If you’ve installed solar on a steep pitched roof, working on a flat roof probably seems like a dream come true. There’s no hardware rolling down gutters, no fall protection lanyard tripping you, and you can use a wheeled cart to move equipment around the job site.
Choosing the Right Solution Solar on Flat Roofs – Ballasted, Attached & Hybrid
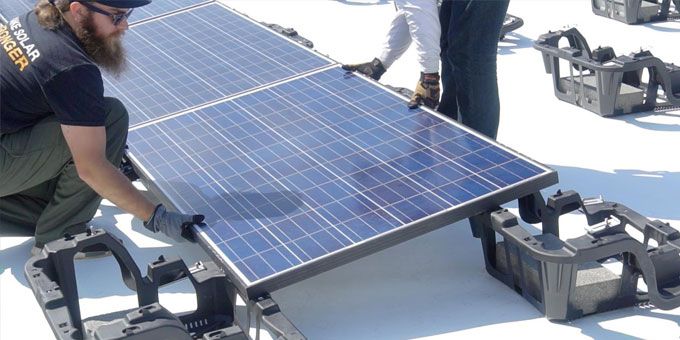
David Briggs and Jon Haeme | IronRidge
If you’ve installed solar on a steep pitched roof, working on a flat roof probably seems like a dream come true. There’s no hardware rolling down gutters, no fall protection lanyard tripping you, and you can use a wheeled cart to move equipment around the job site. What’s not to like?
And to sweeten the pot, designers of flat roof projects also have a lot more working space, so to speak. They can select from a variety of configuration and layout options to maximize performance, minimize material costs, or streamline construction.
Ironridge’s Flat Roof Attachment can be used with its BX ballasted system to provide additional support in high wind or seismic areas.
In particular, the options for structural design are incredibly broad. Designers can choose everything from using ballast weight for anchoring to building a superstructure above the roof for increased equipment clearance. Both of these options are simply unavailable on pitched roofs, where attaching directly to rafters, at fixed intervals, in a “flush mounted” configuration is practically the only viable approach.
But with all these freedoms also come additional responsibilities. Residential pitched roof structures have relatively small floor plans and are designed for simple uses (i.e. “dwelling”). As a result, residential structures rely upon inexpensive timber framing and are designed using the prescriptive methods in the International Residential Code (IRC). The result is a building with significant structural reserves and relatively straightforward options for modification. And, accordingly, adding solar to these structures often follows a similarly prescriptive approach and avoids the need for site-specific engineering.
Commercial buildings, on the other hand, have much larger floor plans, more varied uses, and higher safety requirements. Addressing these issues requires architects and professional engineers to analyze design choices and ensure compliance with the International Building Code (IBC), which is more open-ended and less prescriptive than the IRC. Typically, this analysis results in sturdy steel framing and concrete slab foundations, but not necessarily so. Design professionals pick from a phenomenally broad array of products and approaches, making every commercial building somewhat unique and customized.
Adding solar into this situation only adds to the complexities.
Solar on flat roofs is typically mounted at an angle relative to the roof, and this changes the shape of the roof surface and, thus, also changes the forces acting upon the roof. Solar arrays can increase wind pressures, change snow drifting patterns, and introduce new seismic interactions. In addition, the solar array can change the paths that these loads follow as they are transferred into the foundation. This is because there is an assembly of structurally-rated components translating the pressures on the surface of the solar modules into concentrated point-loads on the roof structure.
The IronRidge BX ballasted system offers the tightest inter-row spacing, fully maximizing power density.
The IronRidge BX ballasted system is ready to begin assembly as soon as they are unpacked from pallets, making for remarkably fast project timelines.
In other words, just as the commercial buildings itself was designed and built with more customized, less prescriptive methods, so too must the solar array be built. In the remainder of this article, we will walk through a simplified approach to addressing design questions for flat roof solar arrays that is logical, repeatable, and designed to serve the interests of your clients.
The simplest place to begin is with the available roof space. The open rooftop area with good sun exposure can be determined using satellite imagery in combination with a standard or solar-specific drafting tool. This will give you a basic outline of the available space with dimensions. If a high degree of precision is needed, there are also services that offer a library of high-resolution aerial imagery for a small fee.
With the available space defined, one can then consider the number of solar modules to fit into that space. Layouts should accommodate obstacles, their shadows, and required setbacks. Collectively, these are known as “exclusion areas,” and once they are defined, the remaining space can be filled with modules.
This is not as simple as “carpeting” the rooftop with solar modules, however. This is because solar modules on flat roofs are typically installed with a tilt relative to the roof surface, and as a result, they cast a shadow that must be avoided by the next row of solar modules.
Determining how many modules are needed and how steeply to tilt them depends upon the energy production goals of the project. This goal can be based on a range of factors from overall energy consumption of the host customer, to time-of-use electricity pricing and rates, to financial constraints of the host business or lending terms of local banks. For the sake of simplicity, however, let’s assume that we have a defined goal in terms of annual kWh of production.
If this goal is very high, you will be looking to maximize production per square foot of roof space (i.e. maximize “power density”). If this number is low, you may be looking to maximize production per installed kW of modules (i.e. maximize “specific yield”).
In general, low tilt angles (10 degrees or below) or dual-tilt configurations (East-West facing) maximize the power density of solar arrays. This is because these configurations reduce the shadow cast behind each solar module, allowing the next row of modules to be placed closely (as close as 10”).
If you’re still unable to meet the energy production goals with low-tilt configurations, it may be time to consider an elevated superstructures that is not limited by fire lanes and equipment setbacks. Though these superstructures are more expensive to design and build, they provide a number of advantages in terms of ease of access for roof maintenance and solar array inspection, in addition to the potential for fitting more modules on the roof.
In the opposite scenario, when there’s plenty of available roof space or a more modest energy production goal, you can use higher tilt angles and space rows of modules further apart to prevent inter-row shading and maximize specific yield. Wider inter-row spacing also has the benefits of lowering the distributed weight (Lbs/Sq-Ft) of the solar array and opening up more roof surface for maintenance access. The energy output of different tilt angles can be modeled in solar software tools, such as PVSYST, Helioscope, Aurora, and others.
Once an array layout is defined, you can then consider different structural support options. Typically, this comes down to a choice between ballasted or mechanically-attached mounts, with this determination then driving the final layout and dimensions of the array.
Ballasted systems use the weight of rocks or concrete blocks to resist wind uplift and seismic shaking forces acting upon the solar array. Typically, ballasted systems form a grid of interconnected rows and columns that is capable of (partially) transferring point loads on one module to multiple neighboring parts of the system. This has the benefit of reducing the required ballast weight in individual parts of the array, knowing that the forces can be averaged over a larger area. As a result, the weight of ballasted systems is most optimized in large PV arrays, where load transference is most effective.
The primary advantage of ballasted solar arrays is that they can be installed without penetrations into the roofing system. This allows the installation process to rely on simple mechanical assembly, rather than requiring a roofing contractor to seal penetrations. In fact, some ballasted products are ready to begin assembly as soon as they are unpacked from pallets, making for remarkably fast project timelines.
But ballast systems are not well-suited to all roofs. The required weight of ballasting can be as high as 8 PSF, depending upon the environmental loads combined with various site and safety factors. As well, many “flat” roofs actually have a slope as high as 7 degrees (technically, flat roofs are considered “low-slope” roofs because they are almost never truly “flat”). Ballast systems apply well to flat roofs that are below 3 degrees in pitch, but above that number, the required ballast weight can increase dramatically in order to generate the friction force necessary to resist sliding down the slope. A structural P.E. should determine if the roof structure and roofing material is suited to handle the ballast weight.
Mechanically-attached systems use positive attachment to the roof deck or structural members, rather than the weight of ballast, in order to resist environmental loads. As a result, an attached system can weigh as little as 1.5 PSF. Another advantage of mechanically-attached systems is that they can support a number of different racking configurations, enabling the use of longer spans between attachments, high tilt angles, and independent row placement. This is very different than the relatively fixed dimensions of a ballasted systems.
Combined, these benefits make attached systems ideal for smaller buildings where the roof structure has limited capacity for additional weight. As well, attached systems are well-suited to flat roofs with slopes of 3-6 degrees and roofs using standing seam metal cladding as the roofing material.
However, because mechanically-attached systems offer more choices and configuration options, it’s absolutely critical to ensure the compatibility of all components in the system. Do not assume that the capacities of individual components are the same as the capacity of the assembled system. The interface between components can introduce new limitations, and as a result, the overall system capacity is less than that of individual products.
Some manufacturers provide online design tools to determine the capacities and reaction forces of their components and assemblies. Armed with this information, a structural PE can confirm the overall system capabilities and correctly specify the length and number of screws required to attach this assembly to the roof structure below.
Finally, there are a number of sealing options for attached systems depending on whether the roof is made of a membrane, asphaltic material, or something else. Pre-formed membrane flashings are the ideal solution for waterproofing attachments on TPO, PVC, and other membrane materials, but other options include the “three-course method,” which employs reinforcing fabric and a compatible roof sealant and “pitch pans” which surround the penetration with a thick and permanent layer of waterproof material. Most solar installers will partner with a roofing contractor to seal attachments because the roofer can provide a warranty for the waterproofing performance of their chosen method.
Though ballasted systems and mechanically-attached systems are fairly distinct options, designers also have the ability to combine them. Most ballasted systems offer a compatible mechanical attachment method for dealing with high wind pressures or extreme seismic risk. So-called “hybrid systems” can offer a nice balance between the benefits of ballasted and mechanically attached systems.
But once again, the designer is faced with too many choices. Should I be quoting an attached or ballasted design? Will the customer prefer 100s of sealed penetrations in their roof or tons of concrete over their head? etc.
Ultimately, these questions raise some very fundamental considerations about what it is we’re selling when we propose “going solar” to a business. Knowing the factors that drive different design and engineering choices is not the same as knowing the factors that drive customers’ interests.
Businesses can have financial motivations, social and environmental commitments to uphold, or simply an opportunistic window associated with another construction project. Designing a solar array to address these types of needs is less straightforward than the steps we’ve described in this article, but it’s also potentially more powerful and valuable.
The best way to build this more advanced and refined skill set is through experience-- experience working with all the different flat roof mounting options, experience listening to the needs of customers, and most importantly, experience reconciling these two different worlds into a single proposal.
The more attention you pay to this process, the more you will be able to see how mounting system choices affect things that matter to customers, such as construction timelines, insurability of construction work, or near-term and long-term financial returns. And with this insight, you have the skills and tools needed to truly hold the responsibilities and benefit from the freedoms offered in flat roofs.
About David Briggs, VP Marketing
David is a solar industry veteran with more than a decade of experience working with module, inverter and racking companies. He is a passionate believer in understanding the details of products so that customers get clear answers to questions and effective solutions to problems.
About Jon Haeme, Senior Technical Support
Jon Haeme has spent much of the last three decades working with designers, contractors, installers and homeowners on their solar projects. Once a self-employed contractor, Jon currently volunteers time with the NABCEP PVA committee.
The content & opinions in this article are the author’s and do not necessarily represent the views of AltEnergyMag
Comments (1)
Featured Product
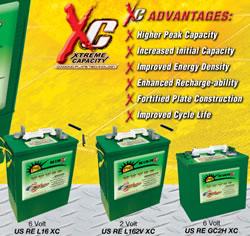