Electrical power delivery systems are usually the most impactful on plant operation. The cost of failure of certain pieces of equipment can quickly escalate into multi-millions of dollars of equipment replacement costs and production downtime.
Monitoring Tools for Manufacturing Plant Maintenance
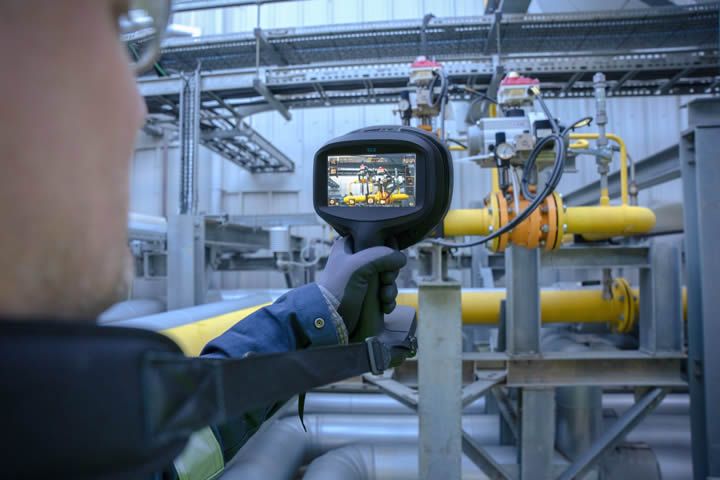
Q&A with Rob Milner, Director of Business Development for Condition Monitoring | Teledyne FLIR
Tell us about yourself and your role with FLIR.
I'm in my 23rd year at FLIR, where I've worked in business development and sales roles across multiple industrial verticals, including portable condition monitoring tools, automation, optical gas imaging, and small unmanned aircraft systems. As a Director of Global Business Development, I provide customer insights that help our product management teams design more effective solutions.
One of the most rewarding parts of my job is the frequent interaction with customers. I regularly meet with them to understand their challenges and recommend solutions that help improve their operations. It's been an honor to work at FLIR all these years, helping customers advance their business processes and overcome technical challenges.
What are some of the primary challenges that manufacturing teams face today regarding equipment maintenance and operational performance?
Maintenance team resources have always been constrained by budget, but more and more, the biggest issue is the lack of experienced people. Manufacturers get caught in a catch-22, reacting to equipment failures instead of getting ahead of the cycle through predictive maintenance techniques and usage-based preventative maintenance plans. Money spent on proactive maintenance techniques has been proven time and again to deliver many multiples in savings.
Companies also struggle with scaling best practices across the organization. Plants often use different equipment, have different training procedures, handle data differently and have different interpretations of data. The end result of fragmented workflow is reliability improvements, and by extension return on investment, is not maximized.
Another significant challenge is the lack of real-time visibility into equipment performance. Outdated systems or disconnected tools make it difficult to monitor critical metrics, leading to inefficiencies and missed opportunities for improvement. Additionally, variability in operator expertise and adherence to maintenance protocols can limit equipment longevity and performance over time.
The key is finding the right balance for your specific operation. From my experience, success comes from combining the right tools with proper training and a clear strategy.
How do modern monitoring tools help address issues like unplanned downtime, equipment failures, and quality control in manufacturing?
Manufacturing managers have various specialized tools available depending on the equipment housed in a manufacturing plant and the issues they are trying to solve. Condition monitoring and preventative maintenance equipment are among the top tool categories that are essential for maximizing plant productivity and quality.
Among these tools, thermal imaging cameras are critical to seeing heat-related issues in electrical systems, insulation, and mechanical systems such as pumps and motors. Additionally, acoustic imaging devices locate mechanical issues and air and gas leaks via the high-frequency sounds that denote friction or leaks. These tools enable professionals to intervene to repair or replace equipment before minor matters grow to become major problems that result in unplanned downtime or even catastrophic failure.
Electrical power delivery systems are usually the most impactful on plant operation. The cost of failure of certain pieces of equipment can quickly escalate into multi-millions of dollars of equipment replacement costs and production downtime, not to mention the potential impact on the health of plant workers. This impact is so great that proactive inspection using thermography has now been incorporated into the USA National Electrical Code, making it mandatory to inspect all electrical systems at least annually under the NFPA 70B code component.
Thermography sees the relative temperature differences between electrical components that form because of loose or dirty connections, crimped conductors, power imbalances, inductive heating and more. Using thermography software tools such as trending and load factor correction, maintenance professionals can detect failing equipment and intervene. Maintenance costs are a tiny fraction of what they would be to repair or replace failed units.
Acoustic imaging detects ultrasonic noise or noise above the range of frequencies people can hear, created by compressed air and gas leaks, vacuum leaks, and mechanical issues. The cost from compressed air lost to leaks can be 2-3% of a manufacturer's total electricity usage, a significant cost in anyone's books. Vacuum leaks can result in poor or inconsistent product quality and compressed gas leaks create higher ongoing material input costs and sometimes health and safety issues.
Additionally, acoustic imaging detects partial discharge issues like arcing in higher voltage electrical equipment. NFPA 70B also requires regular inspection for partial discharge for many systems 600 Volts and above.
Using fixed-mount, permanent sensors that monitor specific spots or areas of machinery, maintenance teams can continually track critical metrics like temperature and pressure in real time, detecting early signs of equipment issues.
Combining the data generated by these tools and software provides a proactive strategy to address potential failures before they occur, improving equipment reliability, reducing downtime, and extending asset lifespan.
In your experience, what are the most critical factors to consider when selecting monitoring tools for manufacturing environments?
Determining a company's ability to address specific operational needs and application challenges is essential. In many cases, a lack of experienced inspection technicians, such as thermographers, leads companies to reduce inspections and backslide into reactive maintenance, leading to a vicious cycle of reduced productivity. Therefore, it is critical to create an inspection plan that solves for, or at least mitigates, this deficit.
Periodic inspection using fully autonomous robots and drones will undoubtedly be a viable option at some point, but for now, we are at the bleeding edge of this kind of technology deployment.
Fixed, permanent monitoring systems are highly capable and can help with the inspector deficit, but they are capital-intensive and make sense only for the most critical of equipment.
Companies can realize a huge impact on reliability through the effective deployment of tools and software that leverage experienced technicians' scarce time. One simple example is using infrared ports and windows to enable faster inspection of electrical equipment. This technique can reduce the time needed for this kind of inspection by as much as 87%, which is time back to be used for further cost-lowering activities.
Imaging and AI-enabled inspection tools provide another way to address the experience gap. Acoustic imaging and thermography can reduce single-spot tool inspection time by 50-90%, especially when decision-support AI analysis is embedded in the tool to help technicians understand issues and corrective actions.
However, effective use of route-based inspection tools is where I see the biggest immediate impact being made to solve for the inspector experience deficit. Using this process, an experienced technician can assess assets for a team of many entry-level inspectors. Tools are available to guide new inspectors from place to place and to capture consistent data and imagery over time or even among different inspectors. These tools make the experienced inspector 10 to 20 times more productive than performing each inspection themselves. To reap this benefit, however, companies must invest upfront in program setup costs.
What concerns or limitations do manufacturers commonly encounter when implementing real-time monitoring systems across their operations?
In addition to the lack of experienced inspectors, infrastructure limitations are often a big hurdle, particularly in manufacturing facilities with older equipment and machinery. Manufacturing plants commonly operate multiple generations of equipment with different control systems. Getting these diverse systems to communicate effectively with a centralized monitoring platform frequently requires additional hardware and custom programming solutions.
Luckily, sensors and software are increasingly available to deploy wirelessly, making it easy to retrofit permanent or semi-permanent monitoring systems on legacy assets. Additionally, these systems increasingly communicate through common modern industrial protocols like REST and MQTT, making capturing data from multiple sensor modalities into a single asset health dashboard easy.
Finally, resource allocation often proves challenging. While real-time monitoring can prove cost-effective on certain critical assets, organizations must consider the initial investment required in equipment and expertise and the ongoing maintenance of the monitoring systems themselves. Success depends on having adequately trained personnel to manage these systems effectively.
When is it better to choose continuous, real-time monitoring tools versus choosing a handheld or tool?
Critical failure risk is the primary consideration for facilities when choosing whether to integrate real-time monitoring or acquire and use a handheld tool, such as thermal or acoustic imaging devices. When equipment failure can result in catastrophic loss, safety hazards, productivity losses, or environmental incidents, those typically justify continuous monitoring. For example, pumps, compressors, and critical electrical power delivery systems operating at high engineering load design fraction benefit from 24/7 surveillance that can trigger immediate alerts when temperatures or vibration characteristics change beyond the normal operation range. This is a critical step to maintaining uptime.
Asset accessibility is also a critical factor in choosing equipment. Permanent monitoring solutions are often the better choice in hard-to-reach areas, such as components in high locations or hazardous areas. Also, automated monitoring can benefit facilities that must perform regular manual inspections requiring production shutdowns or elaborate safety procedures depending on the facility.
Handheld tools remain valuable for routine inspections for the majority of equipment that isn't as critical or cost effective, and for troubleshooting of systems and building envelope. The most effective programs typically employ both approaches strategically, continuously monitoring critical assets while maintaining handheld tools for flexibility and post-fix verification.
In what ways can monitoring technology contribute to a safer, more sustainable manufacturing environment, and what obstacles need to be addressed to fully realize these benefits?
Implementing monitoring processes across facilities offers significant potential for safety and sustainability improvements. Regarding safety, continuous monitoring enables early detection of potential hazards before they become critical. These are potentially dangerous situations for employees, and by identifying these issues early, facilities can prevent accidents and protect personnel.
From a sustainability perspective, real-time monitoring or handheld equipment identifies inefficiencies, so they help optimize energy usage, eliminate waste, and reduce costs. For instance, acoustic imaging helps detect compressed air leaks—a significant source of energy waste in manufacturing. Early detection of equipment deterioration extends asset life cycles, reducing resource consumption and waste from premature replacements.
Success requires a systematic approach: start with critical systems, build internal expertise, and gradually expand monitoring coverage as benefits are realized.
Rob Milner’s 23-year history with FLIR has resulted in an understanding of customer needs in the fields of asset reliability, research, leak detection and more. He is Director of Business Development for Condition Monitoring at Teledyne FLIR, which allows him to apply his curiosity and desire to do things better to learn what FLIR’s customers need and to support FLIR’s product managers, sales and marketing groups to bring the results to market.
The content & opinions in this article are the author’s and do not necessarily represent the views of AltEnergyMag
Comments (0)
This post does not have any comments. Be the first to leave a comment below.
Featured Product
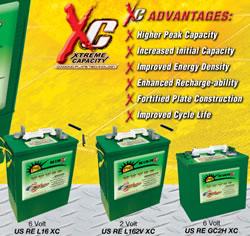