In this series, we’ll debunk common misconceptions and shed some light on how performance is impacted by MLPE technologies.
The Top 10 Most Common Myths about Traditional DC Power Optimizers: Part 1
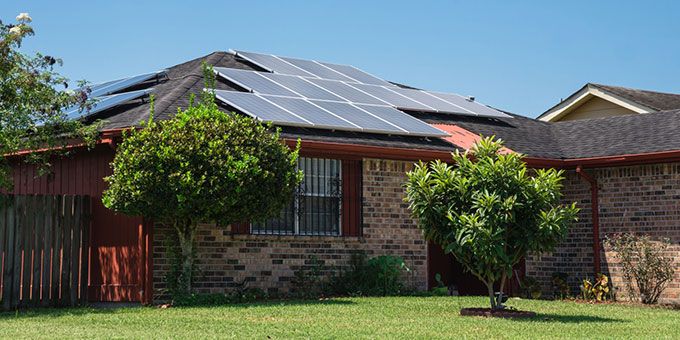
Blair Reynolds for | SMA America
A University Study recently concluded that SMA ShadeFix optimization outperforms traditional module level optimizers, including in partially shaded arrays. That might surprise most American solar installers, where module-level power electronic (MLPE) suppliers sit atop the residential PV rankings. But, traditional, module-based optimization is not the standard in the rest of the world. Why is that the case? In this three-part series, we’ll debunk common misconceptions and shed some light on how performance is impacted by MLPE technologies.
Understanding Traditional DC Optimizer Technology
To understand how a power optimizer operates, it is first necessary to understand that a power optimizer is actually just a buck-boost converter with built-in communications. A buck–boost converter is a type of DC-to-DC converter that has an output voltage magnitude that is either greater than or less than the input voltage magnitude. It operates by simply adjusting DC voltage either up or down. Modern string inverters also have this component built-in, but it is commonly referred to as a Maximum Power Point Tracking (MPPT) input.
A power optimizer-based system architecture is actually built upon a string inverter topology. Groups of PV modules are connected together in series strings. The primary difference is that the DC:DC stage of the inverter is not built-in to the inverter, but instead it is distributed across the PV array. What the power optimizers are actually doing is “optimizing” the string voltage to match the design input voltage of the inverter (typ. 380 or 400 Vdc for single phase systems).
Makes sense, right? Ok, now on to the myths:
Myth #1) Power Optimizers generate more energy for shaded PV arrays
This myth is based on the marketing claims that power optimizers produce more power when one or more modules are shaded. While the basis of this claim is true, more power does not always result in more energy yield. Allow me to explain: As I mentioned above, the power optimizer serves the same function as the DC:DC stage on a modern string inverter — the primary difference being that they are distributed across the array rather than built-in to the inverter. Similar to the maximum power point tracker of a modern string inverter, the power optimizers adjust the operating voltage of the PV modules to match the DC string voltage required to operate the inverter. When one or more PV modules in the string become heavily shaded (relative to the other modules in the string) the function of the power optimizer behaves a lot like MPPT because the current path through those shaded portions of the PV modules have essentially been bypassed (not by the optimizer, but rather by the PV module bypass diodes). The power optimizer will therefore operate (1/3) or (2/3) of the module at a maximum power point based on the reduced voltage output of the shaded module.
Now, consider that the time of day when shadows are the longest are in the early morning and in the late afternoon. During these times of day, the irradiance is also the lowest. Therefore a 4-5% power gain in the mornings does not translate into very much additional energy yield. In fact, a number of studies suggest that the internal power consumption of the optimizers bucking and boosting voltage all-day everyday outweighs the additional energy harvest early and late in the day. Power optimizers would only contribute a meaningful benefit in terms of energy yield if one or more modules were heavily shaded during the middle of the day. In this scenario, I would question the value of placing the module(s) in that location in the first place. If the entire array is shaded evenly (like from a cloud for example) the power optimizers do not contribute any meaningful additional power or energy.
Myth #2) Traditional Power Optimizers generate more additional energy than they consume
Power optimizers are subject to tare losses associated with running the onboard power electronics and powerline communications. These devices consume processing power and they suck that power from the PV modules anytime the PV modules are in operation. Furthermore, power optimizers are almost constantly bucking or boosting voltage all-day, every day. Remember: unlike a microinverter which is truly operating independently, the job of a power optimizer is to operate the module at a voltage which allows the aggregate group in a string to match the DC bus voltage (380 or 400V) required to operate the inverter. Under sub-optimal operating conditions (for example, when there is module mismatch or shading) the optimizers are forced to adjust their operating voltage such that the optimizer efficiency is reduced. The worse the operating conditions become, the optimizer efficiency declines accordingly, because the devices are forced to work harder to adjust the voltage.
And, then there is the increased voltage drop (which is not accounted for on the power optimizer datasheet). A power optimizer adds 8.84 feet of extra 12 AWG cable (including both input and output cables) to every module it is connected to. That extra cable alone creates a voltage drop of about 0.27 Volts lost per optimizer in full sun. That’s over 145 Watts of lost power in a 12 kWp system which correlates to more than 265 kWh of lost solar production per year, due to extra cabling alone. Note: this calculation does not factor in the added resistive losses associated with the additional four connectors per power optimizer.
At the end of the day, plant owners care most about savings, which is directly related to energy yield.
Myth #3) Power Optimizers (or microinverters) are required for Code Compliance
This is a false narrative which is all too often misunderstood. Maybe someday I will write a tell-all about how Rapid Shutdown came to pass, but in the meantime, I will simply say that the primary beneficiaries of this requirement have been the MLPE companies, not first responders. The NEC requires controlled conductors both inside and outside the array boundary. For typical PV module construction, there are two practical ways to comply with NEC 690.12 rapid shutdown within the array boundary. The first is 690.12.(B)(2)(1): The PV array must be listed as a rapid shutdown PV array. What does that mean? It means that the equipment must be listed to UL Standard 3741 or a similar standard. A rapid shutdown PV array (also known as a PV hazard control array in the 2020 code)which has been certified for safe interaction with first responders is the lowest cost, most reliable way to design and build a code compliant system. The second method for complying with rapid shutdown within the array boundary is NEC 690.12(B)(2)(2) which requires reducing the voltage within the array to less than 80 volts within 30 seconds. This is the path of compliance used by most MLPE equipment. However, the trouble with this method is that is only specifies a voltage limit whereas it is actually current which is dangerous and life threatening. This path requires redundant module level switches to essentially disconnect the series connection of adjacent PV modules. However this method also presents a safety loophole whereas the PV module itself could have an operating voltage higher than 80 volts. Thus if a first responder were to come into contact with the electrical circuit within the PV module itself (which is certainly possible when the module is burning or if an axe or tool was to penetrate the PV module glass), she/he could potentially be exposed to not only more than 80V, but also a dangerous level of current. Thus only the first method of code compliance, 690.12(B)(2)(1), ensures that the entire PV array has been evaluated for safe interactions by first responders.
Myth #4) Power Optimizers detect ‘failed’ PV modules
To understand this myth, one must first understand when and how PV modules fail. This topic alone warrants its own article, but the short story is that PV module failure rates are incredibly low — especially when compared to the failure rates of power optimizers.
The top causes of module failure include:
#1) Damage to cables from rodents or wire management. This typically results in a ground fault or an arc-fault. In either case the entire PV plant will be (or is supposed to be) offline. Optimizers will not have an impact on this scenario.
#2) Environmental stress which leads to solder bond failures, delamination, or moisture ingress. Often the result is a short circuit within the PV module. This situation (is supposed to be) detected by the AFCI circuit of the inverter and would render the entire PV plant inoperable while the situation persists. Optimizers will not have an impact on this scenario.
#3) Hot spots due to ‘hard’ shading from nearby objects. The power optimizer will not prevent this. Only system design best practices of the module placement will prevent this situation.
The sad truth is that most installers use the module level monitoring sensors built-in to power optimizers to detect – guess what – failed power optimizers!
Myth #5) Traditional Power Optimizers are 99% efficient
While the power inversion component (i.e. inverter) in the system may have a “CEC Weighted Efficiency” of 99% (actually it’s 98.8%, but the CEC rounds this up to the next half a percent), there is no standardized method for testing or verifying the “CEC Efficiency” of a module level power optimizer. The datasheet may list a “Weighted Efficiency” for the power optimizer but this is a marketing term without any common definition or standardized test like “CEC or EU Weighted Efficiency”. While there might be one operating point of an optimizer where it operates at 99% efficiency, most operating points will likely be running at much less than 99%, attributing to additional losses in your PV system.
The further the true string voltage is away from the inverter fixed operating voltage (a.k.a. “optimized voltage”) the lower the efficiency of the PV string.
The content & opinions in this article are the author’s and do not necessarily represent the views of AltEnergyMag
Comments (0)
This post does not have any comments. Be the first to leave a comment below.
Featured Product
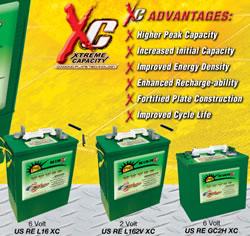