This article explores how advanced inspection systems are pivotal in driving these sustainable practices by enhancing manufacturing precision, reducing waste, and ultimately leading to more environmentally friendly production processes.
Greening the Automotive Industry: Sustainable Practices in EV Battery Manufacturing
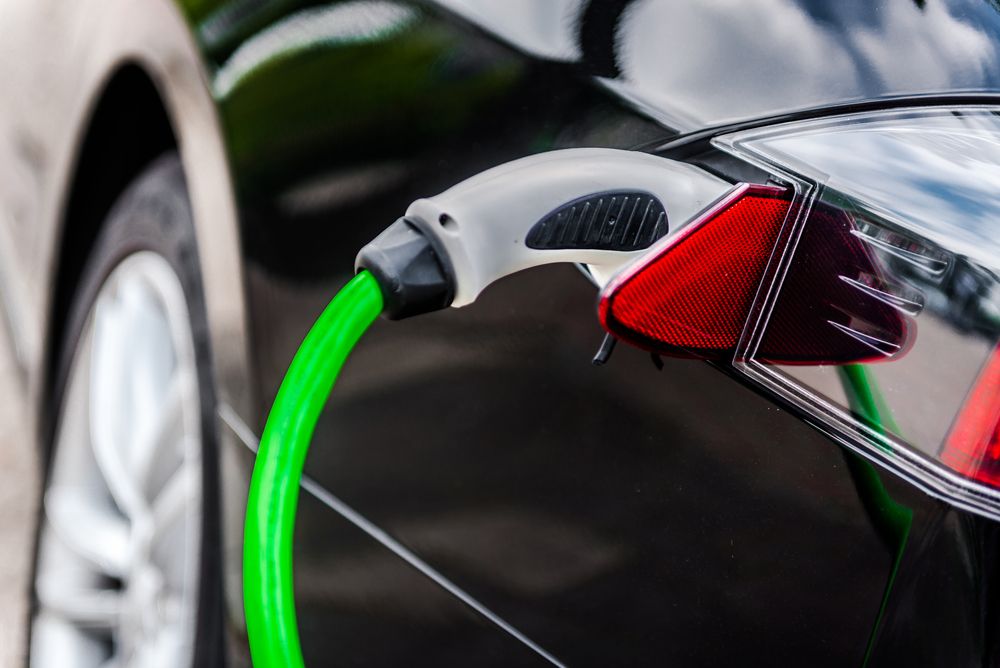
Article from | KEYENCE
The automotive industry has long been scrutinized for its environmental impact, predominantly due to its substantial carbon emissions and resource-intensive manufacturing processes. With the global conscience swinging towards sustainability, the industry is under pressure to reduce its ecological footprint.
This has created a strong momentum toward electric vehicles, or EVs. Their zero tailpipe emissions present a promising pathway to reduce the environmental impact of personal transport. However, the sustainability of EVs is also about how their critical components, especially batteries, are manufactured. Emphasis on green practices in EV battery production can help mitigate environmental damages and align with broader goals for resource efficiency and ecological conservation.
This article explores how advanced inspection systems are pivotal in driving these sustainable practices by enhancing manufacturing precision, reducing waste, and ultimately leading to more environmentally friendly production processes.
Importance of sustainable practices in EV battery manufacturing
In electric vehicle battery manufacturing, implementing sustainable practices is not just an environmental necessity but also a strategic imperative. Inspection systems are critical tools in this endeavor, ensuring that the production processes not only adhere to quality standards but also align with sustainability goals.
Inspection systems are sophisticated technologies used to assess the quality and integrity of materials and products during the manufacturing process. These systems perform vital functions such as detecting defects, ensuring compliance with specifications, and verifying product uniformity and performance. By doing so, they help reduce waste, prevent costly rework, and enhance overall manufacturing efficiency.
Laser profilers, a type of inspection system, are instrumental in advancing sustainable manufacturing practices. These devices use laser displacement sensors to capture precise 2D/3D measurements across surfaces. The data collected by high-precision 2D/3D laser profilers, such as height differences, widths, and angles, allow for detailed analysis of components, ensuring that they meet strict quality standards without excess material use or energy consumption. By minimizing the production of defective parts, laser profilers significantly reduce scrap and associated costs, contributing to a leaner and more eco-friendly production process.
In addition to laser profilers, several other inspection technologies play pivotal roles in enhancing the sustainability of EV battery production:
-
X-ray Technology: This technology is crucial for detecting internal defects in battery cells that might not be visible externally. By identifying flaws early in the manufacturing process, X-ray inspection helps prevent the advancement of defective batteries into the market, thereby avoiding potential waste and safety issues.
-
Ultrasonic Testing (UT): UT uses high-frequency sound waves to examine the uniformity of materials. It is particularly effective in detecting inconsistencies within the battery cells, such as delaminations or impurities, ensuring that only the highest quality products proceed through the production line.
-
Infrared Thermography: This method monitors and manages the thermal properties of battery components during manufacturing. Infrared cameras detect heat patterns and variations, indicating potential faults in thermal management. Proper thermal management is crucial for the longevity and efficiency of EV batteries, reducing energy waste and improving safety.
Benefits of Using Inspection Systems in EV Battery Manufacturing
The adoption of inspection systems in electric vehicle battery manufacturing brings substantial benefits that go beyond compliance with quality standards. These systems are crucial for enhancing sustainability through several key advantages:
Reduction of Scrap and Waste Materials
One of the primary benefits of implementing inspection systems like laser profilers, X-ray technology, and ultrasonic testing in EV battery manufacturing is the significant reduction in scrap and waste. These technologies enable precise detection of any anomalies or defects early in production. By identifying defects before batteries leave the production line, manufacturers can avoid the costly and resource-intensive process of reworking or disposing of defective products. This saves on raw materials and minimizes the waste generated, contributing to more sustainable manufacturing practices.
Improved Quality Control and Product Consistency
Inspection systems ensure that each battery produced meets the same high quality and performance standards. This is critical in the automotive industry, where consistency and reliability are paramount. Technologies like infrared thermography help monitor and manage the thermal properties of battery components during manufacturing, ensuring that each unit performs safely and effectively under varying conditions. This level of quality control is essential for maintaining consumer trust and reducing the likelihood of costly recalls or safety issues.
Cost Savings Through Early Detection of Defects
The early detection of defects is another significant advantage offered by inspection systems. By catching flaws early in the manufacturing process, these systems help avoid the downstream costs associated with failed components or customer dissatisfaction. This proactive approach to quality assurance reduces the need for expensive fixes and warranty services after the product has been delivered, leading to considerable cost savings.
Reduced Environmental Impact by Minimizing Resources Used
Inspection systems contribute to environmental sustainability by ensuring manufacturing processes use resources as efficiently as possible. By reducing the amount of scrap and improving the consistency of battery production, these systems decrease the quantity of raw materials needed and lower the energy consumption per unit produced. Furthermore, improved product quality and longevity mean fewer resources are needed over the product's lifecycle, which includes fewer replacements and repairs.
Integrating Sustainable Practices in EV Battery Manufacturing through Inspection Systems
Integrating sustainable practices into electric vehicle battery manufacturing is essential for reducing the environmental footprint of this booming industry. Advanced inspection systems play a pivotal role in this integration by enhancing efficiency and sustainability across various aspects of production.
Utilizing Renewable Energy Sources for Powering Inspection Systems
One effective method to enhance sustainability is by powering inspection systems with renewable energy sources such as solar or wind power. This shift reduces the carbon footprint of manufacturing operations and aligns with global efforts to decrease reliance on fossil fuels. Renewable energy sources provide a cleaner, more sustainable way to operate advanced technological systems used in battery manufacturing, further greening the process.
Implementing Recycling and Reuse Practices for Inspection System Components
Recycling and reusing components of inspection systems also contribute significantly to sustainability. By designing inspection equipment with modularity and reparability in mind, manufacturers can extend the lifespan of these devices. Additionally, implementing programs to recycle old or unusable parts minimizes waste and reduces the need for raw materials, which often have a high environmental extraction cost.
Collaborating with Suppliers to Ensure Sustainable Sourcing of Materials
Collaboration with suppliers to source sustainably produced materials for both batteries and inspection systems is crucial. This includes prioritizing suppliers who adhere to responsible sourcing and manufacturing practices, thus extending the commitment to sustainability throughout the supply chain.
Training and Educating Employees on the Importance of Sustainability in Manufacturing Processes
Finally, educating and training employees about the importance of sustainability practices is vital. By fostering a culture that prioritizes eco-friendly practices, employees become more likely to engage in and support sustainable operations. This educational approach ensures that sustainability becomes a core aspect of the manufacturing process, rather than an afterthought.
Through these initiatives, EV battery manufacturers can significantly enhance their sustainability profile while still achieving the high standards of quality and efficiency required in this competitive market.
Future Outlook: Advancements in Sustainable Practices for EV Battery Manufacturing
Future EV battery manufacturing endeavors are poised for profound improvements in sustainability through innovation and collaboration efforts across sectors. Thanks to the continuous work of manufacturers and researchers on sustainable battery materials, there’s the potential to stride towards decreasing environmental impact. This includes sourcing elements that are less toxic and more abundant, as well as creating batteries that are easier to recycle, thus reducing dependence on rare and expensive minerals.
AI and Machine Learning
With artificial intelligence (AI) and machine learning (ML), inspection systems in battery manufacturing will be transformed. These technologies enable more efficient quality control that will help reduce waste and speed up production without compromising accuracy. By predicting potential issues before they arise, AI and ML can lead to smarter, more sustainable manufacturing processes.
Recycling
Closed-loop recycling is also crucial to sustainability in EV battery manufacturing. These systems ensure that battery materials are reused at the end of their life cycle. This helps drastically reduce waste and the need for new raw materials, which eases the environmental footprint.
Collaborative Relationships
Lastly, collaboration among manufacturers, government agencies, and consumers is important for developing a circular economy for EV batteries. This effort creates regulations and incentives that promote recycling, reusing, and the continued use of battery materials for a much more sustainable and efficient resource cycle.
These advancements represent a comprehensive approach to reducing the environmental footprint of EV battery manufacturing and highlight the industry's commitment to promoting innovation and sustainability.
The content & opinions in this article are the author’s and do not necessarily represent the views of AltEnergyMag
Comments (0)
This post does not have any comments. Be the first to leave a comment below.
Featured Product
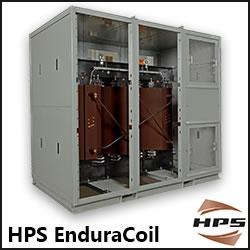