In this feature, Dr Doron Myersdorf, CEO of StoreDot, explores how AI might just hold the key to solving these issues, and the potential of this approach for the future of energy storage and EVs.
Unlocking the Future of EV’s with Ultra-Fast Charging and Artificial Intelligence
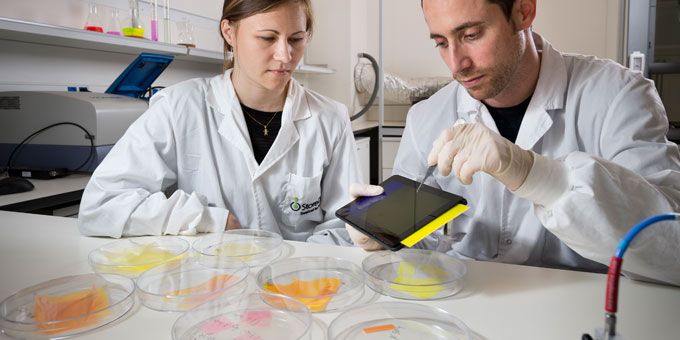
Dr Doron Myersdorf, CEO | StoreDot
By 2030, it is expected that the total sales of electric vehicles (EV) worldwide will surpass 30 million, and the cost parameters will finally come in line with the internal combustion engine. The EV represents a seismic shift in the automotive industry, and its potential impact on business and the environment is compelling. Today, the debates about adoption and longevity of EVs is rife and none more so than the potential performance of EV batteries. For scientists, many challenges still remain - from battery safety, to energy density, charging capabilities, and their performance within a car.
In this feature, Dr Doron Myersdorf, CEO of StoreDot, explores how AI might just hold the key to solving these issues, and the potential of this approach for the future of energy storage and EVs.
The stakes for the global battery market are incredibly high. Some predictions estimate that it will be worth over £250 billion per year from 2025, with the possible creation of 4 million jobs in the EU alone. These batteries, which are already essential for most consumer goods, will be even more vital for EV’s, with widespread adoption hinging on performance. Currently, no automotive or battery manufacturer can claim to offer an EV battery that charges as quickly as it takes to fill the tank of a traditional fossil fuel-based vehicle, nor can it offer the same range. For instance, the Volkswagen e-Up offers 99 miles at full charge, and the Tesla Model S 100D has a range of 335 miles at full charge. However, none of these vehicles can be fully charged in a matter of minutes. Today, a Tesla supercharging station will take 75 minutes to reach full charge, whereas SP Group, the largest EV network in Singapore, takes only half an hour.
The potential for lithium-ion batteries to solve some of these issues is enormous. However, there are a number of challenges with lithium-ion batteries that prevent a rapid charge - from the need for higher energy density, to preeminent rate performance and improved safety requirements. Overcoming issues in battery chemistry is a slow research process, largely based in iterative design of experimentation and systematic trial and error. Indeed, many new advancements fail before they make it to market. In R&D facilities such as ours, cyclers collect info from battery cells every second; this information includes important performance parameters such as cell temperature, real time resistance, operating voltage window, charge and discharge current, and swelling levels. The information is collected simultaneously from thousands of batteries with terabytes of data collected per experiment. As a result, the number of combinations for these materials is endless, and the number of experiments needed to test each combination is equally so. It is extremely difficult to solve with traditional statistical or manual methods.
Artificial Intelligence – Improving Battery Development
However, a holistic approach to employing data science in battery development could hold the key to solving such complex models. Artificial intelligence (AI) is a buzz-word today. Put simply, AI, or machine learning, can assess information and construct a mathematical model at a far quicker pace than the human brain. AI means that systems can automatically learn and improve from experience, without being explicitly programmed.
AI’s current and potential impact across multiple industries is staggering. In manufacturing, some of the world’s largest companies are already using AI with impressive results. For instance, Royal Dutch Shell’s Smart Manufacturing System uses AI to predict demand for oil, measure shortages of supply and analyse the correct mix/blends for an exact refining process. BASF and SAP have claimed to have automated 94% of its payment processing with AI. The application potential of AI is broad - from material design and synthesis, to experiment design, fault analysis and minimizing waste. With AI, smarter science with meaningful breakthroughs is possible.
The impact of this on battery development is not to be understated. The technology can browse through millions of records to describe the relationship between the measured data and battery parameters. As manufacturers, we can then use this to test millions of combinations of electrolytes, anodes and cathodes at any given time.
Scientists can not only evaluate batteries in development, but they can also learn from pre-existing batteries to achieve a better understanding of their performance behaviour profile and recommend the optimal solution. The ability to rapidly test limitless combinations, means that the ultimate formulation of the materials used to make the battery cell is reached far, far quicker. This dramatically reduces the number of experiments necessary, thus dramatically cutting development time, as well as significantly reducing development costs. For example, a team of 50 researchers working on a particular battery formulation, can save up to $1 million in R&D efforts per month by deploying machine learning capabilities.
At StoreDot, an initial foray into this technique returned remarkable results. For instance, for the first generation of our ultra-fast charging FlashBattery technology, with machine learning, our team discovered that a few simple changes in the formation could double the number of cycles of the battery under development from 300 to over 600 cycles. It was this discovery that inspired StoreDot to develop and dedicate an entire R&D group just to build our capabilities in machine learning. This dramatic result is now being applied to the next generation of our battery for EV’s. Ultra-fast charging presents a very complex issue – where in a traditional battery methodology, we would typically change only one component, but here we may need to change far more to reach the desired breakthrough. By combining innovative data science, powered by AI, with expertise in electrochemistry, cell structure, anodes, cathodes and electrolytes, far more complex conclusions can be reached.
Clearly, the benefit of machine learning during the R&D process is proving invaluable. However, this is not the only way in which AI can be implemented to advance EVs. A very different and intriguing application of machine learning would be to implement it within the EV operational software, to continuously monitor the performance and health of the battery, measuring continuous data, learning from it and circulating it back to improve product improvement. Moreover, by creating smarter batteries with embedded sensing capabilities, and with self-healing functionalities, the battery management system can be aware of their ‘state of health’ and can even rejuvenate battery cells or modules when necessary.
Ultimately, by enabling innovators to change more than one component at a time and analyse evidence quicker, they can reach conclusions that traditional statistical analysis cannot accomplish. This evidence allows for faster development cycles and the ability to overcome problems that might not otherwise be solved. For the adoption of EV’s, this capability is paramount in solving one of the biggest consumer barriers, ‘range anxiety’. By bringing battery charging times down by using machine learning technology, quite literally, the entire EV industry could be overhauled.
The content & opinions in this article are the author’s and do not necessarily represent the views of AltEnergyMag
Comments (0)
This post does not have any comments. Be the first to leave a comment below.
Featured Product
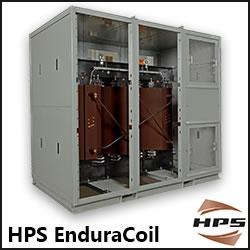