As more businesses, utilities, and state bodies look to solar energy to help them meet their carbon reduction goals and cut energy costs, safety is coming under ever more scrutiny.
Making Solar an Even Safer Investment
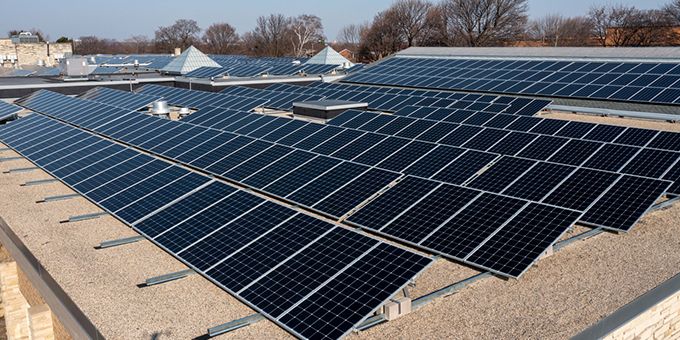
Q&A with | SolarEdge Technologies
Here, Carolyn Humphreys, Commercial & Industrial (C&I) Sales Manager, and Jason Bobruk, Director of Code Compliance, both of inverter and smart energy solution provider SolarEdge, explain what commercial enterprises need to know when considering investing in solar – and why it is imperative that the solar industry works together to drive solar safety forward.
The safety of solar PV seems to be a particularly pertinent topic right now. Why is that?
Carolyn Humphreys (CH): I think the starting point for any conversation about solar PV safety is to acknowledge that it is a safe technology. Commercial infrastructure fires where PV systems are installed generally do not originate from the PV system itself. For example, electrical malfunctions due to domestic heating systems, hospital cooking equipment, factory machinery, flammable materials in warehouses or even lightning, all pose much higher fire risks.
In the unlikely event of a PV system-related fire, one potential source is electrical arcs. They can be caused by faulty or improperly connected cables or connectors, corrosion, animals chewing wires, failed DC isolators, or the overheating of PV system components.
As solar becomes a larger source of energy, it is understandable and wise for safety to continue to be examined. Larger companies are especially sensitive to risk, and as they continue to invest more heavily in solar, it is inevitable that this scrutiny will only increase. However, this is not the only narrative driving the conversation around solar safety. Hand in hand with this, we’re seeing the introduction of more robust safety standards. Innovation is another key driver, with some manufacturers now offering safety features that exceed current regulatory requirements.
What are the safety standards that companies must comply with when installing or operating solar installations?
Jason Bobruk (JB): The US is leading the way in solar safety and that is due in large part to the National Electric Code (NEC), which sets out regulations for the safe design, installation and operation of solar installations as well as other electrical systems. In countries that don’t have a comparable code, we see a much higher incidence of solar-related safety issues. That very clearly demonstrates the importance of regulations in driving safety forward.
While the NEC is a federal code, it is up to individual states when they adopt it. We’ve been really encouraged to see that states seem to be adopting the latest version of the code – NEC 2020 – much more rapidly than they did with previous iterations, which suggests that safety is becoming a bigger priority. It’s also interesting to see a very clear parallel between the higher rates of adoption of our technology in states that adopted the code earlier, because they had to have a safer product sooner.
You mentioned that arc faults can be caused by faulty or improperly connected cables or connectors. What steps can installers take to reduce this risk?
JB: The biggest problem we see in the US is linked to the compatibility of PV connectors. For a variety of reasons, including price pressures, many module suppliers manufacture their own connectors. However, this leads to situations wherein people inter-mate different brands of connectors, not realizing this is not NEC code compliant. While different connectors may fit together initially, over time they might not work well together. One connector could corrode, or there may be a mechanical mismatch that no one sees, and so it heats up and potentially causes a problem that could become an arc fault in the future.
We’re currently working with other leading manufacturers and NEMA on the PV Council to develop a universal PV connector standard. That’s a way off yet, but it’s really important that the industry comes together to work on standards development, to improve safety for everyone. In the meantime, it’s crucial that installers are aware of the risks posed by inter-mating connectors. The bottom line is that it doesn’t matter what brand of Listed connector they use, as long as they use the same brand in each installation.
We’re big champions of installation best practices through our EDGE Academy training program to support installers. In fact, we recently introduced a Commercial Installer Certification Training course designed specifically for the US market. This is a free online training session that takes installers through every step of installing a solar system – from design through to commissioning – to ensure solar systems are safe and NEC-compliant.
However, even with the best training, anyone can have a bad day in the office. So, it’s essential that products are designed to detect and mitigate potential safety issues before they become more serious.
Is this what you meant when you said that innovation is also helping to improve solar safety? Can you tell me more about that?
CH: That’s exactly right. While safety has always been a key driver in the solar industry, it was the arrival of module-level power electronics (MLPE) systems that really raised the bar in terms of solar safety. MLPE systems split the functionality of a traditional string inverter and use Power Optimizers placed directly onto modules to monitor performance in real time. This not only increases energy production, but it also improves safety by identifying and mitigating faults at a module level.
As an example, let’s say a wiring connection heats up in a solar system. Undetected, this small heat gain could develop into a bigger problem. However, using sensors placed on the inverter’s terminal blocks, our system will detect the high temperature, identify the source immediately, and isolate the Power Optimizers from the inverter and each other using our built-in SafeDCTM technology function. It will also alert the installer or asset owner, enabling them to remedy the problem right away. This isn’t possible in a traditional string inverter with a separate rapid shutdown box. Neither the inverter, nor the rapid shut down box, is able to identify which modules are at fault, which may result in the whole string being shut down. If this happens, more energy will be lost, and a truck will need to be rolled for additional trouble shooting.
SafeDC also provides protection for maintenance personnel or firefighters who need to access the roof. As I’ve already mentioned, solar is a safe technology. However, the fact is that where there is a combination of sunlight, PV modules and wires that are energized with high DC voltages, there could be up to 1000 volts of electricity being generated on the roof. In traditional systems, even when the inverter is shut down, that high voltage from the modules remains active, which means older technologies could pose an electrocution risk. With SafeDC, each module is reduced to a touch-safe 1V in less than one minute. This is important for any personnel who need to get on the roof quickly.
It also enables firefighters to tackle fires more efficiently, safe in the knowledge that they can turn their hoses on a building without the risk that it could create further safety issues, or even a secondary fire.
Are MLPE systems or separate devices the only way to achieve rapid shut down? Wasn’t UL 3741 introduced to expand the range of options available to meet this requirement?
JB: That’s a really important question. UL3741 is a flexible standard that makes use of both MLPE and non-MLPE solutions. Since its introduction in 2020, we have seen some suppliers come to market with non-rapid shutdown solutions that don’t require MLPE. While these solutions are NEC compliant, there are concerns that they offer only the barest minimum in terms of solar safety.
In these solutions, AC conductors are de-energized using traditional string inverters. To achieve this, the inverter cannot be located more than one foot away from the array to limit exposure to dangerous energized DC conductors. Straight away this brings limitations. For example, design options are restricted because you lose flexibility of inverter placement.
However, by far the biggest issue with this type of solution is that all array wiring remains fully energized at hazardous levels. This means that only trained firefighters in full PPE can safely access the array. And even then, they will have to work around up to 1000V, 20A circuits with sharp tools. It offers no protection at all for maintenance staff, installers, roofers or anyone else that needs access to the rooftop area around the array.
In some cases, when MLPE is not used, the risk to both people and property is increased by the dependency on unreliable wire management, which also requires specialized training and ongoing inspections and maintenance to remain compliant and safe. For all of these reasons, we strongly believe de-energizing the array with proven, listed rapid shutdown technology, like SafeDC is the safest approach.
Improving safety sounds like a no-brainer. Why wouldn’t businesses choose the safest possible solution?
CH: A lack of knowledge about the alternative options available can be a contributing factor, so market education is always important. Just in the last month alone I can think of several occasions where I’ve visited big commercial customers, and when I’ve highlighted the role these safety features can play, it’s a lightbulb moment for them. They very quickly understand that choosing a system with integrated safety solutions is a smart business decision. Just consider the cost to any enterprise – both to the bottom line and its reputation – of a single day of downtime. In many industries, this can add up to tens or even hundreds of thousands of dollars per hour. By choosing a solar solution that can prevent safety issues before they occur, businesses can often offset their investment in solar by preventing a fault from occurring.
Do you have any final words of advice for commercial organisations who are considering solar PV?
CH: Solar systems are now viewed as long-term investments that need to be managed, and closely monitored, in order to maximize the investment and bottom-line savings. As with any significant investment, it is important to understand the impact of every decision, from the design and component selection, and choice of installer, to the operation and maintenance plan, because each impacts the safety, longevity and return on investment of the system.
SolarEdge optimized array on Ongna Wood Products’ manufacturing facility – as a company working with wood and heat, safety is a crucial consideration for the Wisconsin-based company
While safety has always been a key driver in the solar industry, the arrival of MLPE systems raised the bar in terms of solar safety
Wauwatosa City Council is amongst the growing number of state bodies, businesses and utilities that are adopting solar to meet ambitious carbon reduction targets
The content & opinions in this article are the author’s and do not necessarily represent the views of AltEnergyMag
Comments (0)
This post does not have any comments. Be the first to leave a comment below.
Featured Product
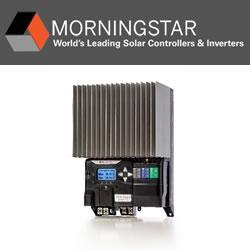