Asset owners increasingly are seeking longer design lives for their solar power plants. While 25 years was the accepted standard for the last two decades, power plant life spans now are being pushed out to three or four decades.
Digging Deep to Preserve the Longevity of Solar
Benjamin Share – Senior Project Engineer | Terrasmart
Owners who can prove longer asset lifetimes to lenders often can refinance to improve project economics and generate higher rates of returns.
Terrasmart engineers work alongside developers, EPCs, and system owners to understand and manage the complex factors that underpin system design life, ensuring that projects can be certified solid for up to 40 years. Understanding and managing corrosion of solar racking systems has become a critical factor when ensuring this long-term reliability. As the industry pushes design life to new heights, Terrasmart‘s deep expertise in managing corrosion keeps us ahead of the curve.
So, what exactly is corrosion?
We all understand how rust eats away at metal and threatens its structural integrity. But what exactly is corrosion — or, more specifically, galvanic corrosion? This electrochemical process, often seen at welds, occurs when two or more different types of metal are brought into physical contact in the presence of moisture, particularly salt water or acid rain. This creates an electrochemical cell, which leads to galvanic corrosion in one of the metals. While each metal might corrode by itself, galvanic coupling speeds corrosion in one while decelerating — or even stopping — corrosion in the other. This phenomenon can be used to protect structural steel members, at the expense of sacrificial materials like zinc or magnesium.
Terrasmart uses galvanized steel components to mitigate the effects of corrosion on the racking structure. Galvanized steel members are coated in a layer of zinc, which acts as a protective coating. In a situation where the steel structural member would begin to rust, the layer of zinc will corrode first. Only after all the zinc has been consumed by the corrosion reaction, will the steel finally begin to break down. This is a common use of the galvanic properties of dissimilar metals, where one metal acts as a sacrificial corrosion cell to protect another.
The rate and extent of the corrosion reaction depends on several factors, including environmental conditions such as moisture, temperature, and pH levels. Corrosion effects also vary and can require different treatment depending on whether it occurs underground with soil contact or above ground in response to atmospheric conditions.

During the hot dip galvanization process.
Visible difference of the galvanization rising out of the hot dip bath.
Going underground
While soil conditions may not vary as drastically as daily atmospheric conditions, underground conditions nonetheless impact degradation rate of the embedded structural components. Subsurface corrosion also carries a practical challenge that it cannot easily be detected and inspected for after installation. Typically, the EPC will provide a geotechnical report and survey data outlining the soil composition and potential risks.
Terrasmart accounts for soil corrosion in every foundation design. Both our piles and ground screw foundations use galvanized steel to protect the base metal from corrosion. There are several approaches that Terrasmart can take to account for soil corrosion, however our typical approach adheres to industry standard soil corrosion criteria published by the Federal Highway Administration.
Geotechnical reports provide a handful of chemical indicators. If any chemical parameters are outside of an acceptable range, Terrasmart has several other options at its disposal. If necessary, our team can commission a third-party corrosion engineer to provide specific project site corrosion rates in a signed and sealed letter, which are incorporated into our foundation design calculations.
Additionally, Terrasmart consistently collects its own soil samples when conducting pull testing to submit for additional chemical analysis using trusted third-party labs as a supplement to geotechnical reports. Customers who are concerned about the soil test results of their geotechnical reports should inquire about additional soil testing services offered by Terrasmart.
Digging through soil properties
Soil pH and resistivity are the main drivers of the rates of corrosion, particularly for galvanized steel. Concentrations of Chlorides and Sulfates contribute to soil corrosivity as well. Soil samples should be checked to ensure that they’re being tested using ASTM and/or AASHTO test procedures for soil, as using testing standards designed for water samples can provide results that seem correct, but are invalid.
While above-ground corrosion takes place in a medium that is dynamic and ever-changing, soil is a relatively static and unchanging medium. Both ground screws or driven piles derive their foundational strength from a combination of geometry and material properties. Since underground corrosion attacks foundations at a uniform rate, it is a trivial exercise to change the foundation geometry in accordance with the final corrosion rates and design life.
If proving end-of-life is your goal, make sure to scrutinize soil chemistry data. In one case, a customer commissioned a lab that performed the wrong test, applying wastewater tests to soil samples resulting in delays that lasted for several weeks.
Tempering the effects of corrosive soils
Terrasmart deploys a variety of tactics to mitigate underground corrosion risks and extend the foundation’s life:
- Extra Material: Terrasmart’s preferred countermeasure for ground screw corrosion entails adding extra metal — sacrificial steel — to the thread, and the tube of the screw foundation, or perimeter of the driven pile to increase material strength.Because foundation strength is a function of geometry and material properties, adding sacrificial steel is a straight-forward tactic to address both criteria: it changes the geometry by increasing the thickness of the thread. However, sometimes it’s not possible to add sacrificial steel to a component. In those instances, increasing the strength of the material in question can allow more strength per unit of steel, thus increasing the overall design capacity.
- Cathodic protection: This technique makes chemically active areas on a metal surface resistant to corrosion by converting them into a cathode. Supplying an electrical current to the metal reduces the reactivity of the metal, which stops the corrosion attack. Cathodic protection is commonly used in the oil and gas industry for mission-critical infrastructure or to protect submerged or buried metal structures, such as ships, offshore platforms, harbors, etc. Customers will sometimes ask about cathodic measures but as these systems can cost tens of thousands of dollars, they can be cost-prohibitive for PV projects thus rarely used today.
- Third Party Corrosion Services: Terrasmart frequently engages with licensed corrosion engineers to provide expert consulting services on projects which encounter challenging soil conditions. Reviews of geotechnical reports, additional soil samples, and in situ data collection are all important factors which can impact the corrosivity of the soil and the corresponding allowable design life. More data gives our team more options.
Rising up into a corrosive atmosphere
Designing for atmospheric corrosion requires expertise and experience to strike a balance between adding more material, such as zinc, to extend design life while keeping costs and lead times in check.
The question becomes how much sacrificial zinc to apply to the steel before it’s formed into structural members. It’s challenging to assess how long zinc coatings will last in various environments. Three commonly available specifications for measuring zinc quantity are G-90, G-140, and G-235. The following table represents life expectancy estimates for varying hot-dip galvanized finishes and corresponding zinc thickness.
Published by the American Galvanizers Association, the chart above shows the approximate amount of time that each zinc coating will protect the steel from developing enough red rust to require remediation, based on the type of environment in which the structure is built. For example, a G90 coating will require almost no maintenance for about 25 – 27 years in a remote rural climate but will likely need remediation in about 20 years if built in a suburban environment.
Over the years Terrasmart’s engineering team has become more sophisticated with our tools and processes. For instance, Terrasmart consults the corrosion maps published by the Whole Building Design Guide when determining atmospheric corrosion rates for project sites. Another process includes regularly engaging with licensed corrosion engineers when the customer or an outside independent engineer (IE) requests a certain level of technical diligence be done on the atmospheric corrosion.

*This chart shows the different thicknesses of zinc coating that can be applied to the racking structure above ground. Terrasmart’s standard offering is G90, but depending upon the project location and client request, we can provide G140 or G235.
Beware of coastal salt air
Because salty air contains many more chlorides than normal, coastal sites experience much more atmospheric corrosion. These chloride ions increase the efficiency of the corrosion cell and can dramatically increase the rate of galvanic corrosion. The uneven distribution of chloride ions on the metal surface will cause pitting corrosion. There is a measurable difference in the amount of corrosion within 10 miles of a coastline compared to inland areas 20 miles away. The Northeastern seaboard, and microclimates in Hawaii are among the most corrosive environments in the country. Project examples of how Terrasmart addressed these challenges can be seen here on sites in Hawaii and here in the Caribbean.
From the American Galvanizers Association, this figure reflects the selection of zinc coatings used for corrosion protection. The use of thicker, sheet galvanization on a structure is more effective when it comes to corrosion protection versus relying on zinc-rich paint to correct rust spots later in the process. Aftermarket coatings almost never provide the same level of protection as factory applied zinc.
Trust Terrasmart’s corrosion expertise to help you analyze your project’s corrosion data, setting up the right steps to value-engineer a racking system that will deliver the life expectancy your asset owner is looking for.
About Benjamin Share
With eight years of experience in the solar industry, Benjamin has been an instrumental part of Terrasmart’s engineering team, helping design large-scale ground mount solar projects for the commercial and utility segments. Additionally, Benjamin has a Bachelor of Science and a Master’s of Science degree in Electrical Engineering.
The content & opinions in this article are the author’s and do not necessarily represent the views of AltEnergyMag
Comments (0)
This post does not have any comments. Be the first to leave a comment below.
Featured Product
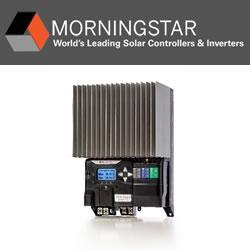