRL) at Kirtland AFB, New Mexico, awarded Uni-Solar a $6.7 million contract to develop its lightweight, high-efficiency solar cell technology...
AUBURN HILLS, MI, Aug. 11--United Solar Ovonic Corp., a wholly-owned subsidiary of Energy Conversion Devices, Inc., announced today that the Air Force ResearchLaboratory (AFRL) at Kirtland AFB, New Mexico, has awarded United Solar Ovonic a $6.7 million contract for developing its ultra-lightweight, high-efficiency solar cell technology for use in space and
Today's announcement builds upon the success of earlier contracts awarded by AFRL to United Solar Ovonic to develop its ultra-lightweight solar arrays to be used in space and airship vehicles. The Advanced Space Power Generation
Group in the Space Vehicles Directorate of AFRL will administer the contract.
"Our performance goals for the next generation solar arrays includelighter, more stowable and lower cost than those currently available," said
Dr. Donna Senft, Program Manager of the AFRL Advanced Power Generation Program at Kirtland AFB. "We are pleased with the performance of United Solar Ovonic's ultralight, high efficiency solar cell technology and the progress made to
date under AFRL contracts to address these goals."
UNI-SOLAR(R) space photovoltaic products offer an ultralight, low-cost alternative to conventional space PV modules made of crystalline silicon or
gallium arsenide. United Solar Ovonic's triple-junction modules, originally developed for terrestrial applications, are made of amorphous silicon-basedthin-film alloys, which are deposited on a 5-mil flexible stainless steel substrate. By utilizing a polymeric substrate rather than stainless steel, new space cells will be developed that have a specific power density greater
than 1,000 watts per kilogram (W/kg), which is significantly higher than what is currently available. A high specific power density is required for airship application. The radiation hardness and superior high-temperature
performance of amorphous silicon make it an attractive material for space application.
"This award provides us with yet another opportunity to continue our successful collaboration with the Air Force to develop our ultralight solar cells. This is a valuable technology that will be very beneficial to AFRL and to our nation's security," said Subhendu Guha, President and COO of United Solar Ovonic.
"We are delighted to have been awarded this contract by AFRL. We are opening up a new era of air and space solar energy solutions that are so critical to our nation's future," said Stanford R. Ovshinsky, Chairman and CEO of United Solar Ovonic and President and CTO of ECD Ovonics. "We recently broke ground for a second 25-megawatt module manufacturing facility in Auburn Hills, Michigan because of the growth in demand for our thin-film, triple-junction solar products for terrestrial applications worldwide--an importantstep in United Solar Ovonic achieving its goal of becoming a leader in this field."
About United Solar Ovonic
United Solar Ovonic, building on technology invented and pioneered by ECD Ovonics, is the world leader in thin-film amorphous photovoltaics. Its existing 25-megawatt production equipment is the world's largest and most advanced machine for the manufacture of thin-film amorphous silicon alloy solar cells and related products used for a variety of applications ranging from large solar farms for utility-scale applications to charging batteries
for solar lanterns. UNI-SOLAR(R) solar cells are lightweight, rugged and flexible, and are ideal as building-integrated photovoltaic roofing systems for residential and industrial customers. ECD Ovonics and United Solar Ovonic hold the basic patents covering the continuous roll-to-roll manufacturing of thin-film amorphous silicon alloy multi-junction solar cells and related
products.
Featured Product
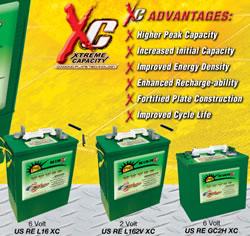