To support both the requirements for a scalable EU battery supply chain, and a reduction in whole lifecycle carbon emissions, greater knowledge of the possibilities and realities of battery recycling is critical.
Reduce, Reuse, Recycle: Understanding the Zero-emissions Automobile Industry
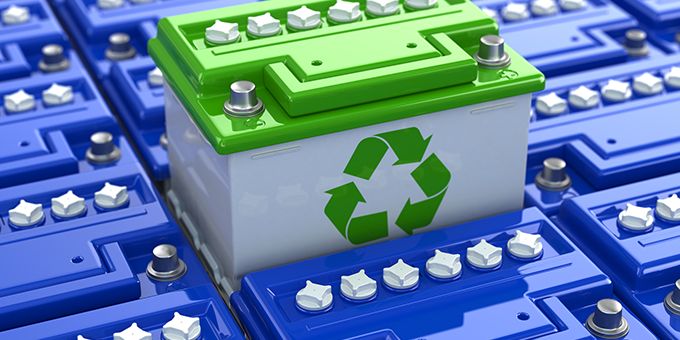
Evie Cleden, Event Producer | International EV Batteries 2023
Currently, one of the largest ongoing challenges for electric vehicle manufacturers is the growth and support of an efficient battery supply chain. In 2021 Environmental Audit Committee Chairman, Rt Hon Philip Dunne MP, said:
“It is welcome news that the Government is acting on our Committee’s recommendations to boost the supply chain for battery electric vehicles. As we move from internal combustion engine vehicles to electric vehicles, we must adopt a circular economy for the batteries to minimise waste of precious metals and to be mindful of our carbon footprint. I am pleased that there will shortly be a consultation on this, to which our Committee plans to contribute.”
With demand for raw materials continuing to grow, the target for a more environmentally friendly vehicle marketplace is being placed under increasing pressure. To support both the requirements for a scalable EU battery supply chain, and a reduction in whole lifecycle carbon emissions, greater knowledge of the possibilities and realities of battery recycling is critical.
In 2022 alone, the RAC registered around 267,000 Battery electric vehicles on UK roads. Existing estimates suggest that around 712,000 zero-emission battery electric vehicles are currently in use. In January 2023, the Society of Motor Manufacturers and Traders (SMMT) recorded that almost a third of all cars produced were fully electric or hybrid, a level of vehicle production export worth £10 billion. Continued growth in EV industry output is essential for a successful transition to net-zero transport, both domestically and globally.
However, as the EV marketplace hurtles towards a goal for increased production, the known capacity and market for end-of-life battery materials and components remains in its infancy. A net-zero automotive industry cannot be built on the production and sale of electric vehicles alone. A more comprehensive overview of the lifecycle emissions of a vehicle from the origin through to the manufacturing, disposal and second life of its components is required to paint an accurate portrait of the industries’ current capacity to reach net-zero goals with a zero-emission product.
As more fully electric and hybrid vehicles begin to disseminate, and new insurance data is released on battery powered vehicles, there grows a distinct cynicism towards the idea of a vehicular ‘circular economy’. As the March 2023 McKinsey report entitled: ‘Battery recycling takes the driver’s seat’ noted, the scrap of cell manufacturing can be as high as 30 percent when a new battery factory launches.
The European Commission has put in place legislation to reduce the environmental damage caused by the disassembly and recycling of end-of-life vehicles (Directive on end-of-life vehicles or ELV Directive). In June 2022 the Council of the European Union enhanced the requirements for CO2 emission performance standards for new passenger cars and new light commercial vehicles in its ‘Fit for 55’ standard. An important element of this is the commitment to present a methodology to assess and report data on embedded CO2 emissions throughout the full lifecycle of cars and vans sold on the EU market by 2025.
In conversation on the issue of battery recycling, National Grid’s then Head of Future Marketing, Graham Cooper noted: ‘the battery will outlive the car… today, most EV batteries have a life expectancy of 15 to 20 years within the car – and a second life beyond’. Cooper goes on to state that ‘there’s still residual life in the viable battery, so it can be hung in your garage or in the cupboard under the stairs as a static battery energy storage system, if you have a renewable energy source like solar panels’.
Whilst it is important to recognise the growing potential and existing capacity for EV batteries to prove useful beyond their initial lifetime, the current durability and weighted potential for second use in contrast to wastage remains problematic. On the topic of their increased battery recycling facilities across the UK, Veolia recorded the potential for 350,000 tonnes of end-of-life electric vehicle batteries to be in the country by 2040. This is largely due to the materials currently used in EV batteries not always being recovered at their ‘maximum value’ and the large amount of specialist knowledge required to continue working with such materials.
This is by no means to suggest that batteries are not the way forward in efforts to decarbonise the vehicle marketplace. Battery technology, from composition to infrastructure, is advancing rapidly and provides a crucial route to minimise the reliance on fossil fuels. However, the contradictions and challenges posed by efficient recycling, sourcing and transportation of materials at the rates required are by no means easy to solve. A look at the wider state of electrification, increasing low carbon vessels in the shipping industry, and efforts to solve embedded carbon in production processes will continue to improve the efficiency of an electric vehicle’s lifecycle. Whilst we may not currently have a complete picture of what an EV battery ‘circular economy’ could look like, steps are being taken to improve the lifecycle efficiency of electric vehicles as they continue to grow in consumer popularity.
In comment on this issue, Daniel Fung, Head of Strategy and Planning at the Advanced Propulsion Centre UK noted:
“Electric vehicle battery recycling will give the UK both security of supply and increase the sustainability of electric vehicles. Potentially, over 90% of critical minerals can be recovered from end-of-life batteries. There is a great opportunity for innovation and scale up of battery recycling in the UK, with a rapid take-up of electric vehicles. Batteries are lasting well in the real world, with automotive batteries estimated to outlast the rest of the car, and then be used in second-life applications. Industry and government have an opportunity now to begin scaleup to ensure we don’t end up shipping this valuable resource overseas for processing once end of life volumes ramp up.”
In support of the engineering community and the ongoing challenges presented by the battery marketplace, the Institution of Mechanical Engineers offers a range of developmental and peer to peer learning opportunities. If you would like to hear more on this topic and the wider EV market place from a range of experts, join us at the IMechE: International EV Batteries Conference (7th-8th November 2023) or discover a variety relevant training opportunities such as those listed below:
-
Re-Engineering for a circular economy course https://www.imeche.org/training-qualifications/training-details/re-engineering-for-a-circular-economy
-
Sustainable product lifecycle design https://www.imeche.org/training-qualifications/training-details/sustainable-product-lifecycle-design
-
Energy storage: https://www.imeche.org/training-qualifications/training-details/energy-storage
The content & opinions in this article are the author’s and do not necessarily represent the views of AltEnergyMag
Comments (0)
This post does not have any comments. Be the first to leave a comment below.
Featured Product
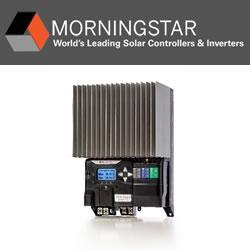