When installing a solar array, having a coverboard as part of the roofing assembly is a best practice. As such, most manufacturers of solar mounts test and evaluate their mechanical attachment products with a coverboard over polyisocyanurate (polyiso) insulation.
2021 Top Article - Best Practices for Installing a Solar-Ready Low Slope Roof
Q&A with Kevin Kervick, Solar Products Business Manager | OMG Roofing Products
Tell us about yourself and OMG Roofing Products.
My name is Kevin Kervick, and I am the Solar Products Business Manager for OMG. My responsibilities include developing and implementing a strategic plan for the company’s solar business, managing the Solar P&L, as well as growing the business with our National Solar Sales Manager, and solar-related product development.
OMG Solar is a business unit of OMG Roofing Products, which is a leading manufacturer of commercial roofing products including specialty roofing fasteners, adhesives, drains, conduit/pipe supports as well as advanced productivity tools. The company’s focus is delivering products and services that improve contractor productivity and enhance roof system performance.
For 40 years OMG has been in the business of providing products and technologies for securing roofing systems to commercial buildings. So, developing products designed to secure solar systems to commercial roofs is a natural extension of the business. In addition to the fastest-installing conduit support in the industry, we currently have four solar products in the PowerGrip Solar Mount product line. All our mounts are designed to secure the system directly to the structural members of the building, not just the roof cover itself. We believe that this is a critical distinction between our products and others on the market. Remember, the role of the roof is to keep water and the elements out, not to hold things like a solar array in place. Roof covers are just not designed for that.
What are best practices for installing a solar-ready low slope roof?
When installing a solar array, having a coverboard as part of the roofing assembly is a best practice. As such, most manufacturers of solar mounts test and evaluate their mechanical attachment products with a coverboard over polyisocyanurate (polyiso) insulation, which is commonly used in commercial roofing applications. The purpose of the coverboard is to protect the insulation beneath it from being compressed by the solar array, which could result in excessive ponding on the roof. Ponding water is a problem for several reasons. First, it is not good for the roof membrane in the long run, and second, and more importantly, water is heavy! Water weights approximately 5 lbs. per inch, per each square foot of surface, so a relatively small 20-ft. x 20-ft. depression or sump with 1 inch of water weighs 2,000 lbs. That is an additional ton of live load added to the building’s roof. Many buildings today are not capable of handling that type of load.
However, coverboards are often not used in commercial roofing applications unless the roof is subject to excessive traffic or something heavy is being installed. As a result, many rooftop solar installations do not benefit from a coverboard. This deviation between best and actual practice can result in significant problems resulting from compressive forces.
What other problems can occur when a coverboard is not used under the array?
Polyiso insulation will fracture at a point load of 18 -20 PSI. Fractured insulation is bad for three reasons:
-
Ponding water, as mentioned above
-
A large loss of R-Value – which is ironic because a hoped-for source of energy efficiency (solar) became a cause of a major energy inefficiency
-
The roof warranty may be voided due to damage caused by owner-installed “overburden” (the term used to describe additional items installed on the roof – solar, HVAC, process piping, etc.).
As noted in the answer above, the purpose of a coverboard is to prevent damage to the insulation and roofing assembly. The large roofing system companies (also known as the roof warranty holders!) typically specify maximum dead loads on polyiso insulation of about 5 PSI, which allows for additional dynamic compressive loads plus a safety factor before hitting 18 -20 PSI ultimate failure. While the building’s structural members (framing, girders, joists, etc.) way be able to withstand the total weight of a solar system, uncovered polyiso insulation can still only handle a 5 PSI point load. This is often the weakest link in the weight calculation.
Most mechanical attachments manage compressive point loads by spreading the weight onto the polyiso by using the total surface area of the mounting plate. A commonly available 5.5-inch diameter attachment plate has just 23.75 square inches of surface area, which translates into a maximum point load capacity of only 119 lbs. (5 PSI limit x 23.75 square inches). Any additional point load weight puts the insulation at risk of fracturing.
OMG PowerGrip Universal 7 Roof Mount which does not rely on dispersing weight over the insulation’s surface area to handle compressive point loads. Instead, the installation fasteners are designed as load-bearing columns. This is one of the only roof mounts in the industry capable of transferring the compressive load directly to the roof deck, completely bypassing the insulation layer.
How is OMG addressing this issue?
We have a couple of approaches. Our PowerGrip Plus product uses one of the largest base plates in the industry. At 10.5-inches, it has a total surface area of 86.5-square inches. This allows it to effectively disperse a point load of 432 lbs. before exceeding the warranty holder’s recommended 5 PSI limit.
Our PowerGrip Universal 7 and Universal 11 products are the only mounts that do not rely on dispersing weight over the insulation’s surface area to handle compressive point loads. Instead, they both employ an innovative mechanism that converts the installation fasteners into load-bearing columns. These are the only attachments capable of transferring the compressive load directly to the roof deck, completely bypassing the insulation layer.
What role do the fasteners play in the performance of the solar roof mounts?
The screws are critically important. OMG is first and foremost a roofing products company, and manufacturing fasteners specifically for commercial roofing is the foundation of our business. Our screws (or adhesives) can be found in nearly 70% of low-slope commercial roofs in the country.
The uplift and shear values of a solar mount are greatly affected by the screws used to secure it to the roof. If the installer uses different fasteners than were tested by the solar mount manufacturer, the performance of the installed mount will not match the manufacturer’s test. All the engineer’s calculations can be rendered null and void by the installer’s fastener selection. In addition, roofing screws are designed for specific substrates, so the proper fastener depends on the deck type (i.e., steel, concrete, OSB, plywood, purlins, etc.). Furthermore, not all #14 or #15 screws are equivalent. The reference number just refers to the gauge of the wire used in forming the screw. Different manufacturers can make #14 screws with different thread profiles, points, hardness, and head styles – which results in performance variations as measured by pullout values. Lastly, it should be noted that the pull-out resistance values actually measure of the roof deck’s condition, not the fastener’s strength. Typically, it is the roof deck, not the fastener, that fails.
OMG manufacturers billions of fasteners annually in our US-based manufacturing plants. We routinely help installers and engineers spec the proper screw for the job. With our national field service force, we perform over a thousand rooftop fastener pull tests annually to measure the resistance performance of the roof deck in question. This is an extremely helpful service to the engineers who put their stamps on the plans. If you are an engineer that is designing a system using our mounts and would like a fastener pull test to evaluate the specific roof deck, please contact me.
In what situations should installers avoid 100% ballasted systems?
To discuss this, installers must understand the difference between a fully adhered and a mechanically attached roof. A fully adhered roof uses adhesive to secure the membrane or roof cover to the material below, which may also have a base layer of insulation that is screwed to the structural deck. A mechanically attached roof uses screws and plates to secure the membrane along its edge. The screws and plates are covered by the edge of the adjacent membrane, which creates a “lap seam” that is sealed to encapsulate the screws and plates. Mechanically attached roofs are subject to billowing, while fully adhered roofs are not. Billowing is when the membrane inflates and balloons up, generating a great deal of force, which in extreme cases can take a 100% ballasted solar system on a wild ride.
Roof slope is another issue. Ballasted systems can and do move around based not only on wind and weather, but also on the thermal expansion and contraction of both the building and the solar rack/rails. Thermal expansion typically occurs in a down-slope direction. So does thermal contraction. If wind is also common in the down-slope direction, a 100% ballasted system can, over time, ‘walk’ off the roof.
Factory Mutual is a global insurance company that performs product testing and certification of building components. Factory Mutual’s solar guidance disallows 100% ballasted solar arrays on mechanically attached roofs. Their guidance also disallows 100% ballasted systems on roofs that have a slope greater than ½” per 12” (or 2.4°).
Mechanically attached roofs are subject to billowing, while fully adhered roofs are not. Billowing is when the membrane inflates and balloons up, generating a great deal of force, which in extreme cases can take a 100% ballasted solar system on a wild ride. The attached image shows a typical 10-foot wide, mechanically attached membrane, on OMG’s test deck, pressurized to simulate wind-uplift. Membrane can billow up to 3-ft. off the surface of the roof. Billowing is a major concern for 100% ballasted solar arrays.
From the corrugated steel deck up, the roof assembly typically includes insulation, secured in place with insulation fasteners and plates or oversized washers. Sometimes a cover board (e.g. gypsum) is secured over the insulation using screws and plates, or an adhesive. The membrane or roof cover is secured over the top using a different set of screws and plates, installed along the edge of the membrane. The next section of membrane overlaps the installed fasteners and plates, encapsulating them. The seam is made by fusing the thermoplastic materials together with a hot-air welder to create a seam that can be made as strong as the membrane itself.
Why is ballast the default attachment method?
Ballast is easy. But also, many installers believe, incorrectly, that ballasted systems will not void a roofing warranty because they do not “penetrate the roof.” This is a misunderstanding of how roof warranties work. Everything that is placed on the roof by the building owner is called “overburden” by the warranty holder. All overburden plans must be submitted to the warranty holder through a “Notice of Alteration” prior to the installation of the overburden. By the terms of the warranty, overburden (for example, a ballasted solar system) that is installed without following the Notice of Alteration process, grants the warranty holder the option of voiding the warranty. When the Notice of Alteration process is followed properly, the presence of overburden does not void the warranty, but any overburden-induced damage (damage caused by movement of a ballasted system), is not covered under the warranty - and if that damage is extensive enough, it may allow the warranty holder to void the entire warranty on the basis of the damage.
In addition to the above, warranty holders do NOT allow 100% ballasted solar systems on mechanically attached roofs or on roofs that exceed the warranty holder’s individual slope allowances. When a 100% ballasted system is used on these roofs - under the mistaken belief that ballasted systems won’t void the warranty - the opposite result can happen.
The last caution to make about ballast is that no flat roof is perfectly flat. All flat roofs have undulations that create low spots. Earlier in the Q&A session, I mentioned the weight of ponding water. This live-load weight can be overlooked and/or underestimated when calculating the capacity of the building to handle the weight of a ballasted system.
What are some of the trends you are seeing in PV array mounts and fasteners?
Traditional mounts are usually supplied with a built-in membrane flashing. As such, mounts with TPO from one manufacturer are generally not acceptable for use with a TPO roof from another manufacturer. Sometimes, the building owner does not know anything about the membrane on the roof. This has created demand for universal mounts that can be used on any roof, regardless of the membrane/surface. At OMG, our Universal 7 and Universal 11 mounts meet this need and can be installed on any low-slope roof.
We are also seeing thicker insulation on new construction projects, which means longer screws are required to reach the deck below the insulation. At OMG, we have had this situation well in hand for some time as some of our fasteners are available in lengths up to 24-inches.
We also hear about non-penetrating mounts. These are mounts that are just adhered to the roof cover – usually a TPO or PVC membrane. We have not introduced this style of mount because of the extremely limited situations where they can be used. Because of billowing (explained above) non-penetrating mounts should never be used on mechanically attached roofs. In fact, we believe that installation of a non-penetrating mount on a mechanically attached roof to be extremely dangerous. They should also not be used on roofs with slopes greater than ½- in 12-inches because of the mount’s inability to handle static shear force over time. There seems to be a lot of misunderstanding about the acceptable uses of this kind of product and they wind up on roofs with higher risk characteristics for that style of mount. Many building owners are interested in this style of mount because they believe that penetrating the roof is detrimental to roof performance or the roof warranty. As a roofing fastener company whose screws are very likely to be holding the roof in place to begin with, we know that adhering a mount to the roof cover is a very risky method for all but a few types of roofs. As noted above, the roof cover’s job is to keep weather and water out of the building envelope, not to support equipment or solar systems.
Are there still improvements and advancement that can be made in roofing products? If so, how is OMG working towards this?
There are always improvements to be made! On our Agawam, Mass. campus, we have an entire building devoted to new product development and innovation. Our product development engineers work every day to develop products that improve contractor productivity and enhance the roof system performance. Our PowerGrip Universal 7 mount, which was introduced last year, was developed in-house and is a great example of a product that can be easily installed on a commercial roof by both solar installers and roofing contractors.
We currently have over a dozen product initiatives underway in our product development area. These products cover all aspects of commercial roofing, not just solar mounting solutions. We promise to keep you and the entire market apprised of the innovative developments that will result from our efforts.
About Kevin Kervick
Kevin is the Solar Products Business Manager for OMG and joined the company in 2019. His responsibilities include developing and implementing a strategic plan for the company’s solar business, managing the Solar P&L, as well as growing the business with our National Solar Sales Manager, and solar-related product development.
The content & opinions in this article are the author’s and do not necessarily represent the views of AltEnergyMag
Comments (0)
This post does not have any comments. Be the first to leave a comment below.
Featured Product
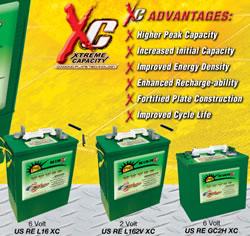