This challenge can be addressed effectively by means of an application-specific fire protection concept for stationary lithium-ion battery energy storage systems, such as the one developed by Siemens through extensive testing.
Fire Protection for Stationary Lithium-ion Battery Energy Storage Systems

Gerd Hülsen, Global Fire Safety Applications | Siemens Smart Infrastructure
Lithium-ion batteries offer high energy density in a small space. That makes them highly suitable for stationary electrical energy storage systems, which, in the wake of the energy transition, are being installed in more and more buildings and infrastructures. However, these positive characteristics have unique fire risks. This challenge can be addressed effectively by means of an application-specific fire protection concept for stationary lithium-ion battery energy storage systems, such as the one developed by Siemens through extensive testing. It is the first of its kind to receive VdS approval.
Each lithium-ion battery cell consists of two electrodes: a negative anode and a positive cathode. They are kept apart by a separator. Another essential component is the ion-conducting electrolyte.
However, this functional principle, while successful and generally safe, has designrelated risks. The battery cells are characterized by the presence of a large amount of chemical energy in a small space and a very small distance between the electrodes (separator layer typically ≈ 30 µm). At the same time, the electrolytes used are typically combustible or highly flammable.
For this reason, a battery management system (BMS) not only controls and monitors the state of charge at the cell and system level but also manages the temperature during charging and discharging. This ensures that the cells are kept within the operating range defined as safe.
Thermal runaway as a hazard scenario
Exceeding the safe temperature range can result in what is called “thermal runaway.” When this occurs, the energy stored in the battery is suddenly released, and within milliseconds the temperature rises to many hundred degrees. As a result, the electrolyte ignites or electrolytic gas explodes.
During a thermal runaway event, the electrolyte successively evaporates as the temperature climbs. This causes the pressure inside the cell to increase until the electrolyte vapors are released through a relief valve or a bursting cell wall. Without countermeasures, this results in an explosive gas-air mixture. All it then takes is an ignition source to cause an explosive combustion. In addition, a thermal runaway event in a battery system can spread from cell to cell, leading to a major fire.
Potential causes of thermal runaway can be found outside the battery cell or inside. In the first case, extreme external factors, such as a building fire, can cause the temperature in the battery to rise above the tolerance level. In the second case, an internal short circuit leads to a dangerous temperature increase. The short circuit could be caused by external mechanical damage or age-related separator failure due to dendrite formation.
Protection concept preventing the spread of thermal runaway
Tests performed at the Siemens Smart Infrastructure Fire Lab in Altenrhein, Switzerland on lithium-ion batteries with different types of cell chemistry (including lithium cobalt oxide, lithium manganese oxide, lithium nickel manganese cobalt oxide, and lithium iron phosphate) have shown that there are early signs prior to the actual thermal runaway event. One reliable indicator is electrolyte outgassing. As soon as electrolytic gas develops, a thermal runaway event is imminent. However, there is still enough time to automatically trigger suitable counter or extinguishing measures. This involves a two-pronged approach: First, introducing extinguishing agent in sufficient concentration into the room where the battery is located before the separator in the first battery cell fails. Second, initiating shutdowns through the battery management system in order to stop the spread of a runaway caused by overcharging or overload.
Rapidly flooding the battery room with the extinguishing agent prevents the formation of large amounts of an explosive electrolyte-oxygen mixture, thus reducing the development of an initial thermal runaway event and inhibiting the spread to adjacent battery cells. This eliminates the possibility of secondary fires and, through prolonged inertization, the potential for reignition.
Step 1: Detection by aspirating smoke detector
In step 1, an effective protection concept must offer not only reliable fire detection, but also very early detection of electrolytic gas. These challenges are met by aspirating smoke detectors (ASDs). Using dual-wavelength technology, they reliably detect electrical fires as well as electrolytic gases and vapors, even at high air speeds and low gas concentrations.
Aspirating smoke detectors continually sample air from the areas to be monitored and analyze it for smoke and gas particles. The air samples are drawn into the patented detection chamber through a network of pipes with defined sampling holes. In the detection chamber, an evaluation unit detects the particle size and concentration. It is able to detect even the smallest amounts of combustion and electrolytic gases.
Step 2: Extinguishing using inert gas
As soon as the detectors detect a fire or the presence of electrolytic gas, they must trigger automatic extinguishing by an extinguishing system. Since the use of water should be avoided for extinguishing around electrical systems and since water does not reliably reach hidden or obscured fires, the battery system is flooded with a gaseous extinguishing agent introduced through nozzles. The gas displaces the oxygen that sustains the fire, thus extinguishing even hidden and obscured fires. What is the most suitable extinguishing agent? Chemical extinguishing agents cannot be used in this application scenario because hazardous decomposition products may form or extended discharge may be necessary. Potential alternatives are three natural extinguishing gases: nitrogen (N2), carbon dioxide (CO2) and argon (Ar).
These differ in detail. Argon is a comparatively expensive noble gas used only for specialized applications such as metal fires. Carbon dioxide, the most effective of these extinguishing agents, is used primarily for inaccessible areas or property protection systems since it is harmful to humans in the concentration needed for extinguishing. For this reason, pure nitrogen is used as the extinguishing agent for lithium-ion battery storage systems, delivering excellent results.
Summary
Lithium ion batteries present unique fire risks. An application-specific fire protection concept combines very early fire detection with high-performance aspirating smoke detectors and inert gas extinguishing systems. Prompt discharge of the extinguishing agent prevents the formation of large amounts of explosive electrolyteoxygen mixtures, reduces the development of an initial thermal runaway event, inhibits the spread of such a runaway to other batteries, and eliminates the potential for secondary fires and reignition. Such a protection concept makes stationary lithium-ion battery storage systems a manageable risk. In December 2019, the “Protection Concept for Stationary Lithium-Ion Battery Energy Storage Systems” developed by Siemens was the first (and to date only) fire protection concept to receive VdS approval (VdS no. S 619002).
The content & opinions in this article are the author’s and do not necessarily represent the views of AltEnergyMag
Comments (0)
This post does not have any comments. Be the first to leave a comment below.
Featured Product
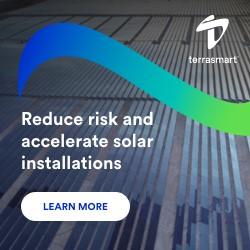