It is critical to detect leaks not visible to the naked eye that, if disregarded, could cause the EV battery to fail, limiting battery performance with diminished capacity and longevity, as well as jeopardize vehicle safety.
Leak Testing is Mission-Critical for EV Drive Batteries
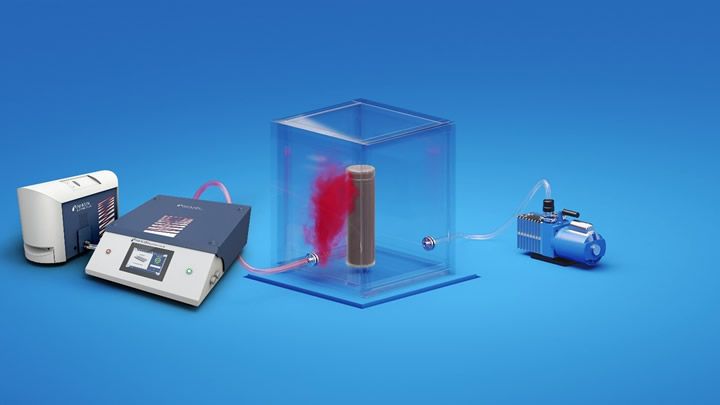
Thomas Parker, North American automotive market sales manager | INFICON
The eMobility industry is moving quickly to develop electric vehicle (EV) powertrain solutions designed to deliver consistent levels of vehicle performance, power density and battery life. A major challenge is to convince consumers to make the switch to driving EVs rather than a familiar internal combustion engine (ICE) vehicle. In the race to the EV future, where speed-to-market can define the winners and losers, many manufacturers are skipping an important step in testing to ensure lithium-ion EV traction batteries function optimally: Leak tightness testing. It is critical to detect leaks not visible to the naked eye that, if disregarded, could cause the EV battery to fail, limiting battery performance with diminished capacity and longevity, as well as jeopardize vehicle safety.
Leak testing vehicle powertrain systems is not a new concept. It’s been applied for decades in testing ICEs to ensure product quality so that the engine system functions properly and safely with the specified pressures and without cross contamination of engine fluids. For EV traction battery systems, the tests are different and more specialized because a number of components must be tested for minuscule leaks. However, the principle remains the same: Leak tightness testing is critical to ensure optimal performance of a vehicle powertrain system.
As the foundation for optimal EV battery performance, capacity, longevity and safety, leak tightness testing does not possess the dramatic intrigue of flashier vehicle technologies that consumers can touch and experience first-hand. However, a system is only as strong as its foundation; the nondescript workhorse providing the stability required for a product to function at a high level. Similarly, leak tightness testing is only seen at the production level on the factory floor. However, the results provide the foundation for the EV battery system to work at optimal levels, thus positively impacting battery power, capacity, longevity and safety. That’s why leak tightness testing is mission-critical to ensure the high-quality performance of the EV powertrain system.
Leak testing and EURO 7
Another consideration for leak tightness testing is the proposed new EURO 7 standard, which is nearing release, and will impact U.S. automakers that manufacture vehicles for the European market. For EV traction battery performance, EURO 7 requirements for passenger cars specify that, after five years or 100,000 kilometers, EV batteries must provide 80% of their original capacity; after eight years or 160 kilometers, 72%. Values of 75% and 67%, respectively, will apply to vans. Each vehicle will receive an “Environmental Vehicle Passport” that contains its specific information about battery health and performance. These proposed EURO 7 requirements can be achieved, long-term, through proactive leak testing during the assembly of lithium-ion battery cells and battery packs.
For leak testing to be adopted as a vital step in EV traction battery production, it needs to perform at the speed of production to maintain high levels of throughput while meeting stringent quality standards.
Battery components and failure modes
There are three main components of lithium-ion EV traction batteries — battery cells, cooling plates and the battery pack housing consisting of a battery tray and lid. During battery operations, these systems have cyclic and continuous high charge and discharge rates. These intense, harsh cycles produce constant high levels of stress on EV battery systems, which only strengthens the position for incorporating leak testing in all phases of EV battery production.
Likewise, three failure modes can be tied back to very small leaks within the main EV battery system components: Diminished operating capacity, shortened battery lifespan and fires. For the cooling circuits in the battery’s thermal management system, leak detection is conducted to identify the escape of the cooling medium (water-glycol) into the battery pack, where it can short-circuit high-voltage power electronics systems.
Leak testing at all stages of the production process.
To achieve the highest-quality results, a best practice is to conduct leak tightness testing at all stages in EV battery manufacturing: During cell production, during pack component production and again during battery pack assembly with leak detection solutions specifically designed for each manufacturing stage. When battery cells with rigid casings are produced — prismatic, cylindrical or coin — they need to be tested twice with a non-destructive method; once, before filling with electrolyte, and a second time after they’ve been sealed. The exception is pouch cells, which typically are not pretested because, due to their flexible nature and the fact that these can only be sealed on all four sides after filling. This makes leak testing pouch cells filled with electrolyte and sealed more critical.
For rigid-case cells, the first test is typically done in a vacuum chamber with helium as a tracer gas. The second test is conducted via direct electrolyte leak detection where escaping electrolyte solvent is detected in a test chamber.
The leak testing imperative
In a lithium-ion EV battery, every joining system — welds, seams, gaskets, etc. — presents an opportunity for a leak that escapes detection with the naked eye. These leaks create a pathway for medium to escape the cell or pack, or enter the cell or pack, which both can have negative effects on battery performance and longevity, as well as vehicle safety.
For the battery cell, it’s critical to perform non-destructive leak tightness testing to evaluate electrolyte levels, as well as liquid water or water vapor ingress in the form of air humidity. When water mixes with the electrolyte, hydrofluoric acid is created, which is inflammable and also attacks the components of the battery, resulting in decreased lifespan. For the battery pack, leak testing is conducted to identify escape of the cooling medium (glycol-water mixture) into the battery pack and to ensure that battery packs do not allow for any water ingress from the outside. In both cases, the liquid can short-circuit high-voltage power electronics systems. Loss of cooling medium also contributes to diminished capacity for the EV battery pack.
EV battery packs and exposure to water
In most passenger EVs, including pick-up trucks and SUVs, the battery pack is designed to fit on a platform underneath the passenger compartment in a skateboard design. At the size of a queen-sized mattress, the EV battery pack can leak in several hundred places, which can be exacerbated during typical vehicle operating conditions in which the battery pack is exposed to water.
Positioned on the underside of the chassis, EV battery packs are susceptible to water ingress with a splash during rainstorms, when driving through puddles or when completely submerged in water for about 20 minutes at a boat launch. Therefore, it’s critical for the battery pack to meet a high standard of leak tightness so that, despite any type of exposure to water, the electrical system will be fully functional and not prone to short-circuiting.
In battery pack production, first the trays and lids for the battery pack housing are leak tested in a vacuum chamber using a tracer gas. After assembly of the battery pack, the preferred testing method is with a robotic (or manual) sniffer device using a tracer gas.
Given the large size of the battery pack, leak testing is most effectively conducted with a sniffing tool — manual or robotic — using a tracer gas and a highly sensitive tracer gas sniffer leak detector. Helium or forming gas (an inflammable mixture of 5% hydrogen in 95% nitrogen) can be used as tracer gas.
During the test, the battery pack housing is filled with the tracer gas. As the sniffer tool moves across the battery pack, it will detect a leak outlet channel via the escaping tracer gas. This test method produces highly accurate, repeatable and reliable measurements, and can detect very small leaks, for example, in the 10-4…10-6 mbar I/s range.
Leak testing for lithium-ion battery cells
Leak testing at different stages during battery cell production.
Leak testing lithium-ion battery cells is critical to prevent water vapor, or humidity, from entering the cell. If water vapor mixes with the electrolyte, hydrofluoric acid is created, which is inflammable and also attacks the components of the battery cell.
Using a vacuum chamber leak testing system specifically designed for integration into production lines, the battery cell housing is placed within the chamber and filled with helium. During pump-down, or evacuation of the test chamber, any escaping helium can be detected as the test gas migrates into the vacuum chamber. Highly sensitive vacuum leak detectors capture the measurement information on leak size.
Next, when a proven leak-tight cell is filled with electrolyte and sealed, it’s crucial to test the leak tightness again. Filled and sealed cells are placed in a vacuum chamber again and electrolyte escaping from leaky cells will be detected by specialized battery leak detectors using the direct electrolyte leak detection method.
Method: Direct electrolyte leak detection of battery cells.
When equipped with a multi-chamber design, these leak-detection systems operate in near-constant measuring mode to optimize production for maximum throughput while meeting rigid quality standards. They also can be optimized for a batch-testing approach, which generates a high-speed and time-saving in-line testing process while meeting the highest quality standards and achieving high throughput to detect leaks in seconds.
These systems can be used to test the smallest leaks in lithium-ion battery cells in the micrometer range with the resulting helium equivalent leak rate as low as 5.10-7 mbar.I/s, which represents a diameter in the range of 1-5 micrometers for common battery designs.
Cooling circuits and leak detection
The cooling circuit in EV thermal management systems is an essential component that regulates the temperature to prevent overheating, which would damage the battery pack and cells, compromising performance and lifecycle, as well as vehicle safety. The cooling circuit is also used to bring the battery pack to operating temperature quickly in cold weather to avoid degradation of the battery cells and pack due to low temperatures.
Cooling circuits are filled with a mix of water-glycol, which possesses the chemical properties to manage the operating temperature. Leak tightness testing is conducted here to prevent loss of medium, in this case, the water-glycol medium, which would compromise the function of the cooling circuit and, by extension, the entire battery pack. As previously mentioned, the cooling circuit is surrounded by high-voltage power electronics. Any escaping medium could immediately short-circuit the battery pack, which has the potential to present a multi-layered hazard.
A best practice for leak tightness testing of a cooling circuit is to use a rejection leak rate in the range of 10-4 mbar I/s. For the assembled cooling circuit, the leak test is best achieved with a highly sensitive, high-flow robotic sniffer leak detector. In addition, a (robotic) sniffer is applied for the leak detection of connections for the cooling plates and the lines that connect them.
Speed of leak testing and speed-to-market
While leak testing is another step in the manufacturing process, there are leak testing systems designed for each phase of production, and for each component of a lithium-ion EV traction battery, that actually create efficiencies. For example, for all formats of lithium-ion and sodium-ion battery cells, specialized leak testing systems designed for mass production of EV battery cells add seconds to cell production because they are designed to have high throughput. They also contain costs because a defective cell or pack is identified and pulled from partial assembly, which saves the time and resources of taking a defective battery cell to final production only to have it rejected there.
The eMobility industry will continue to move fast to deliver the latest in EV powertrain technology, and it can do it without missing a step using high throughput leak tightness testing systems to establish the solid foundation lithium-ion EV traction batteries need to power on.
To learn more about the leak testing imperative, click here:
E-mobility: Leak Testing for Electric and Fuel Cell Vehicles
Thomas Parker is responsible for INFICON’s automotive sales in North America, supporting the company’s growing focus and investment in the automotive market. Parker previously had been the company’s leak detection segment manager for the eastern United States. He joined INFICON in 2006 as a key account manager in Atlanta. Prior to that, he served as a technical sales representative at W.L. Schoonover Inc. in Canton, Georgia. Parker holds a degree in engineering from Southern Polytechnic State University in Marietta, Georgia and an MBA from Syracuse.
The content & opinions in this article are the author’s and do not necessarily represent the views of AltEnergyMag
Comments (0)
This post does not have any comments. Be the first to leave a comment below.
Featured Product
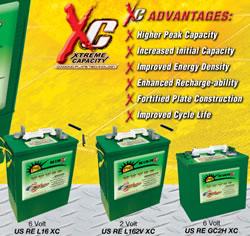