More and more homeowners are requesting battery backup solutions as part of their solar power installations. With increased adoption of solar power, concerns about fire hazards are likely to grow. Are these concerns justified?
Battery Safety Concerns Can Be Addressed With Proper Design and Manufacturing
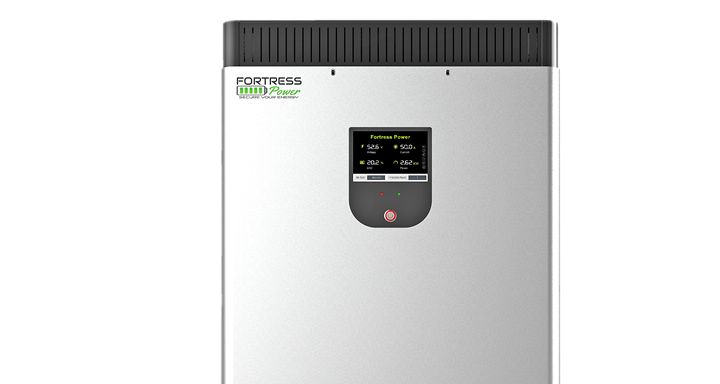
Article from | Fortress Power
Early in December, LG Chem recalled several residential solar battery storage products because of concerns about fire safety. Five fires involving these battery systems have been reported, including an explosion at an energy storage facility in Arizona caused several injuries.
According to the recall notice, cells inside the battery units are at risk of overheating and starting fires. This recall comes on the heels of several fires involving Tesla solar products.
More and more homeowners are requesting battery backup solutions as part of their solar power installations. With increased adoption of solar power, concerns about fire hazards are likely to grow.
Are these concerns justified?
That depends on the battery storage solution you choose and how that solution is designed and manufactured. Some in the industry have deflected blame to installers, claiming that the risk of a fire is virtually non-existent if the battery is installed according to manufacturer specifications.
While a best practices-based approach to installation is certainly recommended, solar battery storage units can be manufactured in a way that all but eliminates the risk of fire, even if the battery is improperly installed.
Although the risk of a fire is very low, put yourself in the shoes of a homeowner who just saw footage of a residential fire that had been traced back to the solar battery. The industry needs to respond to this challenge with safer products, not empty assurances.
There are three basic elements in manufacturing that affect the risk of fire – chemistry, battery pack design, and the manufacturing process itself.
When designing a battery, the manufacturer chooses the chemistry that is ideal for a specific application. Let’s discuss two of the most popular chemistries used for energy storage – lithium nickel manganese cobalt oxide (NMC) and lithium iron phosphate (LFP).
NMC chemistry is ideal for energy storage in the automotive industry. Most automakers use NMC because of the battery’s energy density and battery cell’s higher voltage.
LFP chemistry is ideal for residential solar power storage. While lithium ion batteries can cause a fire or explosion due to overheating during charging, lithium iron phosphate is very tolerant to overcharge and discharge.
Because of the different cathode chemistry compared to NMC, the thermal runaway tolerance is increased significantly by over 100°F, resulting in major safety differences between the two chemistries. NMC is significantly more likely to catch fire compared to iron phosphate. Likewise, under normal operating conditions, LFP will maintain a more stable internal temperature when constantly cycling.
In addition to chemistry, battery pack design should account for performance and safety. Isolation, high voltage, and thermal runaway are just as important as all other structural considerations.
The battery pack design should have enough built-in redundancy and use the right electrical components. This will ensure the system works properly and can accommodate fluctuating power consumption patterns.
Also, a battery management system that monitors the temperature, voltage, and input/output power is important to synchronize the whole system’s performance and eliminate the risk of fire..
The right thermal material makes it possible for a solar battery storage unit to handle more current and higher voltage without creating a fire hazard. A high-heat conductive material such as aluminum, which transfers heat five to six times better than other materials, makes it possible to better control the internal temperature of the battery pack.
Finally, there must be a tightly controlled manufacturing process and environment. If you don’t use the right ingredients, add them in the right order, and combine them in the right way, you’ll ruin the entire dish. Highly automated processes and 100 percent traceability are crucial in the manufacturing plant. Every step of the manufacturing process must be precise, consistent, and quality-checked to ensure the safety of each solar battery.
As families prioritize climate-friendly energy consumption and increasingly turn to solar battery storage as a source of backup power, concerns about fire safety are likely to grow. Both installers and homeowners should research their battery options and understand what factors contributes to fire risk. At the same time, the industry can take steps to design and manufacture battery units that build confidence in solar energy storage.
The content & opinions in this article are the author’s and do not necessarily represent the views of AltEnergyMag
Comments (0)
This post does not have any comments. Be the first to leave a comment below.
Featured Product
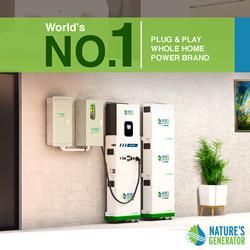