Power Panel’s Gen 20 Thermal Storage Tank scraps the concept of the traditional steel tank, replacing it with durable, safe, stable and recyclable thermoplastics. The result is a lightweight, secure, and rapidly-deployable thermal storage solution.
Changing the Rules of Thermal Energy Storage
Case Study from | Power Panel
Left: Power Panel GEN20 Integrated PV/Thermal hybrid systems with the company’s innovative Gen20 Thermal Storage Tanks for hot water.
The surge in interest for storage alternatives beyond electro-chemical batteries—for reasons including efficiencies, longevity and recyclability-- is raising the temperature on thermal technology as a means to store energy from PV and other sources.
Solar system designers and installers have long used hot water heating in tanks as a “diversionary load” to store excess PV-generated electricity. But such schemes required the installation of complex and costly plumbing infrastructure, between dedicated tanks and circulation systems. Newer thermal storage methods being discussed include so-called “T-Bat” thermal batteries using molten aluminum or alloys, hot silicon, and thermo-chemical decomposition. But these either remain mainly in the concept or early adoption stages, or face challenges in implementation based on the state of present technology.
One company is taking a different approach: that of combining simple, safe, and easy to manage hot water with advanced thermoplastic technology and architecture—eliminating both the issues with old-fashioned steel tanks and the inherent risks of the newer exotic, inorganic thermal storage schemes. Power Panel’s Gen 20 Thermal Storage Tank scraps the concept of the traditional steel tank, replacing it with durable, safe, stable and recyclable thermoplastics. The result is a lightweight, secure, and rapidly-deployable thermal storage solution that can be set up in minutes and lasts for decades.
The innovative Power Panel approach is based on replacing steel, glass and other materials with Expanded Polypropylene Foam (EPP). A molded material, EPP has a fraction of the weight of traditional materials , yet has up to twice the insulation capability at as little as 1/5th the energy storage cost of conventional tank materials and up to twice the insulation capability—in fact, a Gen 20 Tank loses just a little over 2°C of heat over a 24 hour period. It also has superior impact and chemical resistance compared to other designs.
Left: inside Power Panel’s Gen 20 Tank system. All the pieces fit onto a standard pallet easily handled by two people
Below: the sectional assembly process
The patented Power Panel Gen 20 Tank is modular for extremely easy transportation and rapid assembly on-site. A standard shipping container can accommodate over 50 of the tanks for rapid deployment anywhere where needed. Since both the exterior and interior liner are made from non-degrading engineered foam and plastics, the tank can be installed indoors or outdoors, or even buried at grade.
A uniquely innovative feature is the Tank’s configuration for assembly. It comes self-palletized and consists of an outer “hoop” and cover, into which the EPP foam sections are inserted along with a thermo-plastic liner. All the pieces needed fit on the footprint of a standard pallet, making it easy to move the Tank into a building or up onto a rooftop— in fact individual pieces can fit through a very small entrance, and the heaviest of them is just 10 pounds.
The entire tank assembly’s total weight just a little over 100 pounds, meaning that two people can easily unload and manage one under any field conditions. And, they can set one up in a matter of minutes.
On that last statement, the Tank’s inventor Garth Schultz likes to note that “people in marketing always claim that something takes just ‘minutes’ without actually disclosing just how many minutes that is. But in the case of our Gen 20 Tank we’re being transparent: it takes two people all of 5-10 minutes—tops-- to set one up. To say our design saves valuable installation time is the understatement of the decade.”
Schultz also points out other advantages to Power Panel’s unique storage topology. “You can ‘cascade’ multiple Tanks together using our connecting hardware to expand a system. Since the Tanks aren’t pressurized no pressure vessel certification is required. Our system can take full advantage of the various tax and other credits out there. We also have a range of upgrades available, including heat exchangers and water-purification systems for medical and other field uses.”
The adaptable materials that form the Power Panel Tank structure cover the range of thermal applications, enabling either hot or cold storage from 200 F to as low as -25 F. Flexible options include customizing liners for different fluid use, depending on the need. The applications for Power Panel’s thermal storage and complete PV/thermal systems range from disaster relief operations to institutional and hospitality facilities—anywhere hot or cold pure water is essential to human health and well-being. For more information contact info@PowerPanel.com
Above: a Power Panel Gen 20 Tank and integrated PV/Thermal array (also from Power Panel and a patented design), on a hotel rooftop in St. Thomas, US Virgin Islands. Such a system can produce over 15kW of combined PV/thermal energy, and provide enough hot water for the average-sized hospitality facility at a fraction of the cost of typical heating systems
The content & opinions in this article are the author’s and do not necessarily represent the views of AltEnergyMag
Comments (0)
This post does not have any comments. Be the first to leave a comment below.
Featured Product
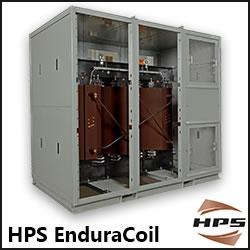