In battery pack manufacturing, the cells are often already assembled and the engineer is challenged with coming up with a design to join them in series and parallel to deliver optimum energy. A typical Li-ion cell is constructed of nickel plated cold rolled steel.
e-Mobility. Battery Pack Manufacturing and Beyond: How 3 Welding Technologies Stack Up
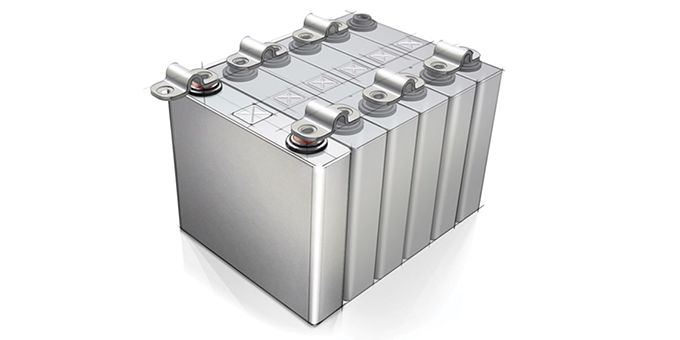
Article from | AMADA WELD TECH INC.
You have probably noticed the increasing numbers of electric vehicles and other transportation devices on the roads today including private automobiles, transportation trucks, bikes, motorcycles, scooters and other modes of transportation driven by electrical power, all of which is provided by stored energy in batteries.
This electrification – which applies across several sectors – is neatly wrapped up in new terminology: e-Mobility or Electro Mobility. According to Gartner, e-Mobility “represents the concept of using electric powertrain technologies, in-vehicle information and communications technologies and connected infrastructures to enable the electric propulsion of vehicles and fleets.” A BIG piece of the e-Mobility puzzle is battery and battery pack manufacturing.
The challenges encountered in bringing this technology to market include the demand for reduced weight, expanded range, faster charge times and lower costs. Translated into manufacturing goals, the batteries need to possess higher capacity with negligible energy loss delivering to the drivetrain, higher current carrying capacity for charging, and be made of light-weight, lower cost materials. And since the e-mobility market is so rapidly expanding, there are additional manufacturing challenges, including the demand for higher throughput and quality.
Some of these goals can be achieved by improved cell chemistries and battery pack design, but others can be improved only by considering the joint quality between the batteries and the current collectors.
It’s a tall order, and that is why special attention must be paid to the welding system selected for EV battery pack manufacturing. In this post we will examine the key challenges in tab to cell connection and see how the available welding technology options measure up. We’ll focus on:
- Resistance welding
- Laser welding
- Micro TIG welding
Another viable option – ultrasonic welding – is not covered in detail but is shown in a matrix summing up how the technologies compare.
Tab to Cell Connection Manufacturing Challenges
The challenges listed above can be broken down into desirable solutions. The following graphic shows five key challenges typically encountered in tab to cell battery connections:
- Dissimilar metal welding
- Thicker tab materials
- High speed positioning
- Tooling design
- Process monitoring
Let’s see how the three welding technologies measure up:
DISSIMILAR METAL WELDING
In battery pack manufacturing, the cells are often already assembled and the engineer is challenged with coming up with a design to join them in series and parallel to deliver optimum energy. A typical Li-ion cell is constructed of nickel plated cold rolled steel. We know that we can easily join a nickel or steel tab to this material, but both materials possess high resistance.
Therefore, ideally, the engineer would choose a more conductive tab material like aluminum or copper – materials that will minimize thermal loss and provide a means to quickly discharge and charge the batteries. However, can these dissimilar materials be joined? Which welding technology is best? Let’s take a look.
Resistance Welding
Material conductivity somewhat limits the ability to join materials using resistance technology. As the name indicates, resistance is required to heat and melt the parts. When the material is conductive – like aluminum or copper – this technology is not suitable. Some novel alloys which combine both resistive and conductive material are starting to be used – like Ni SS Cu (SIGMAclad®), – which provide a resistive layer to make the weld and a conductive layer to meet the challenges above.
Micro TIG Welding
Micro TIG welding is strictly a fusion process, which limits materials to be joined to those with compatible chemistries: welding copper to steel is possible, but aluminum to steel is not.
Laser Welding
In general, laser welding is also a fusion welding process. However, new laser sources make it possible to avoid the traditional fusion process and join materials with limited intermetallic mixing. The resulting mechanical joint which is akin to Velcro®, provides good electrical and thermal contact. This enables even the previously unthinkable joining of aluminum and cold rolled steel without forming the brittle intermetallic structure of a traditional fusion weld. The fitness and purpose of the weld needs to be thoroughly tested, however. In the case of an aluminum battery tab to a nickel plated cold rolled steel battery can the mechanical pull strength is quite strong along the direction of anticipated vibrations. Thermal and shock testing shows that the resultant mechanical joint meets conductivity, strength and overall durability requirements.
THICKER TAB MATERIALS
Why are battery manufacturers using thicker tab materials? Higher current carrying capability. However, thicker tabs also require more energy and more precise input to avoid burning through them and damaging the battery cell.
Resistance Welding
When using resistance spot welding, careful consideration of the current path between the electrodes must be considered. The electrons will always flow along the path of least resistance, thus as the tabs get thicker, the energy will travel directly between the electrodes with little to no energy at the desired interface. This starts to occur for nickel tabs >0.005” (125 microns). To avoid the shunting of current, the tab needs to be carefully designed with slots and tabs to concentrate the energy and guide the weld energy to specific spots.
Laser Welding
When laser welding, the joint geometry of the battery tab weld is a lap weld, which means the laser must penetrate fully through the top tab and at least slightly into the can wall. It is possible to reach very high penetrations (>0.4” or >10 mm) with single mode fiber lasers, however, from a practical point of view the thickest tabs are on the order of 0.020” (500 microns) for can walls that are 0.012-0.014” (0.3-0.35 mm), though preferably the tab thickness of 0.010” (0.25 mm) is preferred to have best manufacturing success.
Micro TIG Welding
Micro TIG welding can also handle up to 0.020-inches (500 micron) thick material with a 200 A output power supply, but thicker tab material requires additional heat that can be a safety concern.
HIGH SPEED POSITIONING
Battery modules are getting larger and larger and the demand for battery packs is ever-increasing. High speed positioning, therefore, is a very desirable system feature resulting in increased product throughput. There are several critical factors affecting cycle time including the actuation/motion of head, weld cycle time, and actuation/motion between cells that need to be considered for each welding technology.
Resistance Welding
There are a number of motion actuations and process time to be taken into account when using resistance welding. For each weld, the electrodes on the weld head must be lowered to the workpiece, squeeze time (is amount of time to apply pressure until the weld fires) must be applied, and then there is the weld time, hold time (after weld fires and starts to cool), and finally raising the electrodes back to home position.
One must also calculate the motion time to move from cell to cell.
A back-of-the-envelope type calculation is shown in Table 1. Per site, it is estimated to take 2.2 seconds. For a battery pack consisting of 117 Cells (9 x 13), this means there are 234 sites to weld and total process time of 514.8 seconds.
Laser Welding
Since laser welding is a non-contact process, the only motion is making a weld pattern and the motion moving the beam from cell to cell. The weld cycle time is a combination of shots and small motion on a cell.
For laser welding, the back-of-the-envelope calculation for time to process 234 weld locations is estimated to be 257.4 seconds.
Micro TIG Welding
With Micro TIG welding, cycle time considerations include the motion of the torch going up and moving from cell to cell.
Because of the motion up and down of the torch, the weld time is longer than laser welding and estimated to be 491.4 seconds.
Table 1 provides an overview of the cycle time comparison of the three technologies. Laser welding is significantly faster showing the allure of the laser for battery module welding. Cycle time can be reduced even further with the use of a galvo scanning system, where some motion is handled by quick motions in the galvo head, and then indexed after all cells within the welding field are addressed.
RW | LW* | MT | |
Motion from cell to cell | 1 s | 1 s | 1 s |
Head actuation (down) | 0.5 s | N/A | 0.5 s |
Weld cycle time | 200 ms | 100 ms | 100 ms |
Head actuation(up) | 0.5 s | N/A | 0.5 s |
TOTAL (per site) | 2.2 s | 1.5 s | 2.1 s |
TOTAL (234 welds) | 514.8 s | 257.4 s | 491.4 s |
*battery pack on XY table with fixed focus head |
Table 1- Estimation and comparison of cycle times for resistance welding (RW), Laser Welding (LW) and Micro TIG Welding (MT)
TOOLING DESIGN
The number one rule in welding is – you can’t weld air! In order to achieve a successful weld, the tab and cell must be in intimate contact. Some welding technologies have a built-in tooling mechanism because they are contact processes. Others are non-contact and require special production tooling to hold the parts in close contact when the energy is delivered.
As battery packs become larger, there are additional considerations to account for. For example, the welding system must account for varying cell heights and maintain flatness over larger modules. No matter which technology is used, the tooling design used to hold the parts must provide access to the weld area, cover part tolerances and meet production throughput requirements.
Resistance Welding
Resistance welding is essentially a self-tooling process; the electrodes come down on the parts forcing them into intimate contact. There are limitations to the amount of gap, but generally this is the easiest of the technologies in this regard. Tooling is generally still required to hold multiple parts in place.
Laser Welding
Because laser welding is a non-contact welding process, it does not have the self-tooling properties of resistance welding. Tooling must be designed to hold the two parts in intimate contact. In general, it is best to hold as close as possible to the actual location of the weld to limit the chance that the tab material is deformed at the weld site. Also – special consideration for lasers – the tooling must not interfere with laser beam access. The laser is focused down onto the part forming a cone – this cone must be clear from any obstruction to deliver the right amount of energy to the part.
Micro TIG
Micro TIG welding – as an arc welding process – is also a non-contact process. So like laser welding, a proper tool must be designed to hold the parts in intimate contact. Standard Micro TIG uses a fixed torch, with the ideal separation range of the electrode to the workpiece of between 1-3 mm (within 250 microns). The torch nozzle is often quite large in relation to the spot weld, which can make tooling design challenging. Some self-tooling concepts are available with the use of a copper sheath.
PROCESS MONITORING
The use of process monitoring is growing, based on the desire for higher throughput, and the increased safety, higher quality output, and the ability to trace product from cradle to grave. The challenge is to conduct monitoring in real time.
Resistance Welding
Resistance weld monitors can measure current, voltage, force, displacement, and time. These weld checkers are well established in industry. Specifically for battery packs it is important to measure displacement (as the projections collapse) and voltage.
Laser Welding
Laser weld monitors are new to the scene, but have been gaining a foothold over the past 5 years. Different types of sensors can detect the signal array that is emitted during the laser-matter interaction. Types of signals include: reflection of the laser beam, thermal, visible light, and UV light. In addition, sound can also be recorded. These are all the signals above the surface of the part. It is also possible to look into the penetration of the laser energy into the part.
Micro TIG
Micro TIG weld monitors monitor current and voltage (after arc start).
While each monitor may check different parameters, all of the ones listed above can measure each and every weld and compare it with known good values to make decisions on the weld. Typically, many welds are made and statistics used to create upper and lower limits of “good” values. If the new weld falls within these limits, it infers that a weld has been successful. If it fall outside of the limits, an anomaly is noted and a NG signal can be issued from the parts.
Summing it Up
We have reviewed 5 key challenges in battery pack welding – and discussed how three different joining technologies fare in each of these categories. Here is a table of the five key challenges discussed above and an overall scorecard of where each technology stands.
The bottom line is that each technology has its place in today’s battery pack manufacturing. Proper equipment selection depends on battery pack design, cost and quality requirements, and production requirements.
For even more information, watch our webinar “Solutions in e-Mobility: 3 Distinct Technologies for Battery Manufacturing.”
The content & opinions in this article are the author’s and do not necessarily represent the views of AltEnergyMag
Comments (0)
This post does not have any comments. Be the first to leave a comment below.
Featured Product
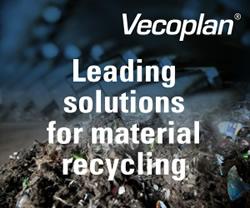