Siemens and Boson Energy enter agreement to accelerate the green energy transition through waste-to-hydrogen (to-X) technology
Siemens to provide consultancy and technology, including applications from its Siemens Xcelerator portfolio, spanning automation, digitalization, electrification, and instrumentation
Boson Energy and Siemens AG have signed a Memorandum of Understanding (MoU) to facilitate collaboration on technology that converts non-recyclable waste into clean energy. The collaboration aims to advance sustainable, local energy security, enabling hydrogen-powered electric vehicle charging infrastructure without compromising grid stability or impacting consumer prices.
"We are excited to join forces with Siemens in our ambition to make a difference in society and support global decarbonization with our Waste-to-X solution," said Jan Grimbrandt, CEO of Boson Energy. "Siemens, with its unique capabilities of people and technology, gives Boson Energy ‘unlimited' capacity to scale and reach markets from Berlin to Delhi and beyond - from day one."
Siemens offers technology for every step of sector coupling, from initial chemical processes to the final charging stations. Its portfolio covers all required products, solutions, and services in automation, electrification, and instrumentation. As a technology partner, Siemens will assist Boson Energy in building a blueprint to create a scalable and repeatable solution, by applying the latest technology within digital services and software for optimization, standardization, and simulation during both the manufacturing and operational phases.
"We look forward to supporting Boson Energy with our portfolio to contribute to a more sustainable circular economy," said Axel Lorenz, CEO of Process Automation at Siemens Digital Industries. "Digitalization and automation are crucial for building and scaling production capacities - even more so for complex processes such as thermochemical recycling."
Combating climate change is one of the biggest challenges of our time. Addressing the challenge, Boson Energy contributes toward decarbonization with its distributed production of local energy and chemicals - turning non-recyclable waste into a sustainable hydrogen that is cost-competitive to fossil fuels at point of use. It does this by integrating its Hydrogen by Plasma Assisted Gasification (HPAG) technology into an ‘energy hub' solution that realizes the important circular hydrogen potential of waste in a uniquely sustainable way. The hydrogen produced can support off-grid applications such as fast charging and facilitates more reliable grid operations.
"The collaboration with Boson Energy represents a significant step forward in our commitment to advancing technologies toward CO2 reduction," said Stephan May, CEO of Electrification and Automation at Siemens Smart Infrastructure. "By leveraging the breadth of our comprehensive portfolio, we aim to create a scalable and efficient model for converting waste into clean hydrogen. This collaboration not only addresses the urgent need for local energy security but also contributes to reducing the global carbon footprint, paving the way for a more sustainable future."
Boson Energy is targeting more than 300 plants in order to produce 1 million tons of circular hydrogen from waste by 2030 - avoiding up to 30 million tons of CO2 emissions per year. Starting in Sweden, Poland, and Germany, then continuing throughout Europe, Boson Energy is aiming for a global presence.
The Memorandum of Understanding was signed during the ACHEMA Fair in Frankfurt by Axel Lorenz, CEO for Process Automation, and in advance by Stephan May, CEO for Electrification and Automation at Siemens.
Featured Product
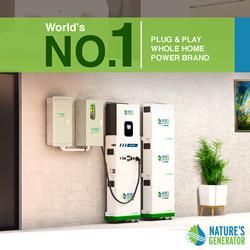