Electron beam welding has particularly outstanding properties: It can be used for joining the smallest components as well as for large parts. Vacuum solutions are indispensable for the application.
Electron Beam Welding in Vacuum
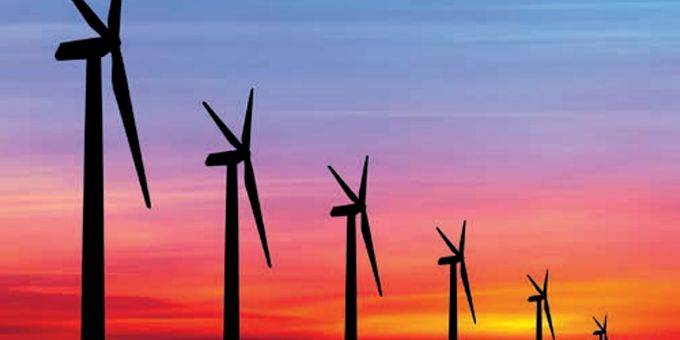
Article from | Pfeiffer Vacuum
Welding connects - the manufacturing of countless components is inconceivable without this joining process. While the history of welding dates back to the Bronze and Iron Ages, today highly specialized procedures are in use that offer certain benefits depending on the application. Electron beam welding has particularly outstanding properties: It can be used for joining the smallest components as well as for large parts. Vacuum solutions are indispensable for the application.
In electron beam welding, a beam of strongly accelerated electrons is focused on a workpiece via adjustable magnetic fields. On the surface of the workpiece, the electrons release energy precisely at the point of impact, where they heat, melt and vaporize material. The beam generation in the electron beam gun and the actual welding process in the welding chamber take place almost exclusively under vacuum at pressures in the high vacuum range (10-3 to 10-6 hectopascals). This is intended to prevent the electrons from being scattered by air molecules and to enable trouble-free and loss-free beam focusing on the workpiece.
Effective and precise
If you are not familiar with the technology, the first thing you have in mind is a welder with an arc conductor and a heavy protective mask who applies the filler metal to the material while sparks are flashing. So why should the process take Keeping air out during welding place in a vacuum? The electron beam process has several benefits. On the one hand, much higher velocities of up to one centimeter per second can be achieved. Also, the possible welding depth is greater, it can reach 30 centimeters. Since the process is not manually controlled, electrical adjustment of the beam parameters ensures very precise real-time control, ensuring first class components. Due to the high reproducibility of the welding results, the procedure is predestined for series production.
Electron beam welding also has a positive effect on the choice of component materials. This is due to the fact that the procedure achieves a very high local energy density on the one hand, but on the other hand there is only minimal heat input into the material surrounding the welding seam. In this way, combinations of a variety of different materials can be processed that could hardly be combined in any other way. Low heat also means low deformation. Since the surrounding material is protected during electron beam welding, metals with high thermal conductivity can also be welded. And finally, a vacuum also prevents unwanted oxidation of the welded workpieces, which can otherwise rapidly lead to problems during processing.
Why vacuum?
It is therefore not surprising that electron beam welding is always used when high precision and quality are not the only requirements. Companies in the automotive supplier industry, electrical engineering, medical technology and precision mechanics in particular make use of this procedure. In addition, there are sophisticated special designs, which are in demand in particularly specialized areas such as the aerospace industry and the energy and nuclear industries. Depending on the installation location of the operating site, electron beam welding systems can be specifically designed for one application or, as a universal machine, cover a wide range of applications and customers. Electron beam welding must take place in a vacuum so that the electron beam is not scattered by residual gas molecules. This increases efficiency because virtually all the energy is applied to the workpiece. Creating and maintaining a secure vacuum is therefore crucial for the entire process.
On the one hand, vacuum pumps have to maintain a permanent background pressure in the high vacuum range at the electron beam generator after the pumpdown process. The requirements for the pump configuration at the welding chamber are considerably more demanding. This can vary in size - depending on the workpiece - between a few liters and several hundred cubic meters. For all these chamber sizes, it is essential to achieve very rapid pumpdown times to a defined operating pressure, which is usually located in the upper high-vacuum range. Finally, the aim is to achieve the shortest possible cycle times so that the welding process does not become the bottleneck of the entire production process. One of the most important criteria for the selection of the vacuum pumps at the welding chamber is therefore a very high pumping speed in the entire relevant pressure range from atmospheric to operating pressure. In order to minimize downtimes, long maintenance intervals combined with high reliability are of the utmost importance for all pumps used.
HiPace turbomolecular pump at the electron beam generator
(courtesy of Steigerwald Strahltechnik)
Support for design
As a provider of highly specialized systems and solutions for a wide variety of vacuum applications, Pfeiffer Vacuum offers a comprehensive portfolio for electron beam welding. It includes high and medium vacuum pumps for evacuating the welding chamber and the electron beam generator, pressure gauges for atmospheric to high vacuum pressure, valves and flange components for connecting the vacuum components and leak detectors for locating leakages. In addition to components and systems, the specialist also offers support in the design of the complete vacuum system of an electron beam welding system to provide comprehensive support for users. This includes the dimensioning of all medium and high vacuum pumps including recommendations for any additional components required. The individual pump characteristics, losses due to piping, leakages and desorption effects of the inner chamber surfaces are taken into account in the design. Here the supplier relies on modern and specially developed calculation programs.
The right combination
Combinations of medium and high vacuum pumps are used to evacuate the welding chamber. The task of the medium vacuum pumps is to achieve a suitable fore-vacuum pressure in the welding chamber for switching on the high vacuum pumps. This is usually between 10-1 to 10-2 hectopascals. With the CombiLine series of Roots pumping stations, Pfeiffer Vacuum offers a complete standard series of Roots pumping stations that covers a wide range of achievable pumping speeds and ultimate pressures. For particularly demanding requirements, customer-specific pumping stations are designed, constructed and manufactured.
If the required fore-vacuum pressure is available, high-vacuum pumps are used. They generate and maintain the operating pressure required for welding, which is usually in the range between 10-3 and 10-6 hectopascals. Turbopumps from Pfeiffer Vacuum cover a pumping speed range from 10 to 3,050 liters per second (for nitrogen). The pumps are designed for high efficiency and flexibility; proven bearing systems offer the greatest possible reliability.
Turbomolecular pumps are the means of choice to generate and maintain the high vacuum at the electron beam generator. The initial evacuation is usually not subject to any time pressure. For the sake of maximum efficiency, medium-size pumps are usually used, such as the HiPace 300 or HiPace 700 from Pfeiffer Vacuum with a DN 100 or DN 160 intake flange. Individual rotary vane pumps or small dry backing pumps such as multi-stage Roots pumps are used as backing pumps when a hydrocarbon-free vacuum is required.
Measure and locate safely
For pressure measurement at the welding chamber and at the electron beam generator, combination vacuum gauges of type PKR (Pirani/cold cathode transmitter) have proven themselves in practice. Pfeiffer Vacuum offers the robust and reliable ActiveLine series. Compact Pirani transmitters - such as the Pfeiffer Vacuum TPR, also from the Active Line - are usually used to measure the fore-vacuum pressure of the high-vacuum pumps used.
For the correct operating pressure in electron beam welding, however, the tightness of the system is also decisive. For this purpose, an integral leak test is carried out, typically using the pressure rise method. In doing so, the system is evacuated to a defined pressure value. After that, all valves are closed. The pressure rise as a function of time then yields the integral leakage rate. Since internal leakages and desorption of surfaces can also cause a pressure rise and falsify the result, the chamber must be empty, clean and dry.
If the leakage rate exceeds the desired threshold value, the leakage must be located and repaired. Due to their high detection sensitivity, short testing time and easy operation, helium leak detectors are in high demand. The procedure is very simple: The system is evacuated, then helium is sprayed from the outside using a spray gun onto sealing points, weld seams and other potential leakage points. If there is a leak, the gas flows into the evacuated vacuum chamber and is sucked in and detected by the leak detector. With the ASM340, Pfeiffer Vacuum offers a powerful and universally applicable leak detector. The ASM 310 is also available as a portable version for mobile use.
Everything from a single source
Electron beam welding can help manufacturers in many industries to achieve greater efficiency in production, higher product quality and more rapid cycles. Although it is a marketable, established procedure in practice, there are special requirements that must be taken into account to ensure a secure, stable process. Users should therefore not only pay attention to first class machinery and plant with long service lives and low maintenance, but should also choose a specialized partner as their supplier who knows the specific requirements in production and offers tailor-made solutions that offer the highest degree of reliability. As an innovative company with a long tradition and over 100 years of experience in the design and construction of vacuum solutions, Pfeiffer Vacuum offers the necessary expertise to help users in all industries achieve success.
The content & opinions in this article are the author’s and do not necessarily represent the views of AltEnergyMag
Comments (0)
This post does not have any comments. Be the first to leave a comment below.
Featured Product
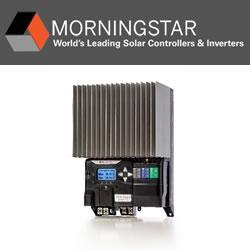